Microprocessors may look like tiny, fragile bits of plastic and metal—at least until they power up and run software. However, they and their many layers, circuits, substrates and coatings are born in processes using severely toxic gases and volatile chemicals, which require at least as much careful handling and process safety as the most dangerous oil and gas, chemical, mining or other heavy-industry applications.
Few engineers are more aware of the critical need for toxic gas monitoring systems (TGMS) than us at Hallam-ICS, an engineering and control system integrator in Burlington, Vt. A member of the Control System Integrators Association (CSIA), we design, build and test turnkey control systems and panels for manufacturing and research labs at major universities, such as MIT, Harvard, Cornell and many others, and has done projects as far away as Singapore, though our main focus is the eastern U.S.
Our TGMS niche is the safe use of hazardous production and research materials required for developing and manufacturing semiconductors. Many of these hazardous gas materials, if not stored, handled and used properly, can expose workers, equipment, facilities and the environment to many dangers. These gas hazards include potential exposure to toxics, highly toxics, fire, explosion, corrosives and oxygen depletion. Many of these materials provide no warning properties—such as odor thresholds or visual vapors—prior to loss of life or significant damage.
For example, a common "dopant" gas such as the hydride arsine (AsH3) has an American Conference of Governmental Industrial Hygienists time-weighted, average-threshold limit value (TWA-TLV) of only five parts per billion. Silane (SiH4) is another hydride gas used in these facilities, and it's pyrophoric (self-ignites in air), yet is so unpredictable that it may delay "self-ignition" until forming a vapor cloud and causing a large explosion. Along with toxic, flammable, pyrophoric, corrosive and reactive gases, one must also monitor ambient oxygen breathing levels in inert gas storage and imaging areas. Oxygen-depletion sources in these facilities are also very common, and include many inert gases such as nitrogen, helium, argon, krypton, xenon—all without warning properties.
Detect and address
Because each of the hazardous gas (targets) is applied from within different "gas families” (e.g., hydrides, halogens, mineral acids, flammables, etc.), each has unique gas properties and safe exposure limits. As a result, each TGMS design must begin with a risk assessment (RA). A complete list of all hazardous gases (including inerts) and how they're employed (stored, delivered and handled) must be obtained to determine how best to safely detect a gas leak for each individual gas target.
Due to the many different gases used—and different gas targets required with many different properties—safe gas detection is challenging and requires using multiple gas-sensing technologies to safely detect each. Gas-monitoring technologies are carefully placed in ambient breathing zone areas, in gas delivery system exhausts, and in tool-processing-equipment exhausts. Ambient breathing sensor locations must consider each room’s area airflow and the properties of each gas, such as vapor density, to determine ideal mounting heights.
Detection technologies vary widely, for example, employing extractive or diffusion gas sampling, chemical cassettes, electrochemical, catalytic bead, infrared (IR) and/or Fourier transform infrared (FTIR) instruments and sensors. Other key considerations include cross sensitivities within gas families and known interferences from other gases and vapors, which can cause negative sensor responses and sensor poisoning.
For example, we may use chemcassettes with chemically treated tape to extract samples from possible leak points. Continuous vacuum (extractive) monitoring (via Teflon sample tubes) drag samples through or bounce them off the chemically treated tape, which discolors in relation to the gas target and calibration for the tape, and can be measured in parts per million (ppm) or parts per billion (ppb). We also use FTIR that can detect leaks for many different gas targets, including flammable vapors. The challenge is selecting the proper detection methods to best address each gas target.
Beyond the fact that facility gases may change frequently, semiconductor researchers and manufacturers, and their TGMS, are also facing lower required detection limits for sensor ranges and lower alarm limits. In general, Hallam-ICS begins with the ACGIH's TWA-TLV levels or short-term exposure limits (STEL), ceiling limits as established by the ACGIH and/or NIOSH. Also, OSHA's PEL “Z” tables now reference, include and recommend using these levels when appropriate. Most facilities alarm at 1 TLV time-weighted average value if there's a leak.
Requirements for various gases and mixes are determined by several organizations, including the U.S. Occupational Safety and Health Administration, National Institute for Occupational Safety and Health and ACGIH, which publish standards and rules for gases every year. ACGIH also publishes handbooks on TLVs and biological exposure indices (BEI), which include values updated annually based on the latest research. These values consist of time-weighted averages of the gas limits that a healthy person can tolerate eight hours per day and 40 hours per week over a 20-year career. Finally, Hallam-ICS also complies with National Fire Protection Association and Compressed Gas Association requirements, as well as International Fire Code, International Building Code and International Plumbing Code, known as the "ICC Family."
Hallam-ICS also subscribes to guidelines and best practices published by SEMI; references FM Global, and is a member of the Semiconductor Environmental Health and Safety (SESHA) organization, along with obtaining annual updates of TWA-TLVs from the ACGIH. We also work with clients to share industry experience and best practices adopted by similar clients to harmonize and coordinate practices.
Automation aids analysis
Even though its TGMS platforms are standalone systems used primarily for emergency shutdowns and providing real-time alarm data locally and remotely to aid and protect emergency response teams—similar to fire alarms that aren't incorporated in regular process control—Hallam-ICS employs continuous diagnostics for all its monitoring technologies to ensure safety system availability. In addition to using supervised wiring, TGMS architectures use failsafe (upstream gas-off ) logic approaches for critical gas targets via hardware and software.
Many sensor technologies used today, such as electrochemical sensors, continuously degrade over time, so they need periodic testing. We handle the problem of failure on demand, which means continuous monitoring to determine when they've become compromised. As a result, we test all sensors with actual target gases or surrogate gases as part of validating the installation and continuing throughout the maintenance lifetime of the safety system. The other challenge is that projects at university research labs frequently change. Managing change of different gases requires updating the RA to identify any new exposures to system safety. Each change, similar to a fire alarm system, must be reviewed and retested to validate any revision.
Hallam-ICS equipment also uses Ethernet and Internet protocol (IP) networking, and ControlLogix control platforms with Safety Integrity Level (SIL) 2 capability from Rockwell Automation (www.rockwellautomation.com) to provide diagnostics, I/O and remote I/O functions. ControlLogix's function-based platform helps users develop RAs and safety requirement specifications (SRS) for their application or facility. Each facility also has its own unique cause-and-effect matrix.
Fab project process
Hallam-ICS works with semiconductor manufacturers that produce microprocessors and other electronics. We're selected to deliver their TGMS because we can meet their fast-track schedules, while still providing the attention to detail needed for their life-safety systems, in-house design, programming and commissioning. "To meet project schedules and maintain progress, we staff our teams with experienced, in-house project management, TGMS code experts, control system engineers and commissioning engineers," says Kristian Montenegro, senior project manager at Hallam-ICS. "Our team forms tight connections with construction managers, and holds progress meetings to make sure final systems meet expectations. These systems are typically based on Allen-Bradley ControlLogix PLCs and GE Cimplicity front-end, while also using Honeywell gas detection equipment."
Montenegro adds that Hallam-ICS also institutes "zero defect" policies, and develops in-house, web-based design tools that provide automated error checking and generation of PLC code and commissioning documents. "This improves overall quality, and enables us to meet aggressive schedules despite design changes," he explains. "All project milestone dates are met, and we deliver thoroughly commissioned systems to insure a safe and reliable manufacturing environment."
Many small, high-tech companies are embedding new capabilities and components in their products. However, they can't always manufacture their own electronics, and this is where these semicondcuctor manufacturers come in.
Designing for safety
Figure 1: Clauses 8 through 11 of the IEC 61511-1 standard for functional safety of safety instrumented systems (SIS) are the most applicable to toxic gas monitoring systems (TGMS), and their flowchart section details a step-by-step approach for determining TGMS requirements and if a safety integrity level (SIL) would be required for any safety instrumented functions.
Source: Hallam-ICS and IEC
To design, build and maintain TGMS that keep users and applications safe, Hallam-ICS employs strategies and safety instrumented system (SIS) standards, most notably IEC 61511-1 (ANSI/ISA-84.00.01-2004) for functional safety of SIS in the process industries (Figure 1). For us, safety means thoroughly understanding the hazards and risks users face. This requires methodical, detailed information gathering to determine the exact dangers, and working to eliminate them. [The white paper, "Fundamental Design Requirements of Toxic Gas Monitoring Systems (TGMS)" by Blais is free to download.]Another challenge is that many materials our users deal with are cross-sensitive, so a gas leak in a family such as the hydrides might be detected by an ambient breathing zone sensor that handles two or three gases. But, unless there's a FTIR detector there, the system won't know which gas tripped it, but those are very costly. This kind of leak usually means shutting down all similar upstream gas family sources, but if it can be detected in the cabinet, exhaust or manifold, then the user can shut down just the one source they know is a problem.
IEC 61511-1 provides a useful framework for the hardware and software that SIS need, including TGMS. Meanwhile, the International Society of Automation covers SIL levels, which help Hallam-ICS develop its own failsafe and shutdown systems, and determine which safety layer and safety functions are needed by each TGMS based on the RA performed for each user and their particular application.
We suggest using the IEC 61511-1 framework and the methodical, step-by-step approach developed and outlined by the harmonized and accepted ANSI/ISA-IEC accepted standard to help determine: identity of all possible, gas-related hazards; severity of each gas-related hazard; and the possibility of an occurrence for each gas-related hazard. We have very capable people that have been doing this for a long time, but we still have to be somewhat old-fashioned and by-the-book, carry out tasks very methodically, and have great attention to detail.
Jim Blais, senior controls designer and engineer at Hallam-ICS, designed its TGMS solutions for 20 years, and retired in December. He can be reached at [email protected].
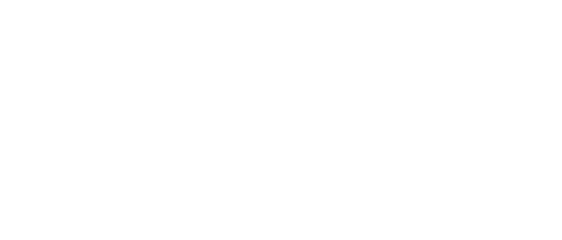
Leaders relevant to this article: