[sidebar id =1]Q: We have a venturi flowmeter with 3-in. flanged pressure taps and flanged chemical seals with capillary tubes in a 44-in. vertical pipe (Figure 1). The fluid is hydrocarbon (polymeric) gas. The problem is that the chemical seal diaphragms often need to be cleaned because of buildup from the gas that includes methane, ethylene, etc., with sand in it. We would like to have continuous flow measurement even during cleaning.
I think a cleanout line could help but I don’t know how to put it in. Another idea is to install a second transmitter on the existing flange taps without any isolation valve. For both transmitters (old and new), we need valves because we want to use the new one while the old one is out of service for cleaning.
I’m told that we can’t use nitrogen for purging because of safety or pressure buildup reasons. I’m also told that ultrasonic isn’t a suitable selection? Finally, is an equalizer is necessary? I don’t think so.
Rahim Rahim / [email protected]
_______________
A: Using a combination of flanged 3-in. nozzles as pressure taps and flat diaphragm chemical seals is rather unusual. Assuming your figure is correct, my recommendation for the installation is shown in Figure 2:
[sidebar id =2]Install full-ported 3-in. ball valves for blocking. Also install an equalizer valve if you want to be able to quickly check the zero. This valve can be small.
Move the flow transmitter directly to the venturi to minimize length of the capillary tube.
Insert a flushing ring below the chemical seal (Figure 3). It can also be used as a bleeding ring to release the pressure before cleaning.
Purge with nitrogen at a rate of 1.0-2.0 SCFH using a constant differential purge meter to keep the hydrocarbon gases and sand out of the nozzles. Nitrogen is safe, pressure buildup is negligible, and natural gas always has some nitrogen in it anyway. Still, if there is some valid reason for not using it, select another gas.
Thermally insulate the whole assembly.
Add a clamp-on, Doppler, ultrasonic flowmeter for backup when the venturi is being maintained. It’s cheap and is likely to work if the pipe is not lined, the acoustic coupling is good and the ultrasonic beam is focused to the average point of the velocity profile. I have not used one for pipe sizes above 24-in., so check the suitability for your 44-in. size with suppliers such as GE.
For specification forms, see my handbook.
Béla Lipták / [email protected]
_______________
A: A sure way to damage diaphragn seals to clean them like you do; it is not recommended. The idea is to prevent buildup by using a purge flow, but the selection must be compatible with the process gas to prevent contact by the polymeric gas with the diaphragm seals (e.g. nitrogen, hydrogen). The purge gas flow is small (approximately 1 to 1.5 SCFH). This is an insignificant flow compared to the gas flow in a 44-in. venturi. You will have to check with the process engineers on the selection of the purge gas.
[sidebar id =3]Purging of differential pressure (DP) measurements have been done for a very long time in refineries and chemical industries. It is not an unusual arrangement, and has been in use for more than 60 years. Please consider the fact that bleed/flushing rings are supplied by companies such as Emerson, Wika, Endress+Hauser and Yokogawa for diaphragm seal transmitters.
I’ve used purging on both DP flow and level measurements for more than 35 years. However, I’m not allowed to provide our company’s standard installation details. I suggest that you ask the instrument company that’s supplying your transmitters.
You should be using a bleed ring (Figure 3) as well as the main isolation valve to the process. The ring is fitted between the diaphragm seal and the isolation valve to the process connection on the venturi, and the purge flow is connected to this bleed ring.
The purge flow needs to be constant and at a low value, so it will not affect the accuracy and stability of the DP measurement. A constant differential relay or a restriction orifice should be used on each diaphragm seal.
The use of isolation valves to the process connection does not affect the accuracy. You should always have a means of isolation for instrumentation. The bleed ring is also useful for “bleeding” off the pressure to the diaphragm before removing the transmitter for maintenance (if required).
If you can’t find a compatible purge gas, don’t use DP flow. Consider a time-of-flight ultrasonic flowmeter.
[javascriptSnippet]
If the polymerization of the gas on the diaphragm is due to cooling, apply heat tracing to the process connection to prevent fouling of the diaphragm seal. If insulation of the venturi is sufficient to prevent fouling of the diaphragm, then that’s good: it’s a simpler installation. However, heat tracing will not affect the DP measurement. Heat tracing around DP flow (and other measurements) is a very common application that’s been used for many decades. There are many cold-climate applications around the world where, without heat tracing, nothing would work. Some of the applications I’ve had to deal with have a specification of -50 °C ambient. In Alaska, the specification is -60 °C.
I don’t understand what you mean by “...need some special condition for the fluid.” If you have a homogenous gas, then a transit-time ultrasonic measurement will work.
Simon Lucchini / [email protected]
_______________
A: Find out when the product becomes viscous or freezes, as you may be able to use steam-heated jackets or insulation. If the flowmeter has errors, it could be that the product is being pumped in an uneven manner and/or the product viscosity changes.
The connection should be a valve like you show but without tubing fittings, then a tee, then two valves, one with tubing, the other with the purge or cleanout fluid. This one also needs to be a plain valve with no tubing connections, so you periodically manually rod out or clean the connection area.
Alex (Alejandro) Varga / [email protected]
_______________
A: It appears you have chemical seals at the pressure taps. These are probably 4 in. (10 cm or so) in size. Here, a full-size ball valve is perfectly possible without compromising the pressure measurement, but it might not be allowed for safety reasons. A manifold of two large ball valves with a bleed valve between them to prove full isolation would be expensive, but might be required. I worry about how the chemical-seal diaphragms are cleaned. These are easily damaged.
It’s hard to imagine an effective gas purge with the size and length of the pressure tap nozzle. You would have to review the flows and the possible purge gas supply to see what makes sense. If you have a source of effective solvent, consider a periodic wash-out, but I have no idea how successful that would be.
An inspection of the installation will probably disclose that the chemical seal is colder than the flowing gas. That would explain condensed “stuff” on the diaphragm. Condensation will be reduced and might be avoided if removable, insulated and perhaps heated boxes are installed around the pressure taps. Educating the field people about the reason for the boxes will probably be necessary (don’t ask me how I know about that).
Cullen langford / [email protected]
This column is moderated by Béla Lipták, automation and safety consultant and editor of the Instrument and Automation Engineers’ Handbook (IAEH). If you have an automation-related question for this column, write to [email protected].
Latest from Flow
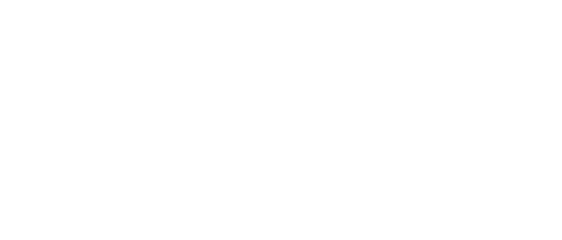
Leaders relevant to this article: