New nozzles improve attemperation at Duke Energy
Duke Energy, a Fortune 150 company headquartered in Charlotte, North Carolina, provides service to more than 8 million customers in six states. Like most energy companies, Duke is moving toward renewables, aiming for a 50% carbon reduction by 2030, when it plans to begin closing coal plants, en route to net-zero emissions by 2050.
Traditional production solutions are beginning to strain under new requirements and processes. For example, atomizer nozzles have been used to control attemperator operating ranges in steam applications for years. But, as the energy market moves toward renewables and as gas-turbine improvements lower combined-cycle plant loads, these attemperators need to adapt and operate under a wider range of conditions.
Duke Energy operates 18 heat-recovery steam generator (HRSG) units, but focused its recent efforts on two particular North Carolina sites in Buck and Dan River. “With the interstage attemperator, we have to maintain a steady temperature to the steam turbine,” explained Eugene Eagle, lead HRSG engineer, Carolina Natural Gas, Regional Services, Duke Energy, who spoke this week at Emerson Exchange. “We have to inject cool water into a hot steam pipe. That can be challenging, especially when you’re cycling the unit.”
Some of the problems include high exhaust gas temperatures at low-load isotherm. Between 40 and 160 MW, exhaust gas temperature was at 1,185 °F. “We needed to be controlling temperature at 1,050 °F,” explained Eagle.
The attemperator spray flow from the original Fisher TBX ring-style nozzle was injected in a vertical configuration at the side of the HRSG units, and thermocouples were added to the downstream elbow 21 ft from the spray point, and temperature differentials up to 400 °F were observed between the elbow intrados and extrados during low-load conditions. Additionally, three thermocouples that measure the steam temperatures downstream of the hot-reheat (HRH) attemperator were being wetted by unevaporated spray flow.
“At Buck, we have thermocouples farther from the elbow than the thermocouples at Dan River,” said Eagle. “We started collecting data in May 2018. The thermocouples were mounted on the outer diameter of the piping.”
Low-load and cyclic operation create more wear and tear on plant equipment. “It increases the risk for thermal-mechanical fatigue failures of HRSG steam piping and pressure parts due to quenching and temperature differentials, especially as the units age,” explained Eagle.
The nozzle used to inject the spray into the steam has significant impact, and few changes had been made over the years. Fixed orifice nozzles are used in constant-load applications, but they aren’t optimal for combined-cycle plants because they lack the ability to handle varied flow rates and pressure drops.
The probe-style nozzle is susceptible to thermal fatigue. Spring-loaded spray nozzles handle pressure drops and inject radially into the flow stream. “We were reaching the limits of these spring-loaded nozzles,” said Eagle.
This offered an opportunity to improve the absorption into the steam line. “The Fisher DSA is a probe-style design,” explained Justin Goodwin, director, steam conditioning, Fisher Engineered Products, Emerson. “This is the best technology we have for breaking the flow up into a fine mist, regardless of flow rate. Injecting water through high-velocity jets of steam results in a fog-like mist that is readily absorbed in the steam, regardless of the water pressure. However, it has limitations, such as vortex shedding and wake frequency.”
Turning the attemperator off and on can cause cracking, which can lead to broken probes, and high steam velocities can cause vibration due to vortex shedding, and this could even cause the probe to break off. Spray nozzles also can become stuck with debris.
“We designed a new steam-atomized nozzle to replace existing spray nozzles,” said Goodwin. The Fisher ATST steam-atomized attemperator uses a laser powder bed fusion (PBF) process to produce the water/steam passages within the nozzle. “It eliminated joints where we didn’t want them,” explained Goodwin. “Additive manufacturing eliminated 100% of weld joints. We printed lots of geometries of the nozzle and tested them in the ATST Lab.”
The new nozzle design is highly resistant to plugging; it eliminates main failure modes of spring-loaded attemperator nozzles; it eliminates thermal-shock failures associated with probe-style attemperators; it’s highly corrosion-resistant; and the quick nozzle replacement is designed to simplify maintenance.
“There are no small passages to plug,” explained Goodwin. “We’re using a cobalt chrome alloy, so it’s not corrosive. And there are no moving parts, no spring to weaken and no trim or weld joints.”
The first unit was installed at the Buck facility. “We reached a field-trial agreement with Emerson,” said Eagle. “This can only work with your reheated attemperator. We attached it to the high-pressure drums—around 600 °F— where the goal is to maintain a 400-lb differential between your supply and your output. It only required two nozzles. We previously used four spring-loaded nozzles.”
Everyone, including management and operators, were pleased. “We then did Unit 12 at Buck, and then two units at Dan River and then other additional sites,” said Eagle.
Get the best of Emerson Exchange Americas 2022
When the event comes to a close, the best, most important coverage will be compiled into a report. Register now to pre-order the report and be among the first to receive it in your inbox.
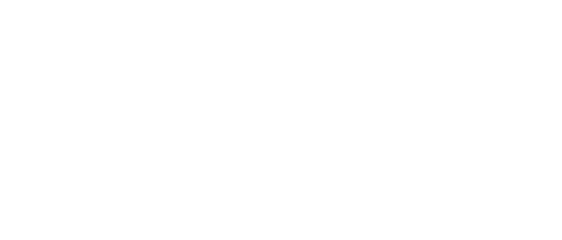
Leaders relevant to this article: