A*STAR model factory initiative allows manufacturers to test digital twin technology
Although some larger firms may have already invested in digital twin technology, others, like those in the manufacturing industry, have been more cautious, weighing the costs with the benefits and the risks that come along with such a large technical infrastructure change.
To give manufacturers a place to develop proof of concept and investment, Singapore-based Agency for Science, Technology and Research (A*STAR) and the Advanced Remanufacturing and Technology Centre (ARTC) developed a testbed for digital twins, the virtual counterparts of real-world manufacturing equipment, at the ARTC, according to an article on A*STAR’s website.
“There is so much potential,” said Stuart Wong, senior group manager at the ARTC, in the article. “But there was no showcase or test data that proved that this new technology can really be used to optimize smart factories.”
Anikath Murali Das, an ARTC program manager, added, “We are bridging the gap between pure research and product development.”
With ARTC’s model smart factory, manufacturers can navigate kinks in their digital twin developments and experiment with various features. And ARTC is continuing to expand those options. Currently, it is working to develop augmented reality features using Microsoft’s HoloLens, which layers digital graphics over visuals of the real world, the article explains. Additionally, it is developing a suite of web-based apps, giving on-the-go workers access to important data from their smart devices as well as virtual help when needed.
“If some maintenance or repair task is beyond the scope of a worker, [using our tools] a colleague somewhere else could see exactly what the worker standing at the machine sees and guide them on what to do,” Das explained in the article.
The researchers continue improve their model and are investigating the best method for adding sensors to machines from industrial partners, the article reports.
“We have a machine on loan from a company, which we have sensorized ourselves,” Das said in the article. “We have put in 43 sensors to look at vibration, temperature and acoustic emissions.”
Data storage and cybersecurity are other factors that the researchers have been and continue to explore. Wong notes in the article that the researchers have put an emphasis on designing the software to be secure, scalable, reliable and lag-free.
The current focus of the developments at ARTC is helping current factory staff, but Wong sees more in the future as artificial intelligence (AI) takes hold.
“The goal is to assist humans by aggregating and digesting data, then creating insights from it. The control room will provide information and predictions, but the human has to make the decision,” Wong said in the article. “… As the systems become more intelligent, we can move to full automation by AI. That can relieve humans to focus on things that AI can’t do: relationships, supply chain or customer issues, and managing workers.”
Das adds that networked machines will be able to collaborate to predict and respond to failures. “Machines will be able to talk to machines directly,” she said in the article. For example, “the machine in my factory could tell a machine in an offsite factory ‘shut down, I don’t want the part you’re making.’”
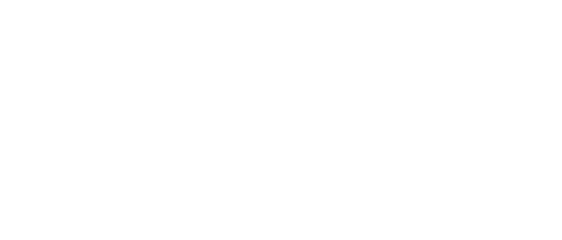
Leaders relevant to this article: