Standards deliver the interoperability promised by OPAF and NAMUR
The well-known "building block” metaphor may be slightly overused by now, but it’s never been more true than illustrating how the FieldComm Group’s protocols and technologies form the base of the two latest openness and interoperability efforts in the process industries. This is because the use of FDI, FOUNDATIONFieldbus, WirelessHART and HART can more easily provide long-sought, often-stranded information from field devices to systems across the enterprise, which is the ultimate goal of openness and interoperability.
Meet OPAF and NAMUR
A revolutionary approach to openness is being developed by the Open Process Automation Forum (OPAF). It aims to develop an open, interoperable “standard-of-standards” specification. In the two years since it was launched, OPAF has grown to 116 members, including end users, system integrators, suppliers and supporting organizations. Throughout the past year, OPAF’s Business Working Group drafted its 36-page “OPA Business Guide” that describes a value proposition and business cases for open process automation (OPA).
NAMUR Open Architecture (NOA) provides Industry 4.0 monitoring and optimization by using a reliable IT infrastructure in centrally located plant areas, that does not impact core-process and deterministic control or proprietary interfaces. Source: NAMUR
During the same period, OPAF’s Technical Working Group developed the OPAF Technical Reference Model (TRM), Part 1—Technical Architecture that defines interfaces between devices, but doesn’t dictate what’s in those products or interfere with their intellectual property. The TRM covers regular DCSs and supporting PLCs, HMIs, I/O and Ethernet-based networks, as well as advanced controls and manufacturing execution systems (MES).
TRM is expected to deliver openness and interoperability in three areas: On-Premise OT Data Center with real-time advanced computing (RTAC) and distributed control framework (DCF); OPA Connectivity Framework (OCF), which is a real-time, universal service bus like Ethernet using an OPA-standard communication protocol like OPC UA; and Distributed Control Nodes (DCN) that are configurable I/O for input/output processing, regulatory control, logic solving and application hosting. If successful, OPAF’s architecture will result in radically different control systems.
The second major openness effort, NAMUR Open Architecture (NOA) is scheduled to be released as an IEC standard in 2021-22. NOA addresses openness as an evolution, that is, without impacting what already works. NOA is trying to maintain the benefits of existing systems by layering NOA’s monitoring and optimization (M+O) applications alongside existing field-level, basic automation, MES and ERP levels. These applications cover M+O functions like dispatching, alarm management, advanced process control (APC), and Industrie 4.0 device management, and essential M+O functions like advanced analytics, historian, central HMI, production network simulation, reliability center and scheduling.
FieldComm Group base for openness
“FDI is the next step of device management. It provides a unified description, and allows for field communication standard independent device management using one tool. It separates device representation from the underlying communication technology, and lays the groundwork for digital twin representation of the devices,” says Thoralf Schulz, board chair of the FieldComm Group and group vice president of R&D and technology in the Industrial Automation Control Technology division at ABB. “Making these device models available through OPC UA makes the device models available, not only to control systems, but also to further applications as formulated by NAMUR and OPAF. FieldComm Group is working actively with the OPC Foundation to make this a reality. The currently ongoing work in standardized semantic identifiers, as defined by international standard IEX or exl@ss, will further strengthen this. It enables not only the data access, but makes it possible to develop standardized applications.”
In a typical process application with Open Process Automation (OPA) standard devices, OPA's Technical Reference Model (TRM) includes On-Premise OT Data Center with real-time advanced computing (RTAC) platform and distributed control framework (DCF); OPA Connectivity Framework (OCF), which is real-time, universal service bus like Ethernet running OPC UA; and Distributed Control Nodes (DCN), which are configurable I/O for input/output processing, regulatory control, logic solving and application hosting. Source: OPAF
Peter Zornio, FieldComm Group board member and CTO at Emerson Automation Solutions, adds that, “FieldComm Group technologies could and should play a major role in enabling OPA and NOA solutions. Regardless of whether OPA, NOA or other open architectures are adopted, users aren’t planning to replace their installed and operating field and measurement devices, such as all the control valves running in their facilities today. The vast majority of these components are running some combination of HART or FOUNDATION Fieldbus, and that huge installed base isn’t going away.”
Zornio explains that whichever openness strategy is employed—OPAF’s redefined, orchestrated control architecture or NAMUR’s added digital transformation layer—both plan to build on the installed base of existing devices. “No one’s talking about ripping and replacing existing field devices,” he says. “Openness and interoperability will be achieved using established standards and easier connectivity.”
Standards unlock data
Lukas Klausmann, senior marketing manager for industrial communication at Endress+Hauser, agrees that the FieldComm Group has spent years standardizing data in all kinds of field devices, which paves the way for NAMUR and OPAF efforts to also unlock data from field devices in a standardized way. “FieldComm Group enables suppliers like Endress+Hauser to launch new tools based on NOA that can cover a wide range of installed bases, and turn data into useful plant information,” he says.
For example, Endress+Hauser recently launched an analytics app that shows a dashboard of the installed devices in a facility, and uses a new approach based on work by FieldComm Group to standardize device data. “Endress+Hauser Analytics app shows serial numbers, tags, manufacturer names, product code, and often asset type as well,” he explains. “We’re also about to launch the Endress+Hauser Health app that works in accordance with NOA to immediately display health status, performance history, root cause and remedy in case of diagnostic events on mobile devices. Both of these app tools are web-based, so dashboards can be displayed on tablet PCs and smart phones.
“In the same way, NAMUR and OPAF are seeking to increase device connectivity, so more field data can make its way to cloud services and mobile devices. All these capabilities are made possible by standardization, which makes sure each device shares its data in the same way. FOUNDATION Fieldbus is standardized on its H1 and High-Speed Ethernet protocols, as well as HART, and FieldComm Group compliance-tests devices to help ensure they can connect without issues to provide field data. In the future, FDI and OPC UA are going to have more standardized interfacing, which will make it easier to connect and access field devices. The potential here is huge because about 90% of Endress+Hauser field devices are already equipped with a communication protocol, such as HART, FOUNDATION Fieldbus, Profibus/Profinet or EtherNet/IP. Standardizing their data will mean that ripping and replacing isn’t necessary.
FDI and OPC UA to the rescue
Zornio adds that two FieldComm Group technologies can enable any OPA and NOA strategy. “FDI is a tool that can configure any device as long as an FDI package is provided. It helps integrate existing and new field devices, which aids everything from configuration to data access and modeling. Meanwhile, WirelessHART is key to fulfilling NAMUR’s vision because it provides easy installation for the incremental sensors that NAMUR talks about adding on top of the controls layer,” he says.
Schulz explains, “Existing HART and FOUNDATION Fieldbus installations make the data from the devices available. FDI adds the system and communication standard that makes independent device management a reality, and available to all HART and FOUNDATION Fieldbus devices, as well as to other protocols like Profibus and Profinet. This is done without needing to replace existing devices, but is still expandable for advances in future devices. Adding OPC-UA and a standardized device representation, independent of the device standards, provides standardized access, and ensures that any advanced applications and capabilities are equally deployable for existing installations and newly evolved installations. This ensures the interoperability targeted by NAMUR and OPAF.”
Scott Saunders, president and CEO of Moore Industries-International, says, “OPAF and NAMUR are attempting to do at higher data exchange levels what FieldComm Group technologies have been doing for years at the sensor, device and DCS levels, which are Layers 0, 1 and 2 of the ISA 95 control information hierarchy. FieldComm Group does a wonderful job of promoting and endorsing open industrial standards for measurement and data exchange at Layers 0, 1 and 2. OPA is the same concept, but it consists of platform-
agnostic data exchange and analytics using open standards and off-the-shelf software components.”
Saunders adds that FieldComm Group can help interoperability initiatives like OPA because its planned DCNs will serve as gateways between Layers 0, 1 and 2 and higher levels. This is where continued support for its open technologies like HART Internet Protocol (HART-IP), WirelessHART, FOUNDATION Fieldbus and FDI can be most beneficial. “The future of process control and automation is big data and analytics, but you can’t take advantages of those without accessing data from Layers 0, 1 and 2, and getting it to the cloud and corporate wide area networks,” explains Saunders. “OPAF has already outlined a number of requirements for its standards, and I understand that HART is going to be part of OPAF’s physical platform requirements.”
Moore has been developing a gateway that supports open protocols like HART-IP, Modbus TCP/IP and HTTP via Ethernet, which lets users take process data from field devices and more easily make it available to higher-level control and information systems. This HES HART-to-Ethernet gateway will communicate with as many as 64 HART field devices, and allow immediate access to real-time HART variables and diagnostics over Ethernet.
Zornio concludes, “FOUNDATION Fieldbus, HART, WirelessHART and FDI are available today, but they’re also set up to meet future needs. The best avenue for field instruments and devices to achieve openness and interoperability is FieldComm Group technologies.”
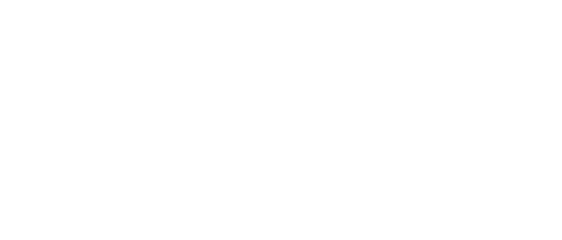
Leaders relevant to this article: