Ethernet-APL: Are you prepared for the new way of doing things?
For more than 10 years now, the process automation supplier community has been working on new networking technology that would finally allow Ethernet to be extended to field instrumentsāwith power and communications over a single pair of wires and in hazardous areas to boot. And this spring, at the Achema Pulse virtual tradeshow, a consortium of suppliers and all the key standards development organizations (SDOs) announced that specifications and chipsets for Ethernet-Advanced Physical Layer (Ethernet-APL) were ready for prime time. But what comes next?
To explore what Ethernet-APL means for the future of field communications in the process industries, Control caught up with Paul Sereiko, director of marketing and product strategy for the FieldComm Group, one of the SDOs that, together with a consortium of leading automation suppliers, supported Ethernet-APLās development and launch. To frame the discussion, we did an email survey of Control readers to gauge industryās understanding and preparedness for this new way of doing things. The results of that survey of 230 individual stakeholders across the global process automation industry are highlighted below.
Q: Weāve both been quite involved in developments on the Ethernet-APL front, but in a just completed survey of Control readers, a majority of respondents said they were just āsomewhat familiarā with this new technology. To start things off, can you review what unique advantages Ethernet-APL brings to field communications?
Director of Marketing and Product Strategy,Ā FieldComm Group
A: I think it's important to realize that for quite some time now, instrument and infrastructure suppliers have really wanted to extend Ethernet networking capabilities to the field level, but doing so requires a physical layer that meets the demanding needs of process automation. Deployment in hazardous areas is certainly one; support for long cable runs is another. And, given the expense of copper together with industryās current practices, a two-wire solution that could carry both power and communications was needed. The technologies required to make this a practical reality simply werenāt available until now.
The operational benefits of Ethernet-APL are wide ranging and include the ability to add many new and different device types, and efficiently distribute information to more peopleāeven remotelyāenabling better and more dynamic collaboration among team members.
A key enabler of these benefits is Ethernet-APL's higher communications speed. Clocking in at 10 Mbps, it provides digital transmission rates that are orders of magnitude faster than any of its precursor physical layers. For example, layering a digital signal onto a 4-20 mA loop is bound by 1,200 or 9,600 baud modems; the original fieldbus protocols are fasterābut nowhere near 10 Mbps.
1. Dramatically faster data rates than previous digital options |
2. Suitable for use in hazardous (classified) areas |
3. Communication protocol independence |
4. Accommodates multiple protocols at same time over same wire |
5. Provides power and communications over two wires |
Table I: When asked how important the above characteristics of Ethernet-APL are from an end-user perspective, the majority of respondents answered "very" or "fairly" important, with the total ranging from 73% (#1) to 67% (#5).
Q: In that survey that we did of Control readers, all those characteristics of Ethernet-APL were ranked as important, with faster data rates and hazardous area suitability ranked most highly (Table I). Another important characteristic of Ethernet-APL is that it's protocol independent and can accommodate multiple protocols over the same wire at the same time. Can you explain a bit more what that means from a practical perspective?
A: That aspect of Ethernet-APL is going to require a mindset change on the part of end users as well as engineering firms and process automation system designers. In the past, the physical layer of process automation communications has been bound together with the application layer, but with Ethernet-APL the physical layer has been effectively decoupled from the applications that run on it. Think of your home IP (Internet protocol) network; in addition to your PC, it also connects to printers, cameras, doorbells and the like. And all these devices are using different application protocols, together with a common media access and transport protocol, IP. Ultimately, transferring this model to the process automation world will result in much simpler and more flexible network designs and eventually new instrumentation and instrument architectures as well.
Take the FieldComm Groupās 2018 Plant of the Year honoree, the Shell Prelude. A floating natural gas processing facility off the west coast of Australia, this plant has 8,500 Foundation fieldbus devices for control, 4,500 HART devices for its safety instrumented systems and fire and gas systems, plus more than 1,000 WirelessHART transmitters. So, to engineer this system, the integrator needed to deploy wiring and infrastructure for HART transmitters, a parallel infrastructure for Foundation fieldbus, and yet a third Ethernet network for the top end of the WirelessHART gateways. Thatās at least three separate networking infrastructures in the facilityāall of which could be replaced with a single network infrastructure based on Ethernet-APL. The engineering firm could then pick the most appropriate automation protocol for the various applications implemented in facility, say, Profinet for motor control centers, EtherNet/IP for complex analytical instruments, or HART-IP for basic control. Or how about RTSP for a thermal imaging camera? It's a huge game changer.
1. Fast, easy device installation and commissioning |
2. Allows Ethernet cybersecurity model at device leve |
3. Accommodates new device/data types |
4. Comfort/familiarity with Ethernet |
5. I/O flexibility to integrate traditional and APL devices |
6. Fast, ready access to data besides the process variable |
7. Enabler for drivers ad other software to be installed on device |
Table II: When asked how important the above value propositions of Ethernet-APL are, the majority of respondents answered "very" or "fairly" important, with the total ranging from 80% (#1) to 70% (#7).
I also think it's important to realize that all of this is going to be a journey. Itās exciting to think whatās possible, but it will take time for Ethernet-APL to gain market share in what is a necessarily conservative industry. Itās also incumbent on the SDOs like FieldComm Group and the supplier community to provide a reasonable roadmap for the journey. While education is important, I can't overestimate how important it is to not oversell whatās possible today.
Q: We also asked our readers to score the relative merits of seven different value propositions that APL satisfies (Table II). The first among relative equals was āfast and easy device installation and commissioning.ā Are you surprised that this project-oriented activity was deemed as most important relative to ongoing operational activities?
A: I like the turn of phrase āfirst among equalsā because all these value propositions were ranked as quite important by the readers. Commissioning has historically been one of the most time-intensive and thus costly aspects of project construction. The combination of dramatically faster network speeds combined with the familiarity of HART commissioning tools will bring a major advantage to project schedules and costs. Obviously, this translates to earlier start-up and faster ROI on project investments.
Ā | Significant | Not significant |
1. Integration/interoperability with current systems | 72.1% | 27.9% |
2. Availability of APL-ready devices | 71.9% | 28.1% |
3. Introduces cybersecurity risk at device level | 58.8% | 41.2% |
4. Management o change from current methods | 56.6% | 43.4% |
5. New technology learning curve | 50.0% | 50.0% |
6. Protocol competition/confusion | 48.7% | 51.3% |
7. Personnel capacity to learn new approach | 47.2% | 52.8% |
Table III: Survey respondents indicated that the most significant potential barriers to Ethernet-APL adoption are integration/interoperability with current systems and availability of APL-ready devices.
One of the developments that I'm looking forward to watching evolve is how device vendors might choose to incorporate software such as device drivers and FDI device packages directly onto the instrument itself, which would obviate the need to manage such software tasks manually. I think instruments will soon be equipped with more onboard memory to automate these steps in the future.
Q: In our survey, we also asked our readers to confirm the relative importance of several Ethernet-APL value propositions (Table II). It was interesting to note that the ability to employ āEthernet cybersecurity models at the device levelā was seen as the second most important value proposition, yet the use of Ethernet at the device level was also cited as increasing cybersecurity risk and a potentially significant barrier to adoption for most respondents (Table III). How can we square the circle on this apparent contradiction?
A: I think itās a given that if an instrument is IP addressable, then you'd better have great cybersecurity. Thereās rightfully going to be some hesitation on the part of end users to drop IP-addressable devices into their plant, and perhaps that path starts, not with control devices, but with monitoring or optimization use cases as outlined by organizations like NAMUR in its Open Architecture (NOA) vision. But it's also incumbent on SDOs like FieldComm Group to make sure we have unambiguous specifications. Late last year, we released a new version of the HART specificationāof which HART-IP is a componentāand we now specify exactly what sort of security is required for certification as a HART-IP device.
Figure 1: Survey respondents were asked: Over the next 12-24 months, which of the following statements best reflects your organization's interest/exploration of APL technologies? While the largest fraction say they'll "wait and see," nearly as many plan to "learn/evaluate/trial."
Q: The value proposition āI/O flexibility to integrate traditional and APL devicesā certainly speaks to accommodating a mixed environment of analog 4-20mA transmitters that speak HART together with new Ethernet-APL devices that speak HART-IP. Can you explain a bit about how using this common protocol, HART, over what is in effect two different physical layersāthree, really, if you count WirelessHARTācan simplify operations in a mixed technology environment?
A: This question really strikes to the heart of the journey that the transition to Ethernet-APL represents. As with any new technology, adoption will take time. Having the flexibility to integrate legacy and new devices into a common architecture will give users flexibility to go at their own pace and avoid proprietary architectures which, as we've seen in the past, can slow adoption.
The collaboration among the user community and suppliers we facilitate through the FieldComm Group ensures that the platform is rock-solid for all applications. It's also important to have a strategy that allows for some commonality and continuity as industry migrates from 4-20 mA to fully digital systems. You already know you're going to be learning a new networking infrastructure with Ethernet-APL, but wouldnāt it be nice to retain some familiarity with the application software layer? And when it comes to users and suppliers of process instrumentation around the world today, that application software layer is HARTāfrom asset management systems to control systems to devices and work processes. HART familiarity removes a big barrier to entry because you donāt have to learn new automation protocols or reinvented work processes.
Figure 2: Most survey respondents "realistically expect suppliers to begin offering a comprehensive portfolio of APL-compatible products" about two to three years from now.
At the Achema Pulse virtual event in June, Emerson demonstrated a single control loop that included both a 4-20mA device and an Ethernet-APL device. From the perspective of the operator or the asset management system, there was no difference. You couldnātāand you neednātābe able to tell one from the other unless you drilled deeper
Q: HART has certainly come a long way since it was first introduced in the 1980s, and todayās HART-IP even includes an integrated security model, which should help to address concerns over increased cybersecurity risk. What other aspects of HART-IP over Ethernet-APL can help to streamline the process industryās journey into this brave new world?
An email survey ofĀ Control's e-newsletter subscriber database was conducted in early August 2021, resulting in a total of 230 completed surveys, about 55% from the United States and 45% internationally. Industry, function and operating plant vs central engineering role as indicated:Ā
A: HART has been arguably the most trusted communications protocol in the industry for four decades. It's clearly the most fully built out for diagnostics. It's familiar, robust and reliable. But it does appear that some users may have an outdated understanding of its capabilities. As we introduced extensions to the protocol like wireless and Ethernet, we've made big steps forward in terms of speed, ease-of-use, security and more.
Much of industryās primary focus right now isn't on the core process control systems, but on the monitoring and optimization systems enabled through digital transformationāthat second, alternate path for all that other data that's beyond the control. This all-encompassing monitoring and optimization realm is where a lot of the new applications and new analytics are being developed. But all of that is predicated on having a protocol at the instrument level that's rich in diagnostic, maintenance and configuration capabilities. HART has always been perceived as a diagnostics and configuration protocol with 4-20 mA still being the predominant method of control.
That means that the data underpinnings for NOA use cases are there in HART and have been there for decades. The challenge was getting that information out of those 4-20 mA, 1,200 baud devices. With Ethernet-APL, all that will change. Longer term, Ethernet-APL will dramatically simplify automation architectures, so we donāt need all those gateways translating data between levels.
The workforce is changing too, and the new generation wonāt come in prepared to work with 4-20 mA analog transmitters and the like. And if they have networking experience, itās likely with Ethernet. So, Ethernet-APL technology is coming out at exactly the right time for the market to transition as we continue this ongoing cycle of workforce retirements and rejuvenation.
Latest from Industry Perspectives (sponsored)
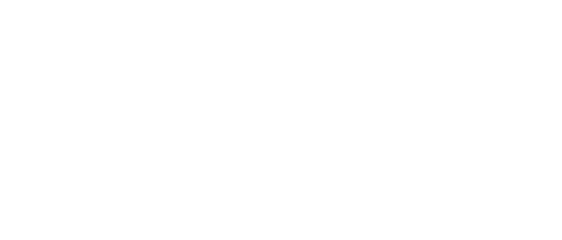
Leaders relevant to this article: