There aren't too many treats better than an ice cream bar enrobed in chocolate. However, if you're a safety engineer in desperate need of a useful solution, then a workable and easy-to-use safety system may be even more delicious and satisfying.
Gram Equipment in Vojens, Denmark, has been building automatic machines for making ice cream bars for almost 80 years, and is presently the leading supplier of large-scale equipment to the ice cream industry. However, there are many temperature parameters in the relatively slow process of making ice cream, numerous potential pinch points on its machines and other maintenance hazards. These constraints and ever-increasing demand from its own end users are why Gram recently needed to upgrade from running safety I/O points via DeviceNet to a more efficient safety system, but it needed some help to do it.
John Christiansen, Gram's automation manager, presented "Functional Safety Using GuardLogix—An OEM Customer Story" at this year's Safety Automation Forum on Nov. 10, the day before the opening of Rockwell's Automation Fair 2009 in Anaheim, Calif.
To improve the operation of its machines and also make them operate more safely, Gram implemented Rockwell Automation's GuardLogix controllers in 2005. Each machine employs two GuardLogix units, which communicate via the CIP Safety protocol and an EtherNet/IP network. This system also includes an RSLogix 5000 software and PanelView HMI displays.
"At the beginning of a scan, GuardLogix's one out of two (1oo2) processors check with each other that, for example, no doors are open, agree that no failure has occurred, and then this allows the machine's process to continue," explained Christiansen. "This is faster for operators to use because it enables quicker de-energizes and start-ups, and so it can save users many critical minutes." He added that Gram eventually saved about 41% on its engineering and testing costs on three lines it enabled with GuardLogix, and that GuardLogix was even cost-neutral from design to green-lighting of its initial testing.
However, before installing GuardLogix, Christiansen reported that a thorough risk assessment was essential to make sure that the new technology was deployed where it would be most needed and most useful. "Our risk assessment was so important, and it had to involve a varied and high-energy team, including many of our mechanical, engineering and safety people," he added. "This group said that doing risk assessment for the first time is like trying to eat an elephant, but the lesson there is to start with the filet, and the rest will follow and get easier as you go along. We also made sure to talk about risk and put ideas down on paper, but then also check out that they would work in the plant."
Gram performed its risk assessments in three main phases—assessment, risk control and risk review. "Using GuardLogix was very comfortable for us because we could step back, watch it function and then show the consequences of what we could do. Previously, we'd be faced with rewiring numerous relays like everyone else," said Christiansen. "Working with Rockwell Automation has been a real eye-opener for us, and really helped Gram move from traditional hardwired safety to full integrated safety controllers.
"If you're going to migrate to a new safety system, you have to go with state-of-the-art and safety standards-compliant systems. This is because, if it ever comes down to the courtroom, the question then will be was your system state-of-the-art and safety-compliant? There no question but that this is the case with GuardLogix."
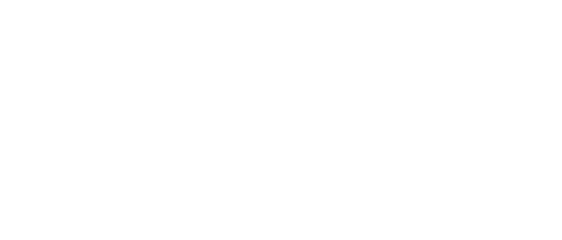
Leaders relevant to this article: