When it expanded into a brand-new 40,000 sq.ft. space near Boise, Idaho with a 50 bbl, four-tank craft brewery, Mother Earth Brewing Co. engaged Paul Mueller Co. for the process, brewhouse and piping engineering; Stone Technologies, Inc. for the automation; and Head Brewer Chris Baker to be sure the new facility could continue to provide the flexibility needed to maintain and expand the company’s eclectic collection of craft labels.
Along with Ryan Williams, project manager, Stone Technologies Inc., Baker presented the session, “A Greenfield Installation of the PlantPAx System Keeps the Craft in Craft Brewing while Automating Processes” at the 2016 Process Solution User Group (PSUG) conference this week in Atlanta.
Along with recipe flexibility, the automation system handles energy recovery, process-value-dependent routines, and an innovative approach to clean-in-place (CIP). The controlled equipment includes a mash mixer (to mix crushed grain and water under controlled pH and temperature); lauter tun (where grain and liquid wort are separated and solids are extracted using a rake mechanism); brew kettle (to boil, concentrate and sterilize the wort, and add hops); whirlpool filter (to further separate solids and deliver cool wort); fermenters (where temperature is closely controlled to prevent off flavors); centrifuge (with a 10-micron lenticular filter to clarify the brew); and “bright beer” storage before carbonation and packaging.
The system has to handle a wide variety of recipes. “We typically brew seven varieties of beer in a given week, and 60 or 70 varieties over the course of a year,” Baker said.
Reliable, repeatable, and flexible
“Automation makes craft beer reliable and repeatable—you’re not dragging hoses around—while providing the knobs brewers need to twist to keep it craft,” said Williams. Along with that flexibility, the system had to allow for expansion and handle several non-brewing capabilities, all with “an information-driven interface for non-technical users,” Williams said.
[sidebar id =1]The PlantPAx-based system uses Sequencer Object for sequencing control, Batch Scheduler for scheduling and starting times, and separate parameter values for non-brew operations including CIP. “The CIP sequences use the same Sequencer Object instruction as the brew process, since all the control functions are the same,” Williams said.
Instead of a separate CIP skid, the system “uses the vessels themselves as washing machines,” Williams said. “The process equipment has cycles to clean one, trigger the next, add caustic, etc. They can clean all four circuits at one time, which they couldn't do with a CIP skid.”
There are about 50 parameters associated with the equipment, and about 50 variables that can be used as recipe parameters, including CIP. “These are the ‘knobs’ they can turn to get the taste and characteristics they’re looking for,” Williams said.
“The displays are a compromise of grayscale for situational awareness, and color they wanted to make them happy,” Williams said. “Sequencer Object gives a very good, in-depth visual of sequencing, a powerful addition to the PlantPAx library.”
The power of a ControlLogix L72 processor and server-based FactoryTalk View SE HMI software allows for expansion. “The kettle is the bottleneck now, and they might add another, with more pumps and valves,” Williams said.
Flex IO, PowerFlex drives, Festo valve manifolds on EtherNet/IP and SQL tag storage round out the system specifications. “We use a spreadsheet tool to create an I/O list, and a routine builds the base PlantPAx program,” Williams said. “Then we can go in and configure the I/O. We’re able to do that without going into every routine, every add-on instruction. We can see it all in one picture and when we’re done, it becomes part of the documentation.”
Other features include collecting heat from the “knock-out” of the brew kettle. “The wort comes out at 190 °F, and has to be cooled to 60-70 °F for the yeast,” Williams said. “We’re collecting that heat and putting it back in the hot water system.”
Automated sequences are engaged based on differential pressures, and hot and cold water flows are balanced “so the water tanks don’t overflow,” Williams added. Batch numbers are being created for future reporting features, and historical data is being taken for when it’s needed later to come up with new brews, or to increase throughput or efficiency.
Lessons from the project include involving the customer early and thoroughly. “Chris was involved from the beginning, in the process of functional spec creation and through factory acceptance test (FAT), checkout, water batching and commissioning,” Williams said. This resulted in very fast customer ownership.
“PlantPAx provides an excellent interface with users, allowing them to control a process without a need to understand PLC programming,” Williams said, “And our use of development tools such as Excel creates a consistent and structured program.”
In the end, “No matter how much planning is done and how many meetings take place around the functional spec, there are always modifications needed and requested during startup,” Williams said. “Sequencer Object and PlantPAx makes those modifications very quick, often with no need to open a PLC program.”
[sidebar id =2]
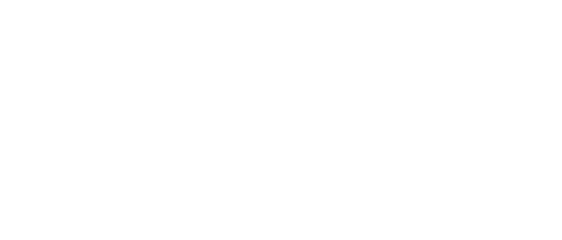
Leaders relevant to this article: