At their simplest, Coriolis meters operate by using a drive coil to make the tube through which mass flow is to be measured vibrate at a naturally resonant frequency. Filling the tube with a fluid causes the resonant frequency itself to shift in proportion to the density of the fluid. And, once flow begins, the Coriolis effect dictates a phase shift in the vibration that is proportional to the mass flow rate through the tube. The calculated mass flow measurement, then, is only as accurate as the reference to which these changes are compared is stable.
Make no mistake, the ability of the earliest Micro Motion meters to measure mass flow directly was a game changing innovation out of the box, but the company’s A, B and C Series single-tube meters required that the meter be anchored on a grounded block of concrete to provide this stable point of reference—it was neither the easiest nor most flexible installation arrangement.
Introduced in 1983, the D Series’ breakthrough innovation was a patented dual-tube design that split the flow between two tubes that vibrated with respect to one another, effectively canceling out many of the external factors that would otherwise have affected meter accuracy. The D meter—and its users—were liberated from those concrete anchors, resulting in Coriolis applications that were easier, more flexible and more accurate as well.
The success of the D Series meter demonstrated two interwoven throughlines of Emerson’s longstanding leadership in the arena of Coriolis measurement: the drive to increase mass flow accuracy while simultaneously broadening the application envelope of the technology. The steady drumbeat of sensor innovations that led to the D Series meter only intensified after Emerson’s acquisition the following year.
ELITE Series debuts
The balance of the 1980s saw Emerson’s Coriolis presence and customer base expand across Europe and Asia, even as product development efforts continued. Line sizes increased, as more precise sensor electronics allowed the accurate characterization of two-phase flows. These and other advances culminated in the 1992 debut of the Micro Motion ELITE Coriolis meter, which became the preferred high-performance solution for critical applications such as custody transfer and multi-phase flow measurement.
The ELITE Series combined superior mass flow, density and volume measurement in a wide variety of line sizes and materials. To this day, its mass flow accuracy of 0.05% sets the standard for Coriolis meter performance. The ELITE Series meters were also designed to accommodate widely varying application conditions from cryogenic conditions to high temperature and pressure extremes.
“With the ELITE Series, we made a product that is designed to handle the most challenging applications,” says Patrick Zimmer, director of product marketing, Coriolis technology, Emerson. “You can certainly compensate for a lot of problems with software, but our philosophy is to design our products to minimize the effects of process conditions so they can handle nearly all process variations and conditions. Measuring two-phase flow, for example, is more effective with a lower resonant frequency. We looked at how the tubes themselves were structured to create a lower frequency sensor which in turn eliminated many of the performance effects generated by multiple phases going through the meter.”
Process control workhorse
If the ELITE Series staked out the high-performance end of the Coriolis application space, the sweet spot for 1995’s F Series introduction was intended as a practical replacement for competitive flow measurement technologies being used in process control applications. The F Series delivers 0.1% mass flow accuracy and is available in line sizes from 1/4 to 4 inches in 316L stainless steel or nickel alloy C22.
“The F Series is a compact, drainable product family that is still highly accurate and extremely reliable, but smaller in footprint,” says Zimmer. “Its sister product is our H Series (for Hygienic) that was launched in 2002. That sensor is similarly compact, but features hygienic surface finishes for applications in the life sciences and food and beverage industries.”
The straight tube revisited
By 1999, Coriolis technology had advanced considerably, and the time was right to revisit a straight, single-tube meter. A range of customer applications, especially in the food and beverage industry, dictate a straight, single tube rather than splitting the flow in two. This might be required due to cleaning with a mechanical device or to preserve product integrity during production. (Imagine a mixed flow of yogurt with whole raspberries.) Without the compensating effect of a second tube twisting in the opposite direction, Emerson engineers had to tackle varying temperatures and other effects head on.
They found their solution in the titanium from which the T Series takes its name. Titanium is far less sensitive to temperature changes than steel alloys. It retains a consistent stiffness, and doesn’t expand or contract nearly as much as steel does in response to changing temperatures. “It’s the same material used to make aircraft turbine blades,” says Zimmer, noting the similarly precise tolerances that turbine blade must maintain in the face of extreme temperature swings. Placing the flow tube down the center of a rigid outer case provides the necessary frame of reference for accurate mass flow measurement even when the process is quite hot and ambient conditions cold. “It’s also a relatively compact meter,” adds Zimmer, “which is well suited to food and beverage applications where space can be at a premium.”
Viscosity, density portfolio additions
While much of Emerson’s expanding footprint in Coriolis technology was through organic growth, the 2005 acquisition of Solartron Mobrey expanded the company’s measurement portfolio with dedicated viscosity and density measurement technologies.
“Viscosity and density are often tightly correlated with final product quality—which is often at least as important as product quantity,” notes Zimmer. Insertion-style gauges can accurately measure density and viscosity in open or closed tanks as well as in flow applications, thus representing important complement to the Coriolis meter’s density measurement capabilities.
Key applications include the blending of multiple components to reach precise viscosity and/or density targets. “Consider a large ship that uses both light diesel and heavier, marine-grade fuels,” Zimmer says. “The latter needs to be heated to a specific viscosity for optimal engine operation.” Fermentation monitoring and control also benefits from insertion-style density instrumentation.
Pushing the extremes
At the end of the 2000s, Emerson again expanded the application range of its ELITE Series with both smaller and larger Coriolis meters. In 2009, the ELITE High Capacity meters became available for line sizes up to 14 inches in diameter. This significantly bolstered Emerson’s Coriolis offering in the custody transfer arena, especially for customers in the oil and gas industry. At the other extreme, the ELITE CMFS meter introduced in 2010 extended line sizes downward to as little as 1/12 of an inch.
“We now have a device that can measure as little as a few drops an hour to 14-inch meters that measure 120,000 pounds per minute, and everything in between,” says Amy Johnson, vice president, Coriolis and ultrasonic meters, Emerson. “This multi-variable device is pushing its application space and customers are using the information from the meter to drive step changes in their businesses.”
Latest from Flow
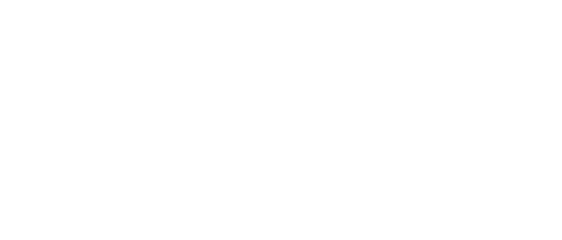
Leaders relevant to this article: