Neural nets improve flame detection
In August 2013, President Obama issued an executive order with the intent of helping improve petrochemical safety policies. Since then, nearly two and a half years later, there have been more than 400 petrochemical accidents, large and small.
What these incidents tell us is that despite the best intentions of government and the industrial community, safety is an issue that isn't going away anytime soon. There is new hope on the horizon, however, because the latest generation of gas and flame detection systems is smarter than ever with artificial intelligence, can provide a multi-sensory layered strategy to safety monitoring, and is certifiable to comprehensive international safety standards.
Neural network intelligence
Biological neural networks were the inspiration for artificial neural networks (ANNs), which are mathematical models. In ANNs, an interconnected group of artificial neurons process information, and actually change structure during a learning phase. That process allows the network to model complex relationships in the data delivered by sensors in a quick search for meaningful patterns.
Figure 1: Looking back to the 1940s, computer researchers were inspired by the human brain when they developed the first conceptual model of an artificial neural network.
Looking back to the 1940s, computer researchers were inspired by the human brain (Figure 1) when they developed the first conceptual model of an artificial neural network. Their work focused on solving certain kinds of problems that are easy for humans, but difficult for machines or computersāotherwise known as pattern recognition.
Applying NNT to safety monitoring
Fast forward to the present, and youāll find there are now a variety of applications of neural networks, some of which are at work in the newest generation of gas and flame detectors. With the application of neural network technology (NNT), which is based on ANN, these detectors operate, in essence, with an artificial intelligence capability.
The breakthrough advantage with NNT-enabled gas and flame detectors is their ability to learn. They learn through a type of apperceptive process, which means the comprehension or assimilation of something such as a new idea can then be related in terms of previous experiences or perceptions. NNT-enabled devices operate similarly, and are much like a human mind in the way that it enables a person to recognize a face from the distant past. The brain, for example, facilitates recognition by matching a face with an image stored as a memory.
Just like the human brain, NNT-based gas and flame detectors each have thousands of pieces of data stored in their memories from hundreds of gas leak, non-gas leak, flame and non-flame events that have been observed in the past. Such detectors have been trained through NNT intelligence to recognize an actual gas leak or flame based on that data, and they make decisions about whether they're detecting an actual gas leak or flame, even if they haven't seen that exact pattern in the past.
Multi-sensory layered safety monitoring
Taking NNT a step further, because no single sensing technology can detect every gas threat or every flame hazard, there is a new strategy emerging in safety monitoring. What if you combined multiple gas and flame detection technologies together, and then layered them where they fit best in terms of their reliability in each unique plant layout?
Gas and flame detection sensing technologies, if you think about it, all mimic the senses of the people who invented them. Catalytic bead detectors āsniffā gases, infrared and optical type sensors āseeā gases and flames, and ultrasonic sensors āhearā gases. What if some of these detectors behaved more like peopleāreacting based on their intelligence (NNT enablement) and retained past memories?
Layering sensor technologies throughout the plant where they fit best in terms of their reliability achieves a human sensory chain of plant defense against hazardous gases and flames (Figure 2). This human sensory model builds a chain of defense to protect industrial plants, helping process and plant engineers add layers of protection that increase overall system protection and reliability, which includes avoiding false alarms.
Figure 2: Layering sensor technologies where they fit best in terms of their reliability builds a chain of defense, helping process and plant engineers add layers of protection that increase overall system protection and reliability, which includes avoiding false alarms.
SIL-rated detectors
When plant safety engineers go one step further and choose detectors certified to Safety Integrity Levels (SIL) for safety instrumented systems (SIS), they have again added another layer of safety. Certification to these standards plays a valuable role in effective industrial gas and flame detection.
Normative standards establish minimum requirements for the design, fabrication and performance of these safety devices as necessary to maintain protection of personnel and property. ISA 84.01 was enacted to drive the classification of SIS for the process industry within the United States, as well as the norms introduced by the International Electrotechnical Commission, IEC 61508 and IEC 61511.
Together, these standards have introduced several specifications that address safety and reliability based on optimizing processes for risk. IEC 61508 is a risk-based approach for determining the SIL of safety instrumented functions. Unlike other international standards, IEC 61508 takes a holistic approach when quantifying the safety performance of electrical control systems: The design concept, the management of the design process, operations and maintenance of the system throughout its lifecycle are within its scope.
Adopting next-generation gas and flame detectors with neural network technology, taking a multi-sensory layered approach to plant protection, and specifying SIL-rated detectors can all help increase plant safety, prevent catastrophic accidents, and reduce false alarms. Plant safety engineers who take these three steps have embarked on the newly enlightened path to protecting people, equipment, facilities and business operating in hazardous process industries.
Latest from Safety Instrumented Systems
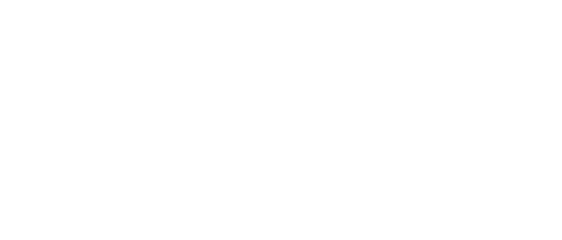
Leaders relevant to this article: