Task force to release new Power over Ethernet wiring standard
Ethernet and IP-based systems have had limitations to prevent use as field sensor networks for moving data packets around a facility. Now one of those limitations—the power-to-the-field hurdle—is about to be overcome. The IEEE P802.3cg 10 Mb/s Single Pair Ethernet Task Force expects to release a new standard describing power over Ethernet (PoE) twisted-pair wiring option within the year.
This new standard is specifically designed for harsh environments and will support short-reach (15 m/50 ft.), high-noise installations (automobiles). It also will support long hauls of up to 1,000 m (3,280 ft.), while being able to survive certain fault conditions.
The long-haul, point-to-point configuration will support a trunk up to 1,000 m with 200-m spurs and a maximum of 12 connectors. Echo cancellation to 300 m is incorporated to provide increased reliability along the spurs. To ensure suitability for industrial and automotive environments, the standard also supports optional physical layer powering techniques, including addition of a power injection partway along the network.
The estimated power dissipation is less than 50 mW, which means that with the addition of protective diodes, a 1.0 V peak-to-peak signal will be compatible with intrinsically safe (IS) operation. Additional energy management features include support for both quiet and standby modes. Target bit error rates (BER) are in the range of 10-9 with support for message failure mechanisms to detect when a packet fails to reach its destination.
Key variables proposed for the IS implementation include maximum output voltage Uo 17.5 V; maximum allowed supply voltage 14.3 V; functional supply voltage 13.2 ± 0.3 V; short circuit current Io 380 mA; minimum output voltage 9.6 V; minimum device voltage 9.0 V; maximum device current 55.6 mA; and maximum available device power 500 mW (www.ieee802.org/3/10SPE/public/Nov2016/index.html).
These values are quite different from the normal 24 V for process instrumentation, 12 V for CAN bus (automotive), and 40 V for PoE in the IT environment. However, with 0.5 W/55 mA at the remote end of the network (a typical transmitter today is less than 20 mA and closer to 10 mA), it should be possible to power three or four devices per link, which coincidentally was what the original Foundation fieldbus IS spur was capable of supporting.
One challenge with any new system is the same problem faced by the various process fieldbus systems: the installed base of field devices. However, because the average home-run cable in a plant is approximately 300 m (1,000 ft.), especially with the trend toward distributed interface rooms, it should be feasible to use this technology with existing infrastructure.
I can envision distributed I/O options for various protocols, similar to the connector blocks we used to replace terminals when migrating to Foundation fieldbus in 1996, that reuse the existing multiconductor cables for the home-run signals. ODVA is watching these developments closely, as are, I'm sure, many other protocol trade organizations.
The new IEEE 802.3cq standard makes it foreseeable that the death of the traditional field junction box will soon be upon us. With 10 Mb bandwidth for arguably four signals, there will not be any challenge in accessing the full range of device diagnostics or similar capabilities for an installed HART or fieldbus device, while also making it possible to use true Ethernet devices with access to faster updates or raw data for further analysis and understanding of the process than is possible today. Of course, Ethernet to the field device foregoes the multi-drop capability. However, for some applications (perhaps vibration or other high-frequency, high-value signals), this may be just what's needed.
This is sure starting to sound like the Open Process Automation Forum's concept of the distributed control node (DCN) without the local regulatory control capability—but that’s just software that could be added to the field junction block I/O connector microprocessor.
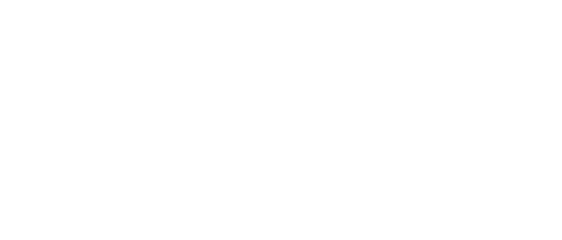
Leaders relevant to this article: