Globally, FMC has more than 100,000 employees and is the world's largest provider of products and services for individuals undergoing dialysis. "The facility provides peritoneal dialysis (PD) solutions," said White. "It's basically ultra-pure water used to help with renal failure therapies. We provide a complete solution for people with chronic kidney failure from dialysis machines to dialysis clinics and in-home care products."
“The existing, legacy equipment and some of the new equipment used a variety of controllers from several different vendors. The final system design using PCS 7 controls could manage the facility with just two controllers," said White.
[sidebar id =1]
The team selected Siemens PCS 7 with Simatic Batch for the process areas, and TIA Portal systems using S7-1500 PLCs for the secondary processes. White and Jeff Clark, PhD, lead systems integration engineer at Cross, described the implementation at Siemens Automation Summit 2017 in Boca Raton, Florida. They focused on the design and startup using Simatic Batch, the S88 approach, GAMP 5 and FDA validation methods. “It was a new experience to me,” White said.
Business needs define requirements
"When we started, we needed to determine what our business needs were, so we leveraged the existing system and created a baseline for the control process," noted White. "It needed to be robust, reliable, modular, standardized and compliant with FDA regulations. The process must be available 24/7 with redundant systems and data integrity. The equipment cannot go down and we cannot lose any data. We also needed to include the capability that, as we grow, we have the ability to bring new equipment and processes online without shutting down any processes to do it.”
As a pharmaceutical company, Fresenius Medical Care is required to follow 21 CFR Part 210, 21 CFR Part 211 and 21 CFR Part 11. "As we move away from paper documentation, we wanted to make sure we could use electronic signatures and all the data recording in places as required in 21 CFR Part 11," said White. "All this had to be completed within aggressive cost and milestone requirements and at a fixed deadline for start of manufacture."
When selecting the control solution, White worked with Cross Integrated Systems Group and did a comparison of the options available. "We developed a list of pros and cons of each scenario," said White. "As a result, there were a number of things that drove us to go with Siemens. One of the reasons was based on a shortened development time. There was basically no customization required; we used the standard function blocks and faceplates. Another thing important to use was robust security."
The partnership with Cross, which provides control system design, system integration and engineering services, was very helpful in making this project successful. "A Siemens solutions provider in a variety of industries, Cross helped us from the start in developing the system business requirements," said White. "They aided in development of P&ID schemes following ISA standards, detailed design specifications and qualification documentation. They also supported qualification protocols from FAT through OQ."
How did we get there?
White stated “There were a variety of PLC controllers involved from several manufacturers. Our group did not want six or seven control solutions to solve the problem."
Cross and Siemens were able to develop a hardware design to bring all of this equipment together. "The solution includes three major I/O panels that were designed and built and included two S7-410 controllers," said Clark from Cross. "Scalance networking was used along with fiberoptics due to the large facility. We followed a Siemens-provided network architecture. It was a big help following Siemens' plan, and it worked well without needing to reinvent the wheel."
The design also added one engineering station (ES) and runs two, redundant servers for OS and Batch. "We are currently running six OS clients and a process historian/information server," noted Cross. "This takes care of all the data integrity needs."
Two important components the team kept in mind while completing this project's development cycle were the Good Automated Manufacturing Practice (GAMP 5) and the S88 standard. GAMP 5 includes requirements and specifications, review and approval, implementation methods and testing phases. S88 describes various models, which integrate well with PCS 7 and Simatic Batch.
"Documentation is a big part of GAMP and critical in a pharmaceutical operation," noted Clark. "Literally everything needs to be documented. We brought in all the information and developed the I/O list, control modules and graphics all with the documentation. A detailed design specification defined the required sequential logic for the process, and the documents were written for understanding without requiring a PCS 7 programming background."
The batch solution
"The PD solution in the facility is well suited for a batch application, so it made sense to utilize Simatic Batch from Siemens," said Clark. "A total of seven recipes were configured and were used for PD solution batching, a filling product solution, and cleaning and sanitization of equipment—a very important part of the process."
Simatic Batch also worked well for meeting the requirements of compliance with 21 CFR Part 11 and operational efficiency. "It reduced manual entries and has the capability to expand and utilize formulas for various products," continued Clark. "Meeting standards, less paperwork, built for expansion over time, and reducing the work necessary for different formulas were all realized benefits of this system."
Similar to the hardware design specifications, general batch design specifications were developed from business requirements. "Detailed procedure flowcharts were developed in specifications used to configure recipes," said Clark. "These detailed documents were designed in such a way that they closely mimicked what the operator would see on the batch screen. This made it easy for the personnel during qualification and testing to compare what was happening in the flowchart to what was actually happening in the batch recipe during the run."
The use of electronic signatures is a major part of compliance with 21 CFR Part 11. "One of the great things about Simatic Batch is that it allows for E-sigs at all stages in the recipe," said Clark. "Electronic records are also available in Simatic Batch, and provide a ton of information. Custom reports were also generated through collaboration between Fresenius Medical Care, Cross and Siemens. This reduced some of the massive amount of batch information down to a more usable, daily level, for example, for management use."
Days instead of weeks
"So how did all this help get us to FDA approval?" asked White. "Because we built it all on the front end, we didn't have to come back and recreate the documentation. We leveraged all the information created during the detail design phase and FAT. For example, with hardware configurations and device communication—critical items—it had already been written, we just needed to reformat it to complete all our test phases again."
The details were so well documented, the testing took only days where it could have taken weeks to complete. "We turned the system over to some of our technicians after training, and the IQ took about five days instead of what would take four to six weeks," said White. "We repeated the same operation when we got into our OQ; we used all the documents created during the design phase after reformatting them for the qualification testing." The graphical and logical presentation of the process information including batch, sequencing and interlocks in the PCS 7 HMI was very effective for our operators. “99% of the time we find the information we need directly on the operator screen and almost never have to use the engineering system to answer our production and operations needs,” said White. “I have used the PCS 7 HMI graphics and as training tools to help operators learn the process and how to operate the plant”.
The benefits of this project methodology were many, commented White. "Shorter development and start-up time was a big one," he said. "The hardware and software made it efficient to build graphics, logic and recipes. Both the PCS 7 and Simatic Batch feature improved specification creation and reduced qualification effort, and they are well suited to meet FDA regulations. As the process is run, the historical trend data collected will provide efficient evaluation of the process for improvements."
Latest from Home
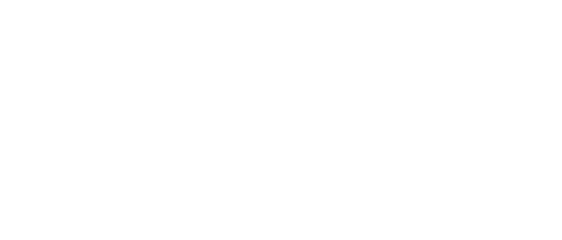
Leaders relevant to this article: