[embed width="80" height="90" class="left" thumbnail="http://www.controldesign.com/assets/images/voices/bacidore.jpg?r=16458"]http://www.controldesign.com/assets/images/voices/bacidore.jpg[/embed]Mike Bacidore is the editor in chief for Control Design magazine. He is an award-winning columnist, earning a Gold Regional Award and a Silver National Award from the American Society of Business Publication Editors. Email him at [email protected].
“We can bring up to 35% savings in energy consumption and increase productivity by up to 20%,” said Alexandre Perrat, drives marketing director for Schneider Electric, speaking at CONNECT 2016 this week in New Orleans.
“We have one of the largest drives portfolios in the market,” added Jean-Pascal Riss, Schneider Electric’s marketing director for Altivar Process. “In 2014, we shipped 1.7 million drives.” More than half of those drives were for use in process-industry applications.
Industry’s first services-oriented drive
“Altivar Process is the first services-oriented drive,” said Riss. “It is a smart connected product providing business optimization.” Processes can be optimized using decentralized application expertise, enabled by dedicated control in real time, he explained.
Altivar Process drives provide flexibility for water/wastewater, oil & gas, mining and food & beverage applications, and they’re available in wall-mounted and floor-standing designs. Available from 1 hp to 1,100 hp, these low-voltage drives are ready to use or fully customizable. They’re tested and validated before shipment, and are modular and compact for smaller footprints.
“The Altivar Process drive is cybersecurity certified at Achilles Level 2. It’s a complete application asset, not just a VFD.” Schneider Electric’s Alexandre Perrat explains the benefits of the company’s new services-based drive at CONNECT 2016.
“The Altivar Process drive is also cybersecurity certified at Achilles Level 2,” explained Perrat. “It’s a complete application asset, not just a VFD. We can record and log the energy and visibly display the energy consumption on an hourly, daily, weekly or monthly basis, so they know if the energy consumption is increasing or decreasing based on the working conditions. It can diagnose when a gearbox is exceeding a preset torque level or when a pump is operating outside of parameters.”
Optimize process performance and energy consumption
The drives can provide instant reaction if pump efficiency drops, thanks to embedded pump monitoring. Notification of critical operating points can be executed without additional sensors, and the drives can be integrated with pressure, flow and level control including compensation of flow losses. For example, a pump curve embedded in the drive, combined with flow-measurement and energy-measurement sensors, lets the drive understand how the motor will respond best and then optimize performance.
The data allows users to monitor key performance indicators (KPIs) related to energy and process performance. Local and remote access to energy use and customized dashboards means energy use is visible anywhere, any time, on PC, tablet or smartphone. The drive contains a web server, giving access to the information through the IIoT, the Internet or mobile asset management applications. “We can readily integrate the drive’s intelligence into Modicon M580, PlantStruxure PES or Foxboro Evo,” said Perrat. “We’re able to make sure this data is available to every level of the automation infrastructure. The idea is to have this tested architecture enable transparency across the infrastructure.”
Thanks to standardized FDT/DTM and ODVA technology, the drives also can be integrated into PLC environments, and they’re supported by predefined Unity Pro libraries.
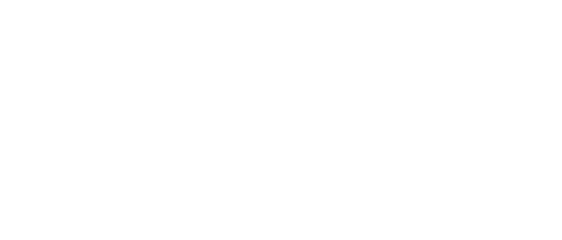
Leaders relevant to this article: