Emerson debuted a first look at DeltaV digital twin delivered through a software-as-a-service (SaaS) subscription model this week at the 2017 Emerson Global Users Exchange. Built as an extension of Emerson’s already established and successful cloud project engineering platform, the new subscription service delivers a virtual reference system for customers to optimize their operations.
“It’s not just about the technology, it’s about how to deploy it,” said Jamie Froedge, president, process systems and solutions, Emerson Automation Solutions. “We help customers deploy, measure and show the benefits.”
[sidebar id =1]
Emerson first released cloud engineering services in 2014, building a foundation that has now transformed hundreds of capital projects across the globe. The service brought engineering configuration and virtual testing online instead of on-site, eliminating costly travel requirements, as well as hardware, storage, and services costs. Cloud engineering has cleared the way for agile work processes and non-linear project methodologies, shortening overall project schedules and significantly reducing capital project execution costs.
“We used to do it on location—we’d fly there, maybe rent a space, build out the system, test it, fly in the customers and do acceptance testing. Then go to the site and do it all over again,” Froedge said. “Now, we have performed thousands of systems virtually. The next evolution is to use it as an operations reference system—a high-resolution digital twin as a subscription service.”
The service is designed to unlock a customer’s operations potential by providing a more flexible landscape for maintenance, reliability, education and performance services.
Virtual FAT to digital twin
“Users log on and we collaborate in a secure engineering environment to engineer and test the system,” Froedge said. “Then we extend it into the operations phase, so we can use the virtual system for system maintenance, reliability, education and performance improvements.”
The digital twin makes it easier to monitor and improve operator performance, deliver operator training with simulation, manage alarms, optimize production optimization, and implement advanced process control. What might take a year or two in the plant can be done ahead of time, and ready to go on day one.
“We break down the barriers between the project and operational stages,” Froedge said. “Instead of waiting until the system is running to train operators, add advanced control and optimization, do reliability optimization and develop work practices, we can do it ahead of time on the virtual system.”
In 2018, DeltaV digital twin will be offered as a subscription service to make it easier to deploy changes, tune loops, and implement advanced control. “You can deploy and test changes safely, while the plant continues to run,” Froedge said.
As an up-to-date reference of the control and safety system, the digital twin also serves as a repository and guide for future project planning. Froedge said, “Customers often wish they had an up-to-date reference version for new sites and expansions, to not have to reinvent the wheel. Now they will have it.”
Better displays for screens of any size
In June, DeltaV Mobile brought the DCS to the small screen. Now DeltaV will use HTML5 to make the same screens available across essentially all platforms. “DeltaV v14 now includes an all-new operations experience we call DeltaV Live,” said Peter Zornio, chief technology officer, Emerson Automation Solutions.
DeltaV Live Operator Interface offers a more intuitive HMI to empower the digital worker. “We took human-centered design practices and years of display building experience to develop new display building tools and dramatically reduced the number of hours needed to make an effective, functional display,” Zornio said. “We showed the displays to operators and the Center for Operational Performance, and developed them to get the best situational awareness, with progressive disclosure and an operator-configured watch list.”
DeltaV Live helps today’s digital worker make the most of every action by introducing more ways to visualize information as well as providing new capabilities for operators to augment their environment on the fly. Ultimately, digital workers will be able to make faster, better decisions in complex situations.
By building this modern offering on the latest technology, Emerson sets the stage for taking advantage of the wide variety of desktop, tablet and phone platforms, giving users more flexibility to choose the right platform or device for what they are doing and where they are working. Regardless of the device, digital workers will have intuitive and familiar displays to make decisions to run their plants safely and more effectively.
“Being HTML5, it’s cross-platform, so you use the same technology and get the same displays for mobile workers,” Zornio said. “It’s a leap forward for DeltaV.”
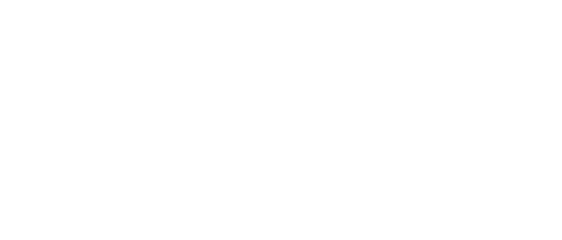
Leaders relevant to this article: