This Control Talk column appeared in the March 2019 print edition of Control. To read more Control Talk columns click here or read the Control Talk blog here.
My most challenging applications in my career were pH, demanding exceptional performance from valves, equipment, piping, measurements and controllers. Particularly difficult were applications involving high concentrations of strong acids, strong bases, salts and/or non-aqueous solvents. My sensitivity to valve rangeability and resolution started with these systems. Valves could be the deciding factor on the number of stages required by being the source of large oscillations due to amplification of valve limit cycles from resolution limits and minimum controllable flow due to a valve’s real rangeability. Poor designs of reagent injection and mixing are a big factor as well. The total system cost is largely determined by the size and number of vessels required, and can be greatly decreased by better I&E and mechanical design. If these risks are addressed, then the traditional solution is one well-mixed vessel for every 2 pH units from the most extreme feed pH to the pH setpoint. For example, if the incoming feed is 1 pH and the setpoint is 7 pH, three well-mixed vessels are required. Advanced control, with attention to details and the best valves, can potentially eliminate one vessel.
I was fortunate to have key books, papers and articles that provided the essence and reality of the solution by means of key, concise, insightful equations capturing the first-principle relationships. For pH, it was the charge balance equations I first saw in Shinskey’s 1973 book, pH and pION Control in Process and Waste Streams that led to my Masters’ Degree thesis, “Analysis of a pH Process and a Self-Adaptive Control System by the Use of Process Simulation,” followed by numerous successful applications and the ISA book, Advanced pH Measurement and Control. The charge balance equations were extended to include conjugate salts in the Chemical Processing article, “Improve pH Control.” The relatively simple equations and quick solution by interval halving amazingly address all of the issues I’ve encountered, avoiding thousands of pages of confusing, individual-application-specific equations seen in the literature. The effect of temperature on water, acid and base dissociation constants, which change the actual process pH and are not addressed by standard pH temperature compensation, is readily computed. The effect of high ionic strength on hydrogen activity, and thus pH, can also be included by an activity coefficient. The often-unrecognized, profound effect of carbon dioxide absorption simply from exposure to air is addressed by adding a carbonic acid concentration. The equations are truly elegant and offer incredible insight.
To emphasize the role such discoveries have played in my career, a few other examples have recently been noted in Control articles. To reveal the actual, quite bizarre, dynamic response of a compressor in surge, momentum balance equations were used to show the path of the operating point on a compressor map, as discussed in article “Compressor surge control.” The key to modeling complex, biological extracellular and intracellular processes is the multiplicative effect of factors for specific cell growth rate and product formation rate, noted in the article, “IIoT crossroads.” The limitation and inhibition effect of almost any component concentration can be expressed by Michaelis-Menten equations. The extreme variations in the effect of temperature and pH based on cell type can be readily computed by convenient cardinal equations. The parameters are rather intuitive and easily set.
For valve modeling, (a critical part of any digital twin used for process control improvement and described in the Control article, “Virtual plant virtuosity”), a combination of about five standard function blocks and a dozen lines of simple code in a CALC block can simulate a second-order, velocity-limited, exponential valve response with backlash, stiction and variable positioner sensitivity. The knowledge gained from using this valve response model goes well beyond pH, as seen in the Control article, “How to specify valves and positioners that don’t compromise control.”
PID Greg: The titration curve is the essential starting point for pH system design, including the 5Rs for measurements and valves, and minimization of dead time. Curves should be generated in the lab for the spectrum of operating conditions, including changes in process temperature and concentrations of acids, bases, salts and solvents. The lab must use the same reagent(s) being manipulated in the field for pH control. You must insist on at least 10 points in the control region. Often, labs find titration difficult using the high concentrations of strong acids and bases used in the field, and show only two or three points in the steep part of a titration curve. If it’s difficult for the chemist with a simple beaker, you can imagine what it is like in the field. For a continuous system, it’s like the beaker had a hole in the bottom, and someone was adding a variable amount and concentration of process sample. After conversion to the right concentration used, the X axis has be translated from reagent added to a volumetric ratio by dividing each reagent addition by the sample volume. Setpoints are picked on the titration curve for each stage of neutralization. The reagent flow needed to get to each setpoint for the extremes in feed concentration and flow is readily estimated, revealing the required size and rangeability of the reagent valve. The allowable control error at each setpoint, divided by the titration curve slope, is the summation of the permissible valve dead band and resolution expressed in flow units. To minimize excursions on the titration curve reducing the consequential nonlinearity seen, the total loop dead time must be minimized. The 86% valve response time must be less than 10% of process dead time from reagent injection and mixing. Reliable performance is a must due extreme nonlinearity and sensitivity.
I&E Greg: The best reagent valves we have available with a wide range of corrosion-resistant materials are linear globe valves with diaphragm actuators and digital valve positioners. The backlash dead band of 0.2% and a stiction resolution of 0.1% can more than double near the seat. The high viscosity and extremely low flows of concentrated reagents such as 98% sulfuric acid can cause plugging and laminar flow. The one bright spot is that the installed flow characteristic is linear for linear trim, since the ratio of reagent valve drop to total reagent system drop is high. Consequently, we can simply multiply the summation of dead band and resolution by valve capacity. We therefore may need a big and small valve in parallel to meet the rangeability requirement. The 86% response time for the small valve can be less than 2 sec. if a high-sensitivity positioner without integral action is used and tuned with a high gain. Since the control valve with the best 5Rs, particularly the least friction near the seat and best linearity, does not give tight shutoff, we will add an isolation valve to meet a leakage spec downstream of the control valve.
PID Greg: Instead of split-ranged control with its discontinuities at the split-range point and valve nonlinearity, we can use valve position control (VPC). The stage pH would be controlled by direct manipulation of the small, more precise, valve for fine adjustments. VPC with directional move suppression will only make coarse adjustments to keep the fine valve in a fine position. If plugging is a serious problem near the closed position, we can install a reagent dilution system using Coriolis mass flowmeters to give precise water-to-reagent ratio flow control.
The reagent injection delay must be minimized. The conventional dip tube design, with a minimum size of 1 in. to withstand agitation and an exit point near the agitator, and extremely low reagent flows (e.g., gph) can cause a reagent injection dead time of minutes to hours whenever the reagent valve closes for a sustained period, resulting in backfilling of the dip tube with process fluid. The maximum reagent injection dead time is the dip tube volume divided by minimum reagent flow. To avoid this problem, reagent should be injected into a feed or recirculation line just before entry into the vessel. An isolation valve should be close-coupled with the throttling valve to the pipe nozzle to minimize volume between control valve and injection point. We can coordinate automatic opening and closing of the isolation valve based on pH controller output.
For best pH control, the vessel must have an axial agitator and a height-to-diameter ratio between 1 and 2. Agitation should cause noticeable turbulence in the surface. The mixing dead time must be less than 6 sec. and can be estimated as ½ the vessel volume divided by the effective agitator pumping rate plus feed rate. The nonuniformity requirement can be considered normal (e.g., 1%) for a pH of 5 or 9 with buffering due to weak acids or weak bases and conjugate salts, or extraordinary (e.g., 0.001%) for solutions dominated by strong acids and strong bases at 7 pH. Nonuniformity shows up as fast random noise.
Now that we got the piping, mixing and valves, let’s move on to the measurement. We need electrodes to meet our 5Rs. Also, important is a minimal offset (e.g., less than 0.02 and 0.1 pH for biological and chemical reactors, respectively) and no susceptibility to noise.
I&E Greg: Wow! This is quite a challenge with extraordinary implications. To achieve rangeability and resolution beyond the neutral region we go with a spherical bulb electrode. Flat glass and ion-selective field effect transistors (ISFET) performance deteriorates at high and low pH. The glass must be selected to deal with sodium ion error above 10 pH from caustic and to minimize deterioration of hydrated layer from high acid concentrations below 1 pH. A high-temperature glass can double electrode life by slowing down the aging process that cuts life in half for every 25 °C increase in temperature.
The electrode 86% response time is less than 4 sec. if the velocity of the process fluid is greater than 1 fps and the glass surface is clean and in good condition. Aging and fouling of the glass surface can increase the 86% response time by several orders of magnitude. To prevent fouling, the process fluid velocity will be kept about 5 fps. A shroud can protect the bulb from direct impingement to reduce abrasion but lower velocities may still be necessary. Since velocities in even a well agitated vessel rarely exceed ½ fps and removal while the vessel is on operation is problematic, the best location is normally in a recirculation line with the velocity set by a throttling valve. If there is a heat exchanger in the line, the electrode will be installed upstream of the exchanger to minimize transportation delay, and 25 pipe diameters downstream of the pump to minimize noise from pulsations and concentration gradients.
Electrodes should be kept hydrated (with 7 pH buffer when not in service) to prevent deterioration of the glass surface and loss of pH response. The electrodes should not be installed until after the lines are clean and the process fluid is imminently ready to flow past the electrodes. The electrodes should not be installed in the pump suction because of possible vapor and bubble formation, and damage from nuts, bolts, welding rods and other debris not cleared out by flushing and water batching. The pump screen provides protection, and discharge pressure is normally high enough to ensure liquid flow. The electrodes should not sit in stagnant flow or empty lines. During shutdowns and in between batches, the electrodes should be removed if a continuous circulating flow cannot be assured.
For high-purity water applications, the velocity must be extremely low with a flowing junction reference electrode upstream of the glass electrode to reduce noise and fluid resistance. This is best done by a very small flow through the assembly, where geometry and velocity are enforced.
Where electrode life is severely reduced due to fouling, non-aqueous solvents or extremely high concentrations of acids and bases, an automatically retractable electrode will be used. The time of insertion is minimized and when retracted, the electrodes can be cleaned by flushing with a mild cleaning agent, conditioned by soaking in 7 pH buffer, and automatically calibrated by use of two buffer solutions. For high-ionic-strength applications, the equilibration time of the reference electrode can be reduced by the use of high-ionic-strength buffers.
Since actual solution pH changes with process temperature, results from laboratory tests and modeling will be used to determine the solution temperature compensation put into the smart transmitter.
Triple-junction and, especially, solid-junction reference electrodes, can greatly reduce poisoning, but the equilibration time is so long that tight calibration with two buffers is difficult, and drift can occur for days in high-ionic-strength process streams, making them essentially unusable for batch operations.
Calibration will most often be done with buffer solutions. If the offset is adjusted based on a process sample, precautions must be taken to prevent the sample temperature or composition from changing due to cooling, evaporation of volatile components, reactions, dissolution of solids (e.g., lime), or absorption of carbon dioxide from the air (or ions from a glass beaker for pure water solutions). This normally requires that the pH electrode be inserted in the sample immediately after the sample is taken.
To prevent the occurrence of the many problems with lab pH measurements, I will be adhering to the guidance offered in the Control Talk column, “The wild side of pH measurement”.
A flowing junction reference electrode has the fastest equilibration time and the least junction potential, minimizing the offset in pH measurement. The electrolyte reservoir must be pressurized and restricted to ensure a small, consistent, positive flow of electrolyte into the process. Process sample and buffer solutions must be in relatively large beakers, and a fast measurement made to minimize contamination by electrolyte ions flowing through the junction into the beaker. A reference electrode with a replaceable liquid junction, and an electrolyte and internal electrode chosen to minimize poisoning effects, can be a good compromise when flowing junctions are not wanted by maintenance.
Regardless of the type of electrode and the degree of difficulty of the application, three electrodes and middle-signal selection will be used to inherently ignore a single failure of any type, decrease offset, reduce vulnerability to a slow electrode, ignore noise from EMF or non-ideal mixing, and to provide intelligent diagnostics that actually reduce maintenance. The lifecycle cost is greatly reduced and savings can be enormous if you include the effect of process efficiency and capacity.
P&ID Greg: Thank you. A good measurement improves the tightness of control not only by faster and more precise measurements with less offset, but also by more accurate linearization. The titration curve obtained from the laboratory and extended by modeling can be used in signal characterizers to translate the controlled variable from pH to the X axis of the titration curve, simply expressed as 0-100% reagent demand. A cascade of characterizers is used to provide greater resolution in the control region. For much more on the applications and implementation of signal characterizers, see the Control Talk blog, “Unexpected benefits of signal characterizers.”
The theoretical calculation and use of hydrogen ion concentration from just strong acids and strong bases (ignoring the incredible moderating effect of carbon dioxide absorption to create carbonic acid or other weak acids and weak bases and conjugate salts) is unrealistic. Such systems rarely exist and any controlled variable based on such an erroneous calculation is wrong. The slope of the titration curve, and thus the process gain, is orders of magnitude larger than actual. I made this mistake early in my career. I saw it repeated by an associate decades ago, and touted it in a recent article in a magazine popular with process engineers. The moderating effect must be included by an expanded charge balance.
If you want a comprehensive, concise view of how to achieve the best measurement and control, look for the McGraw-Hill Handbook, “Process/Industrial Instruments and Controls Sixth Edition,” due out in early 2019. The handbook covers the design, installation, calibration, commissioning and maintenance of every part of an automation system, concluding with a list of best practices for each of the hundred sections resulting in over a thousand best practices. See the Control feature article, “Best practices for PID,” for another glimpse of what the handbook offers.
10. We have reagent valves with tremendous flow capacity and nearly zero leakage
9. I prefer to have the electrodes in an analyzer house where HVAC invites longer maintenance
8. I like to let the process sample cool off before I measure it
7. What are buffer solutions?
6. I scrub the heck out of the electrodes to make sure they are clean
5. We like to make sure the electrodes dry out in between batches
4. We like to install the electrodes before water batching
3. We went with submersion assemblies and just left them alone
2. I have a favorite electrode—I don’t need middle signal selection
1. My electrode is great—the measurement hasn’t changed value in over a year
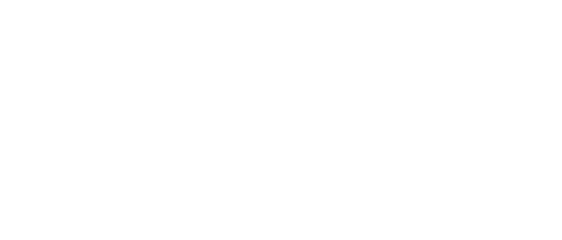
Leaders relevant to this article: