For many years, end users and their engineering contractors have been installing a quality measurement system (QMS) such as a sampling, mixing and analyzer system (SMAS) for immiscible liquids, including oil and water. It is a tenet of process measurement that any analyzer or sensor is very capable of measuring only a single-phase sample. In fact, most practitioners assume that using two analyzers on one stream for immiscible liquids will solve the measurement problem. It doesn’t—it just requires a double SMAS, each with its own level of uncertainty.
This article describes a new SMAS, referred to as SmartMix®, that uses a novel approach to improve multiphase measurement.
Crude oil sample conditioning systems must comply with international quality measurement standards, such as ISO 3171 and API 8.2, if they are used in the delivery and sale (custody transfer) of crude oil. Almost all crude oils contain basic sediment and water (BS&W), with the water usually having a high concentration of salt and the basic sediment composed of various impurities. The question is, how much BS&W is passing unmeasured?
A more critical question is, “Are the current quality measurement systems in use today fit-for-purpose?” A QMS that is not fit-for-purpose is a double-edge sword. First, if the measurement is inaccurate, salty water will be bought or sold at the price of crude oil, resulting in a potentially significant financial exposure. Second, the amount and composition of these salty waters and complex impurities have detrimental effects on the process operation due to corrosion, fouling and upsetting the mass and energy balance of the system.
Figure 1: Oil & Gas Measurement (OGM) Ltd.'s integrated flow testing and calibration laboratory includes a small multiphase flow loop (SMPFL) and large multiphase flow loop (LMPFL) for oil-water testing, supported by a liquid meter calibration loop (LMCL) and high-performance computing (HPC) capability.
As many of us in the hydrocarbon and chemical processing industries know, SMAS—particularly mixing—requires attention to every detail if we are to minimize lost revenue.Mixing difficulties
Many of the technologies involved in mixing are not well understood. In the hydrocarbon industry, mixing is a critical component for liquid custody transfer of crude oil. Poor mixing practices can lead to inaccurate measurements with high levels of uncertainty, resulting in losses totaling millions of dollars per year for typical petroleum refinery or pipeline operations.
Significant loss reductions are available for plants that mix well. Consider a 250-million-barrel-streaming-per-day (MBSD), or about 1,500 m3/hr, petroleum refinery receiving crude oil with a nominal 2% by volume water content for a crude price of $65/barrel. Compared to 100% mixing efficiency (ME):
- 90.0% ME leads to losses of about US $10 million per year (current ISO/API requirements),
- 95.0% ME leads to losses of about US $5 million per year (upper limit of current technologies),
- 97.0% ME leads to losses of about US $3 million per year (standard capability of SmartMix), and
- 99.8% ME leads to losses of about US $213,000 per year (optimized capability of SmartMix).
Genesis of a new technology
Some existing SMAS did not seem to provide a homogeneous mixture for truly representative sampling of two-phase immiscible liquid streams. We thought it should be possible to do better.
Figure 2: Two views of Oil & Gas Measurement (OGM) Ltd.'s small multiphase flow loop (SMPFL) at the University of Cambridge Magnetic Resonance Research Centre show the nominal 2.5-in. pipe passing through the magnetic resonance imaging (MRI) unit used to characterize the prototype SmartMix device.
Current industry practice is to use vertical pipe runs for mixing and sampling immiscible liquids, especially when the stream velocity is less than 0.5 m/s. It is sometimes assumed that stream turbulence induced by pipe elbows and globe or check valves will provide homogeneous mixing. Such mixing, although significant at high velocities, is far from satisfactory.ISO 3171 states that a ratio of the water concentration at the top of a pipe (C1) to water concentration at the bottom of the pipe (C2), or C1/C2, greater than 0.9 is indicative of good dispersion of immiscible liquids: 0.9 < C1/C2 < 1.0.
To ensure representative samples, we believe that the mixing system must maintain a C1/C2 ratio as near as possible to 1.0 under all flow conditions. To do this, the sampling system must provide efficient mixing based on optimized real-time feedback control using its analyzer sensors.
With that in mind, the R&D Group at Oil & Gas Measurement (OGM) Limited, under the direction of co-author Wes Maru, CEng, built multiphase flow loops at its facility in Ely, Cambridgeshire, UK, to test and optimize mixing and other technologies.
The flow testing and calibration laboratory (Figure 1) integrates a small multiphase flow loop (SMPFL) and large multiphase flow loop (LMPFL) for oil-water testing, a liquid meter calibration loop (LMCL), and a high-performance computing (HPC) capability.
Figure 3: Oil & Gas Measurement (OGM) Ltd.'s large multiphase flow loop has a 10-in. nominal pipe diameter, 110-diameter straight pipe section and 6-in. return flow, where entrainment atomization (EA)was characterized and validated using an advanced multi-probe profiling system per ISO 3171 and API 8.2.
The SMPFL (Figure 2), with a 2.5-in. nominal pipe diameter, was used with magnetic resonance imaging (MRI) to characterize the prototype.The LMPFL (Figure 3) has a 10-in. nominal pipe diameter, 110-diameter straight pipe section and 6-in. return flow. It was used to characterize and validate the SmartMix® entrainment atomization (EA) mixing device using an advanced multiprobe profiling (MPP) system according to ISO 3171 and API 8.2.
At the start of this technology development program, OGM set the following goals:
- Produce technologies and products that not only meet the current industry standards, but that essentially exceed them all.
- Accelerate design and testing activities through the use of synergistic fluid mechanics (physical experiment and computer simulation).
- Develop and employ turbulent multiphase flow models to understand the intricate issues involved in mixing of immiscible fluids in general, and oil-water flows in particular, in an effort to bring about a paradigm shift from current technologies.
- Improve the mixing efficiency (C1/C2 ratio) as defined in ISO 3171, beyond what is currently achievable.
- Obtain significant cost savings in lifecycle and energy usage compared to all currently available technologies.
.
In 2014, a research award to Dr. Maru by the UK’s Technology Strategy Board allowed collaboration with the University of Cambridge, which:
- Provided a process-size, research-quality MRI to characterize the prototype SmartMix®,
- Developed interest and resources to extend the research program into process industry technologies,
- Provided guidance on how to extract a new MRI sequence used to characterize the SmartMix® device and validate OGM’s in-house-developed advanced multiphase computational fluid dynamics (MCFD) modeling tools, and
- Provided critical review on the validation of the MCFD according to the International Association for Engineering Modelling, Analysis and Simulation Community (NAFEMS) test protocols for scale-up of the 2.5-in. SMPFL data to the a 10-in. LMPFL.
EA mixing technology in action
Figure 4: In addition to the Cambridge University MRI facility, characterization was done using electrical capacitance tomography (ECT) and a high-speed video camera that allowed imaging via an optically transparent Perspex (PPX) pipe.
Instead of physical agitation, the EA mixing system uses a controllable, turbulent vortex to achieve more representative sampling of immiscible liquids. The EA mixing relies on a weak jet/strong jet interaction supplied in a controlled way using proprietary (patents pending) mixing nozzles. This results in a more uniform droplet size and a more homogeneous flow profile than conventional sampling systems.These claims have been experimentally proven using Cambridge University’s MRI facility as well as highly sensitive electrical capacitance tomography (ECT) and a high-speed video camera that allowed imaging via an optically-transparent Perspex (PPX) pipe (Figure 4). The experimental validation together with the MCFD simulations show that the EA mixing system can control the droplet sizes and their distribution across the pipe diameter, creating fully homogeneous flow for improved representative sampling. Unlike other SMAS, SmartMix® also eliminates occurrence of undesirable oil-water emulsion.
In operation, a continuous stream sample is extracted from the process piping by an isokinetic sample extraction probe, circulated via a pump, and reintroduced to the process stream through twin nozzles that create weak jet/strong jet interaction within the process fluid.
This operation is constantly adjusted by a stochastic model-based feedback control system, which automatically responds to changes in the process flow rate and composition to achieve uniform droplet size and homogeneous oil-water mixture without producing any emulsion. The model-based feedback control uniformly adjusts to the measured fluid temperature, pressure, viscosity, water cut, density and salinity from its sensor systems.
The system achieves greater than 97% mixing efficiency, resulting in potential savings of millions of dollars per year (see earlier figures). This is accomplished in horizontal process stream piping, even at very low flow velocities. This eliminates the need for vertical piping, and avoids pressure drops due to elbows or bends. Installation can be done with minimal cost for process piping rework.
The high accuracy and continuous nature of the system may allow reduced manual sampling, minimizing or eliminating the common, laborious, expensive and less accurate five-stage sampling protocol. It is also energy-efficient, reducing pump power requirements by up to 50% compared to existing technologies.
Figure 5: A major oil operator in the North Sea has ordered three SmartMix systems for challenging applications, including complete replacement of an existing alternative system that failed to function as desired.
Existing applicationsAfter extensive testing and further industry- and peer-reviewed demonstration in the LMPFL at Ely, a major oil operator in the North Sea oil fields has ordered three SmartMix® systems for one of its challenging applications (Figure 5), including a complete replacement of an existing alternative system that failed to function as desired.
In summary, a new proprietary (patent pending) SMAS has been demonstrated to improve the accuracy required for ISO 3171 measurements by more than 7%, where 1% improvement equates to a saving of US $1 million for a typical 250 MBSD (1,500 m3/hr) process flow. It promises to:
- Bring rapid return on investment (ROI) in process crude stream quality measurement,
- Give accurate and efficient performance over very large process flow turndowns,
- Cause no system pressure drop, and
- Provide accurate, single-pass sampling through its compact fast-loop design, eliminating current sample recycle practices.
The system may also help optimize crude de-salter operation in refineries by improving droplet size and its distribution across the electrostatic field (energy saving), and by improving the operation of water wash injection and heat transfer via efficient mixing. The flow through the fast loop and its advanced control may also be able to replace current emulsifier valves.
SmartMix® may also provide data for prediction of corrosion levels due to free water in refinery piping and vessels. This allows reduction of expensive additives worth up to hundreds of thousands of dollars per year.
About the authors:
Wes Maru, Ph.D., R&D Manager, OGM corporate operations world-wide and principal technical contact for SmartMix® technologies, resides in Cambridge, UK, and can be reached at [email protected]. Gary Rathwell, principal, Enterprise Consultants International, is near Houston and can be reached at [email protected]. Robert E. Sherman, ISA Life Fellow and principal technologist, Enterprise Consultants International, is near Chicago and can be reached at [email protected].
References
- Lakshmanan, S., Holland, D.J., Maru, W., Gurevich, M., and Sederman, A.J., “Multiphase flow quantification using computational fluid dynamics and Magnetic Resonance imaging,” 33rd International North Sea Flow Measurement Workshop, Tønsberg, Norway, 2015.
- Lakshmanan, S., Maru, W., Holland, D. J., Mantle, M. D., and Sederman, A. J., “Measurement of a multiphase flow process using magnetic resonance imaging,” J. Flow Measurement and Instrumentation, 53 pp. 161-171 (2016).
- Huang, J., Lakshmanan, S., Maru, W., Thomas, A., “(SmartMix®) Validation of OpenFOAM Models with Magnetic Resonance Imaging and Nuclear Gamma Densitometer Measurements”, 12th International OpenFOAM Workshop, University of Exeter, 24th – 27th July, 2017.
- Maru, W., Sherman, Robert E., “Optimized Hydrocarbon Sampling Methodology and Equipment in the presence of Basic Sediment and Water,” 63rd Annual ISA-Analysis Division Symposium, April 22-26, 2018, Galveston, TX, USA.
- Maru, W-A., Holland, D., Huang, H., Lakshmanan, L., Sederman, A., Thomas, A., “Multiphase Flow and Mixing Quantification using CFD and MRI,” Invited Topical Review, J. Flow Measurement and Instrumentation, (2018), in press.
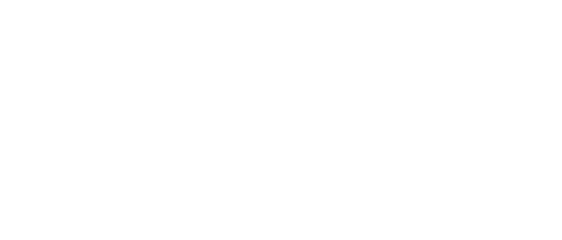
Leaders relevant to this article: