At the 2016 Automation Summit in Las Vegas, Siemens announced winners of its 11th annual Customer Excellence Awards (CEA). Since 2006, the CEA’s have recognized the achievements of Siemens’ customers and partners who have exemplified superior business practices using Siemens technologies and solutions. Past award winners include small, mid and large scale companies representing everything from a sugar refinery to a fertilizer manufacturer to an oil and gas company. The awards provide an opportunity to shine a spotlight on companies demonstrating their leadership and innovation in leveraging software and hardware to successfully automate and digitalize their manufacturing operations.
“Manufacturers are looking for new ways to get to market faster while increasing quality, efficiency and flexibility,” said Raj Batra, president of Digital Factory, U.S. “The answer can be found in technologies that bring together the real and virtual worlds of product design, production design and all phases of the manufacturing process. Our annual user conference is a great venue for Siemens customers to network and share experiences on their transformation to digitalization and the Customer Excellence Awards allow Siemens to recognize the accomplishments of our customers.”
Siemens 2016 Customer Excellence Award winners include:
Ford Motor Company, an American multinational auto manufacturer headquartered in Dearborn, Mich.met with Siemens because the company wanted to gain engineering efficiency with concentrated support of a single automation platform. Ford was seeking a technology partner to support a global engineering structure, especially with more expertise in the powertrain environment. Ford’s goal was a complete IP65 Distributed Controls package to reduce its footprint of production lines and ultimately provide better line of sight and reduction of traditional control cabinets.
[sidebar id =1]Working with Siemens, Ford drove IP65 hardware development and standard architectures allowing seamless distributed control and easy re-balancing of its production lines. Ford created global standards for hardware and software in more than 30 of its manufacturing facilities which allows for standardized training for both the engineering and maintenance workforce. In addition, Ford Motor Company’s collaborative and focused efforts have resulted in Ford Powertrain deploying a successful customized global learning program complete with performance-based objectives, customized curriculum, plant-matched equipment simulators, and a better prepared maintenance staff.
Constellation Brands, an international maker and marketer of wines, beer and spirits, headquartered in Victor, N.Y., sought to expand the capacity at their brewery in Piedras Negras, Mexico to meet the growing demand in the U.S. market for their Corona, Modelo Especial and other beers.
They partnered with Siemens to supply the automation platforms for all areas of the state-of-the-art brewery through various OEMs and partner channels realizing both engineering and operational efficiencies. The project included a wide range of components from Totally Integrated Automation, including Simatic PLCs, PCS7, HMI Panels, SCADA software, industrial networks, LV VFDs, motor control centers and motors, process instrumentation and associated industrial services. The first two phases of the expansion were completed ahead of schedule with additional phases in progress.
Jack Daniel Distillery, a producer of Tennessee Whiskey, located in Lynchburg, Tenn. is the top selling American whiskey in the world. Jack Daniel’s was experiencing an increase in demand for its offering, so the company took steps to ensure it could efficiently increase production to meet the rising demand at the Lynchburg facility. Jack Daniel’s decided to first upgrade the computers and operator interface on the existing distillery to Siemens PCS 7 APACS+ OS to improve the reliability, performance and functionality. Jack Daniel’s then built a new distillery to provide additional production capacity while also providing flexibility for the future. The implementation of the PCS 7 Simatic batch and Route Control, by Siemens certified solution partner Cross Integrated Systems Group of Knoxville, Tenn, provides more transparency, simplifies changes and increases production flexibility to develop new recipes and products. The use of the Siemens preconfigured SiVaaS virtualized computer system architecture reduces system maintenance while supporting future expansion. The addition of wireless mobile clients empowers the operators by providing the production information while in the field to make real-time decisions. The production process in the new facility supports repeatable and reliable production, providing a high quality product with more throughput for the entire process. The system reports help provide the critical information to the process, maintenance and production teams which helps them further optimize the process.
The 2016 Automation Summit, with more than 60 breakout sessions led by Siemens customers and partners and 14 hands-on training sessions, was a user-based conference with more than 600 participants and focused on “Community. Experiences. Productivity.” The event is led by two Siemens divisions in the U.S. – Digital Factory and Process Industries and Drives.
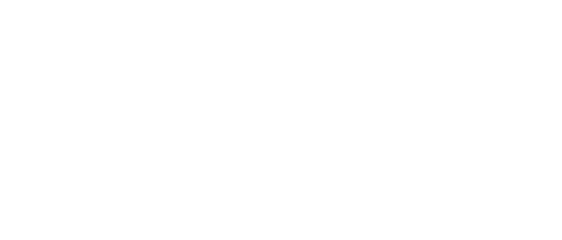
Leaders relevant to this article: