Downtime is without a doubt the least productive time in the lifecycle of an asset. When you're down, you're not making product. And when you're not making product, you're not making money. It's no wonder that for production managers worldwide, unplanned downtime is enemy number one—followed by scheduled downtime, which they'd like to see as short as possible (and would eliminate if they could). Next to eliminate would be process variability, which typically contributes to sub-optimal operation and off-spec production.
Despite the best of intentions and much hand-wringing, the process industries continue to struggle with poor availability, boosting total production costs by as much as 10% annually. Indeed, ARC Advisory Group estimates the average cost for plant downtime at $12,500 per hour; at some plants, of course, it's much higher. Research also indicates that those scheduled maintenance turnarounds may be longer than they need to be; a full 50% of all maintenance work may be unnecessary and 10% is actually harmful, according to the Gartner Group.
To begin to move the needle on asset utilization in a positive direction, plants need a combination of better process reliability, visibility, control and understanding. Across all of these dimensions, measurement instrumentation plays an outsized role. First, the correct choice of properly applied instrumentation can be a direct contributor to overall process efficiency and reliability. Second, instrumentation can help identify and diagnose a growing number of process conditions that, if left unaddressed, could escalate to a production outage. Third, wireless technology allows the cost-effective addition of new measurement points that can help fine-tune performance, as well as liberate stranded diagnostic information needed for a more complete picture of equipment health. Finally, the integration and presentation of diagnostic information in ways that can be quickly and intuitively understood—and acted upon—can help speed turnaround time, in no small part by helping to determine what maintenance activities need not be done at all.
Reliable Measurements Come First
At the North Star BlueScope Steel mini-mill in Delta, Ohio, challenging environmental conditions including high ambient temperatures, high vibration levels and red-hot chunks of slag took their toll on the plant's traditionally wired instruments, knocking out as many as a dozen temperature measurement points each week. As a result, each of the plant's several furnaces was out of commission at least once a week—with downtime ticking away at $500 per minute.
A total of 28 different measurement points, each with ten different wiring junction connections between the sensor and control system were subjected to vibration, moisture and heat, causing connection failures and changes in connection resistance that resulted in large measurement errors. Large chunks of slag could be ejected from the furnace—damaging cable or conduit up to 80 feet from the furnace. In addition, physical damage could occur each time the furnace top was opened to charge the furnace. Each week between 9 and 12 measurements would fail.
Switching to rugged Rosemount wireless temperature sensors that could reliably withstand the extreme temperature conditions—and remove wiring vulnerabilities altogether—eliminated the reliability problems, saving $200,000 in maintenance and repair expenses annually. More importantly, eliminating this source of downtime increased production capacity by nearly another full batch each day—and at $200,000 per batch, represented $50 million in "recaptured" production capacity.
At another extreme of challenging conditions, Perry's Ice Cream in Akron, N.Y., experienced persistent failures of its Coriolis and magmeter flow instrumentation caused by the plant's sanitary washdown procedures. Water repeatedly entered the flowmeter housings, causing the electronics to eventually fail. Since switching four years ago to Emerson's Rosemount Magmeters and Micro Motion Coriolis meters which are designed to withstand extreme operating conditions such as repeated washdowns, "I never have to worry about reliability," says Dave Foley, senior plant engineering technician.
Diagnostic Intelligence
Once your process instrumentation is no longer adding to downtime problems, you can start to enlist its detection and diagnostic capabilities to spot process conditions that may be early indicators of trouble. Indeed, Rosemount instrumentation comes equipped with a broad range of advanced diagnostic capabilities designed to help monitor the integrity of the instruments themselves as well as the health of equipment assets and related infrastructure.
These advanced diagnostics alert operators or other personnel to potential issues before they become disruptive. Dashboards and local displays deliver information in clear, concise language, conveying immediate understanding of the nature of any operational issue for quick resolution. And because the user-friendly interface is used consistently across a wide breadth of Emerson products, personnel can be more productive without having to learn a different interface for each type of instrument.
In the U.K., at the SSE Slough Heat and Power facility, Rosemount Analytical wireless conductivity transmitters are preventing process downtime by detecting changes in boiler condensate conductivity that could be caused by cooling-water leaks in the turbine's condenser. If left undetected, the contaminated feedwater causes hydrogen embrittlement of the furnace tubes resulting in tube failure.
The 80MW combined heat and power (CHP) plant had previously relied on manual sampling and laboratory analysis of turbine condensate. However, this method caused delays in detecting leaks and, as a result, the boilers sometimes had to be shut down while repairs were made.
"Emerson Smart Wireless conductivity transmitters allow us to continuously monitor the condensate extract lines," says Emma Wilcockson, electrical, control and instrumentation technician at SSE. "If we detect a change in conductivity, maintenance can be scheduled before the problem leads to an unplanned shutdown or damage to the plant."
Rosemount's workhorse pressure and temperature transmitters also pack an increasingly powerful set of process diagnostic capabilities. For example, the Rosemount 848T foundation Fieldbus Temperature Transmitter now features a new Measurement Validation Diagnostic, designed to detect temperature measurement and process abnormalities. By evaluating the variation in the temperature measurement, Measurement Validation can detect abnormalities related to degraded sensors, as well as electronic interference, corroded termination points, loose electrical connections and process upsets. By alerting the user to these issues through continuous online monitoring, degraded temperature sensors can be replaced before they fail or other preventive action can be taken—resulting in fewer process shutdowns, more efficient process operations and increased plant safety.
Product managers for the Rosemount 3051 Pressure Transmitter family recently announced an array of new capabilities designed to reduce both the total cost of ownership and the number of maintenance work orders, while improving productivity and safety. Power Advisory Diagnostics, for example, is a new predictive diagnostic tool that allows users to identify electrical loop issues, at the instrument or anywhere in the loop, before they cause a loss of measurement. Examples of these issues include water or corrosion in the terminal block or junction boxes, wiring problems or even a failing power supply. With simple three-step activation and guided troubleshooting, users of all experience levels can easily implement this diagnostic to help prevent costly outages and minimize time spent diagnosing and resolving the root cause of a measurement issue.
To improve accessibility to diagnostic information, the Rosemount 2160 Wireless Vibrating Fork Liquid level Switch continuously monitors device status and sends instrument health information to the control room via Emerson PlantWeb alerts. The alerts notify operators of conditions such as internal or external damage to the fork sensor, media build-up on the forks, excessive corrosion, and the potential effects of damage caused by over-heating. Customers can then implement a preventative maintenance program to reduce the number of field visits, maintenance costs, safety risks and unplanned shutdowns.
These enhancements join a roster of other process diagnostic applications derived from the dynamic behavior of process variables. Plugged impulse lines, for example, will drive down the standard deviation of a pressure measurement, and this pattern can be used to trigger an operator alert. Other applications include detecting furnace flame instability, wet gas flow and pump/valve cavitation. Emerson is even working on using differential pressure dynamics to detect incipient distillation column flooding. Operators typically steer well clear of flooding conditions, says Roger Pihlaja, a Rosemount principal engineer, but if you could manage to control the column just before it floods, you could increase production capacity.
More Measurements, Better Control
At a steel mill in Ohio, wireless measurement points have improved control and reduced downtime of the 80-in. hot strip finishing mill, boosting overall productivity by 5%. "We are building an infrastructure that opens up opportunities for more applications," says their operations manager. "The result is better information from difficult-to-reach areas of the mill, and this is helping our personnel prevent unscheduled downtime, meet customer quality requirements, and optimize productivity."
Recently, when the mill increased its product mix with a heavier and wider material, it required more run-out table cooling water to maintain the proper grain structure throughout the strip. Unfortunately, as the new product was being rolled the target coiling temperature could not be achieved. Manual valves used to scale the curtain water flow to the proper setting for each product could not be confirmed with flowmeters, since they were deemed too expensive and difficult to install in this congested environment.
Four Rosemount Annubar primary elements teamed with Rosemount 3051S Wireless Pressure Transmitters and an Emerson Smart Wireless Gateway were quickly and easily installed, and within 24 hours, the mill had the flow rates they needed. The flow information obtained from the wireless transmitters enabled them to fine-tune the sprays. Since then, coiling temperature rejects have been almost entirely eliminated.
Three other downtime problems were also solved with wireless instruments. A malfunctioning grease delivery system was providing inadequate lubrication of roll bearings, causing downtime and surface defects. A Rosemount 3051S Wireless Pressure Transmitter now raises an alarm if grease pressure drops or cannot be maintained, eliminating another source of downtime. The mill was experiencing work roll damage and subsequent downtime in the roughing mill due to coolant flow problems. Work practice changes, together with wireless pressure transmitters to ensure adequate coolant flow and pressure, resolved this downtime issue, too. And in the back-up roll bearing system, Rosemount 648 Wireless Temperature Transmitters measure inlet and outlet oil temperatures—flagging any temperature excursions so that brief repairs have now replaced lengthy outages.
Set Turnaround Priorities
In their quest to increase asset utilization, the process industries aren't just striving to head off downtime due to unanticipated problems, they're also lengthening the time between shutdowns for scheduled maintenance—and aiming to turn plants around as quickly as possible. Here, too, the process intelligence gathered by smart instruments and other field devices is helping make plant turnaround activities as efficient as possible.
Valero Energy Corp.'s Wilmington, Calif., refinery uses AMS Suite asset management software from Emerson to help make sense of data coming from its many production assets, including process and mechanical equipment, electrical systems, valves and instruments. "We can find out what's about to happen before it causes an upset," says Paul Chandler, senior instrument engineer.
But information gathered during the course of normal operation can also pay off at turnaround time. For example, through valve signature analysis enabled by the AMS Suite, Valero Wilmington discovered that "in the past we pulled many valves for maintenance that we didn't need to pull," Chandler says. In its latest turnaround, just 12 valves were pulled instead of a past average of 107. "In fact, it was almost a million dollar savings in just three turnarounds," Chandler says.
A faster turnaround that's less expensive, too? That's enough to make any production manager proud.
Latest from Pressure
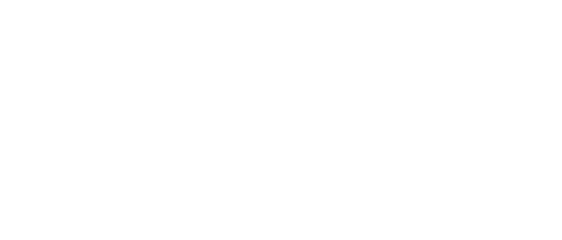
Leaders relevant to this article: