Jim Smith set the bar for innovation sky high from the very start when in 1977 he led the team that brought the first meter for measuring mass flow based on the Coriolis effect to the industrial market. Since that time, Micro Motion, now as part of Emerson, has continued to break new ground, expanding the application envelope of Coriolis technology and making its industry-leading meters ever smarter and more capable.
To learn more about how the company has successfully responded to changing industry demands—and what trends are likely to shape the company’s portfolio in the future—Control caught up with Amy E. Johnson, vice president of Coriolis, Density and Viscosity and Ultrasonic Flow Meters for Emerson’s Automation Solutions business.
Q: It seems that Micro Motion’s early years were all about increasing performance—improving the accuracy and stability of mass flow measurement, even as the meters were made able to measure a broader range of diverse, even multiphase flows. Can you speak a bit about the innovations of the products over the years, and how some of the industry requirements have changed?
Vice President, Coriolis and Ultrasonic Flow Meters, Emerson
A: After the introduction of the Coriolis technology with direct density measurement into industrial applications, we started to make some extensions to the products to the meet demands of new markets. A lot of our development efforts focused on the oil and gas market, which tends to have some of the most demanding process requirements of any industry. Operating in this space has driven our innovations to handle higher temperatures, pressure and multiphase measurement conditions, frankly, pushing Coriolis operating conditions beyond simple process control. We've really come a long way since our first Coriolis meter, which was mounted on a concrete block and had limited outputs. Now, we have a device that can measure a little as a few drops an hour to 14-inch meters that measure 120,000 lb/min and everything in-between. This multi-variable device is pushing its application space and how customers are using the information from the meter to drive step changes in their businesses.
Q: There also seems to have been an era of Micro Motion product innovation that focused more on the application context of the meters in use. I’m talking about two-wire transmitter versions that increased application flexibility; then there’s onboard functionality like Smart Meter Verification that boosted reliability and made them easier to manage from an asset perspective. What were the driving forces behind these advances, and what benefits were realized by users?
A: One of the challenges that we hear from our customers is they want a Coriolis meter, but it can be expensive to upgrade legacy products in their plants. Legacy equipment can be two-wire/loop-powered devices that tend to be a limiting factor for which technology they can use. Traditional two-wire devices couldn't provide enough power to really drive/operate a Coriolis meter to its full potential, meaning two-wire Coriolis meters exist but with compromised performance. We're always driven to meet customer challenges, so we pushed our development teams to improve our abilities, and as a result, we have our 4200 two-wire Coriolis transmitter. By incorporating advanced signal processing, we were able to release our 4200 transmitter on our meters without any compromise of performance. This transmitter will allow customers to get our meters in that two-wire form factor, so they can upgrade value measurement points and get all of the benefits of Coriolis technology. This transmitter brings a lot of new features to the two-wire market: Coriolis line sizes up to 4 inches, compatibility with our straight-tube sensor, integrated data historian and real-time clock.
In addition, we added our Smart Meter Verification diagnostics to this two-wire device and all our Coriolis meters. Evolving from Meter Verification (launched in 2006), Smart Meter Verification for our Coriolis meters was ahead of its time when we launched it back in 2010. For the first time, it allowed a user to verify—even remotely—that a meter was working correctly without having to remove it from service or interrupt the associated process.
Customers often ask, “How often do I need to calibrate my Coriolis meters?” But since there are no moving parts, there are very few things within the meter that requires constant attention, Smart Meter Verification is there to keep tabs on the meter. If something does change, we have a team of application specialists, who can look at a data set and tell you exactly what’s going on. Bottom line, the assurance afforded by Smart Meter Verification is helping users to reduce the number of calibrations they perform.
Q: Across industry, an increased focus on data and connectivity has been front and center for the past half dozen years. What has Micro Motion been doing to leverage the new power of data analytics on behalf of its users?
A: I mentioned earlier the onboard data historian, which was first included in our model 5700 field transmitter. But we didn’t stop with data storage. We also developed a range of tools to analyze that data and make it easy for our customers to understand what’s going on in their processes and how their processes are changing over time. Starting with the foundational level of the data, we've been incorporating more digital communication protocols, including Ethernet. We just introduced the 5700 Wi-Fi, a Coriolis transmitter that uses wireless as a secondary channel for transmitting diagnostic information, so if it happens to be January and snowing outside, a technician doesn’t have to trudge through the snow to access the installed meter.
Providing this sort of access to information is at the forefront of our thinking: how do we continue to evolve the usability of our meters, and help our customers with what they want to do next with that information?
Q: Are there other new demands and emerging applications that will shape the next generation of Coriolis technologies that we see from Micro Motion?
A: We're seeing customers apply Coriolis technology to more measurement points across their plants as well. Not only can our meters provide the most accurate flow measurements in the world, but we also provide extremely reliable, repeatable process measurement solutions. Having a reliable measurement is only part of the solution. Now that customers are upgrading their technology and communication protocols and the speed of data transition is getting better, customers are tapping into our meters because they're data machines. As a result, they're using the data to drive second-order improvements to their facilities. They're operating more efficiently, with less down time, and more safely.
Another new arena where we’re starting to see more and more interest in Europe is in the use of Coriolis technology to meter hydrogen as an alternate vehicle fuel. We recently introduced a new high-pressure Coriolis sensor designed specifically for dispensing hydrogen into vehicles, which has now been approved by European agencies for such custody-transfer applications.
While this may not be an application we would have envisioned back in 1977, we're always looking to our customers to challenge us, to bring new ideas, to ask us “Hey, what if we did this? What if we did that?” We’re always looking for unique challenges that push the limits of what we know a Coriolis meter to be
Continue Reading
Latest from Flow
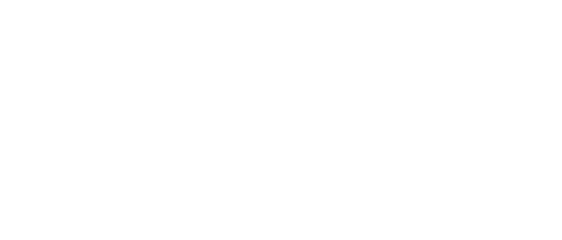
Leaders relevant to this article: