Rockwell Automation sets out strategy for extending its reach into the process automation mainstream . . .
For a company that has in the past been accused of failing to resolve the inherent conflicts between its hardware and software activities, the choice by Rockwell Automation of Ironmongers Hall in the City of London as the venue for a U.K. press briefing on its process automation strategy might fall into that ominous category of courageous. In truth however, as the headquarters of one of the Citys most ancient livery companies, with a history going back 700 years, Ironmongers Hall has about as much to do with ironmongery as Rockwell would have you think it has with the old style, push-the-boxes-out-the door, PLC business.
Thats the basis of the decision to bring together representatives of each of Rockwells recent process automation acquisitions―ProsCon, ICS Triplex and Pavilion Technologies―and its rather longer established alliance partner, Endress+Hauser, in a single press event designed to demonstrate that collectively they represent, not a succession of more or less random impulse buys, but integral pieces of an ongoing strategic jigsaw puzzle.
Not newcomers
That task fell to Richard Sturt, a long-time Rockwell U.K. marketing veteran and currently business development manager for process industries. Sturt argues, with some justification, that Were not new to process, pointing to the huge numbers of drives, motor control centers, motion control systems and PLCs it already sells, particularly into the hybrid end of the process market. As a result, he believes Rockwell doesnt have to introduce itself when it pitches for process control business because We work with these people every day.
What they do have to do, however, is to convince process industry users that they have a control platform which stands comparison with the best that the established DCS vendors have to offer and around which the new acquisitions can be clustered to form a whole that is greater than the sum of its parts. It has to be said that, on last weeks showing, its not clear that Rockwell itself, let alone anyone else, is entirely convinced that it really has that platform.
Instead, its overall approach is based on the argument, already made familiar by successive presentations from arch rival Siemens over the years, that, in contrast to the mainstream DCS vendors, what it has to offer is a common plant-wide architecture capable of integrating everything from the arrival of raw materials to the dispatch of finished goods. Theres no doubt that, as Siemens has demonstrated, its a compelling argument in a host of industries right across the hybrid market from food to fine chemicals, and Rockwell is now attempting to apply it in areas such as cement and steel, where the continuous element, while significant, is still by no means dominant.
Complete solution
Sturt gave as an example one potential customer faced with the near impossible task of supporting 23 different control solutions on a single site. We believe we can provide a complete solution, he said, adding, Theres no doubt that customers want it. And he reckons even doubters can be persuaded. For example, he said, when Rockwell lost a project to a DCS competitor two years ago, it was able to come back and win a similar project from the same customer just a year later.
Despite these successes, however, one cant help feeling that Sturt and his colleagues are being somewhat disingenuous. His key graphic, used both in the introduction to and the conclusion of the presentation, shows a continuum of automation applications from discrete through hybrid to continuous process, with the solid block of Rockwells presence across discrete and hybrid tapering off into the continuous end, but with successive alliances and acquisitions progressively extending its coverage. The underlying justification for that extension is, of course, that the process automation market as a whole is, according to most estimates, worth roughly twice as much as the discrete market. Given Rockwells acknowledged strength in discrete and the ever- present demand for growth, expanding into the process market is the best opportunity, said Sturt. In reaching that conclusion Rockwell is, of course, by no means alone―GE Fanuc, Mitsubishi and Siemens are all in pursuit of the same goal.
Is there perhaps a flaw in this argument, however? True, the process automation market as a whole may be attractive, even if the incumbent DCS vendors are unlikely politely to step aside. However, the real money is buried at the far end of Sturts continuum in up stream oil & gas, refining and petrochem, where the plant-wide integration model is arguably least compelling and where, in any case, the existing vendors compete as much, if not more, on their proven domain expertise as on the perceived marginal advantages of their respective systems.
Confusion
Moreover, there does seem to be an element of confusion as to whether Rockwell can indeed penetrate that end of the market or even whether it should be trying. On the one hand, Sturt and his colleagues argue that ICS Triplexs strength in oil & gas in particular will open doors for its new parent; on the other, both Sturt and his boss, Dominic Malloy, seemed to concede in subsequent conversations with INSIDER that they do not, for example, expect to pick up a major refinery project in the near future, although they believe that they have both the product portfolio and the expertise to handle such a project.
So why does Rockwell think it can succeed where other PLC vendors over the years have tried and failed? And has it in reality any chance of doing so without making a major acquisition aimed both at grabbing market share and filling what many perceive as gaps not at the periphery, but at the core of its process portfolio? Sturts answer is that Rockwell can already claim leading solutions in our own right and that we feel that the acquisitions we have made give us a world-class process control solution.
Precedents
Rockwell argues that its incremental approach is the surer route to success, and it cites ABBs experience at the end of the last century to highlight the problems of integrating DCS vendor acquisitions. But of course, thats not the only precedent―witness the consequences of Invensys failure to integrate its disparate acquisitions in the early days of this century. Its only a couple of months since we asked Invensys chief strategist and Honeywell alumnus Chris Lyden whether he was concerned at the prospect of new entrants from the PLC world attempting to break into the process automation market. Not at all, he answered, but I would be if they acquired an existing DCS vendor.
Some commentators including, most prominently, Jim Pinto, believe Rockwell is currently itself a potential bid target for, among others, cash-rich ABB. It would be ironic indeed if fear of repeating ABBs earlier mistakes prevented it from realizing its process automation ambitions and made Pintos prediction self-fulfilling.
- Despite the three process acquisitions, its the alliance with Endress+Hauser which has arguably done most to raise Rockwells profile as a serious process automation contender. As E+Hs Tony Grassby pointed out, the alliance is completely complementary with little or no overlap. Moreover, E+H on its own, with no significant system capability, nevertheless ranks in the top ten of the worlds automation vendors, while a combination of Rockwell and E+H would, according to the last time we did the arithmetic, rank sixth in the U.S. automation market and eighth worldwide.
That, however, isnt going to happen, at least as long as the current generation of the Endress family remains firmly in control. Nevertheless, its clear that the alliance is proving mutually beneficial, although whos bringing most to it is debatable. Certainly Grassby seemed to suggest to INSIDER that E+H is probably bringing at least as much business to Rockwell as its gaining. Nevertheless, he sees major benefits, most notably in the area of integration. Easy connectivity is the most important customer requirement, whether the protocol is HART, Foundation fieldbus, Profibus or whatever, he said.
Specifically, and despite the interoperability arguments made for fieldbus, he still argues that what customers are interested in is minimization of risk and Integration of devices from multiple vendors incurs risk of interoperability. Thus, one of the major benefits of the alliance is the ability to offer solutions that have been pretested to ensure proven and fully documented interoperability. For the end user, he argues, that means reduced control system development time and, hence, shorter time to market. To that end, the two companies have jointly invested in an Integration Office that proves the interoperability of solutions and creates preferred integration procedures in response to requests from a joint sales and marketing council. Nor is the integration activity confined to basic functionality. A key area has been the integration of asset management capabilities based on both companies commitment to FDT.
Acquisition integration
Less clear is how far last years acquisitions have benefited either Rockwell itself or the individual companies. Pavilion, for example, would undoubtedly be an asset to any company, although whether its ambition, as expressed by Robert Kranz, Pavilions former managing director for EMEA and current manager of global professional engineering services, to be the worlds leading model based software provider is enhanced by being associated with one particular system vendor may be debatable. Nevertheless, a company that can claim that 25% of all bio-ethanol in the U.S. is produced with its technology and that has particular strengths in such target industries as cement and polymers is certainly not going to impede Rockwells long term ambitions.
Less clear, even a year on from its acquisitions, is quite how ICS Triplex is going to fit into the overall scheme of things. Here there is an undoubted overlap, with Rockwell having its own safety solutions up to SIL2, which must to some degree compete with some elements of the recently introduce AAdvance. With the concept of integrated safety continuing to gain acceptance in the process sector, there is clearly a strong argument for an aspiring BPCS (Basic Process Control System) vendor acquiring a full-fledged SIL3 SIS (Safety Instrumented System) capability. The question for both Rockwell and its new acquisition, however, must be whether the BPCS is strong enough commercially to enable ICS Triplex to make the transition from third-party independence.
Finally, what of ProsCon, acquired, so rumor has it, to enable Rockwell to bid a major project from a pharmaceutical multinational that was subsequently lost and now described as Rockwells Process Technology Centre of Excellence? Certainly its expertise in such areas as batch, MES and what ProsCons Mick Horkan calls paperless manufacture can be seen as an asset, but whether the same can be said of its engineering and integration capability is more questionable. Specifically will the effect on Rockwells other integrators in the process sector of finding themselves competing with their own principal be to drive them into the arms of other vendors?
. . . and adds Incuity to its software portfolio
One of the final questions put to Richard Sturt at the end of last weeks Rockwell process presentation was whether there were still gaps in Rockwells portfolio and whether further acquisitions were planned in the process sector. Not surprisingly, he didnt answer, but it did give him the opportunity to reveal with a flourish the previous weeks announcement of a definitive agreement to acquire Incuity Software.
INSIDER readers have been able to follow the Incuity story since the summer of 2005 when, under its former name of DataWorks Systems, it announced Incuity HDA (Historical Data Access), described at the time as the only true upgrade for Wonderwares ActiveFactory 8.5. That claim had its origins in the fact that, while the DataWorks team had developed the original ActiveFactory and licensed it to Wonderware, that relationship had been terminated with effect from version 9.0.
In fact, the Wonderware relationship had its origins back in South Africa in the early 90s when the same team developed what subsequently became Industrial SQL server and was acquired by Wonderware. Shortly after the 2005 launch, DataWorks changed its name to Incuity and introduced its new flagship product, IncuityEMI (for Enterprise Manufacturing Intelligence).
Key milestone
Its that product, in its latest version 2.6, that is the focus of the Rockwell acquisition. Rockwell Software vice president Kevin Roach describes it as giving Rockwell the vital top layer in the information chain where the roles of the ERP vendor and industrial automation vendor meet and a key milestone in the continued expansion of our FactoryTalk software suite.
Incuity has much in common with Lighthammer, the MES vendor acquired by SAP in 2005, not least because Lighthammer also had its antecedents in Wonderware. This latest acquisition suggests increasing maturity in the MES space as both ERP and automation vendors recognize the importance of the convergence of the real-time and transactional worlds. Commentators such as ARCs Greg Gorbach and AMR Researchs Alison Smith believe that by acquiring Incuity, Rockwell has stolen a march not just on its automation rivals, but even on ERP vendors such as SAP as they seek to integrate more closely with the shop floor. The acquisition gives Rockwell Automation enterprise manufacturing intelligence capability that rivals―even surpasses―the likes of SAPs MII on many measures, and potentially positions Rockwell Automation to commoditize many of its traditional controls platform competitors by providing a control-platform-agnostic intelligence layer, said Smith.
Incuitys management team, including CEO Doug Lawson, and its employees are to become part of Rockwells Architecture & Software operating segment, although on past form quite how long some of them will stay must be a matter of speculation. In the meantime, many members of the distribution network Incuity has been assiduously building both in North America and further afield including, in the U.K., Duncan Fletchers Matrivue, may be wondering whether their sudden and new found proximity to Rockwell sits comfortably with their other relationships.
Fast Switch reemphasizes MTLs IS credentials
Cooper Crouse-Hinds subsidiary MTL has wasted no time in making good its assertion that its disposal of its MOST systems and I/O business to GE Fanuc Intelligent Platforms allows it to focus on its core businesses in intrinsic safety, fieldbus and industrial Ethernet. Last months Interkama show in Hanover, Germany, saw it announcing a series of significant developments. Add to that the news that Yokogawa has confirmed last months rumor that it is adopting the MTL/Byers Security Tofino product as its standard cyber security solution for the CENTUM CS 3000 and STARDOM control systems, and Cooper Industries £140m acquisition of MTL is beginning to look like the steal of the year.
Of the developments on parade at Hanover, by far the most significant, was MTLs new Fast Switch technology that allows the safe use of higher than normal power levels in intrinsically safe (IS) circuits, while continuing to meet certification requirements under existing standards. Fast Switchs particular contribution lies in enabling live maintenance of devices in hazardous areas by sensing the fall in voltage at the load when a break is made in a circuit, or a device is unplugged and disconnecting the load. As a result, it prevents the build up of voltage at the break which could otherwise generate an incendive spark.
Removing barriers
The simple and effective Fast Switch circuitry conforms to the principles of intrinsic safety and has been proven using the standard spark test apparatus according to international standards. It makes its debut in the MTL 9491-IS power supply, part of the 9400 Series of Intrinsically Safe Power over Ethernet or PoEx devices launched at Interkama. MTL believes the 9400 Series will remove significant barriers to the adoption of industrial Ethernet in the process industries. It allows live connection and disconnection of the end device in an industrial Ethernet installation in Zone 0 and Zone 1 hazardous areas, and as a result is claimed to reduce the cost of installing a LAN in a hazardous area by typically 40%.
Included in the series are a wireless LAN access point, managed Ethernet switch, copper-to-fiber media converter and serial gateway, all certified for mounting in Zone 1 with connectivity into Zone 0, together with a Zone 2 mounting IS Ethernet isolator and the associated Fast Switch-based IS power supply, which allows live power connection/disconnection without the need for a gas clearance certificate.
The serial gateway supports Ethernet connectivity for legacy IS series devices such as analyzers, displays and I/O, while the wireless LAN device provides hazardous area infrastructure for IS PDAs anywhere on a plant. MTL says the technology has already been proven in use in mining applications, but can now be extended to process applications under ATEX and IECEx certification.
MTL is also claiming a further first with the introduction of redundancy for FISCO (Fieldbus Intrinsically Safe Concept) protected Foundation fieldbus networks in hazardous areas. This enhancement to MTLs FISCO product range, first introduced in 2002, eliminates the risk of network failure in the event of the loss of a single power supply unit and meets end user demand for higher levels of availability.
- Yokogawas decision to adopt Tofino as its first industrial firewall for the Centum CS 3000 DCS and the Stardom network control system marks a major breakthrough for the MTL/ Byres Security developed technology, which both companies have been vigorously promoting to major system vendors for more than 18 months. The small industrially hardened devices are designed to be deployed throughout a facility, but centrally managed to provide a coordinated security solution.
- In Yokogawa systems, Tofinos will be placed in front of mission-critical control devices such as the Stardom controllers and CS 3000 sub-system interfaces and tuned to meet their specific security requirements. Yokogawa will thus be able to provide the multi-layer defense in depth, which is now widely regarded as essential. If companies want to meet the new ANSI/ISA-99 security standards, it is critical they divide up their plant operations into security zones and then protect each zone in the most appropriate manner, explained Byres Security CTO Eric Byres. It is no longer good security practice nor cost-effective to lump everything together behind one big firewall and pray that you are secure.
Sensing will drive process wireless market past $1 billion
Still not sure why process automation vendors are quite so excited about wireless? ARC gives part of the answer with its prediction in its newly published Wireless in Process Manufacturing Worldwide Outlook that the market for wireless devices and equipment in the process industries will grow at 32% a year over the next few years, breaking through the $1-billion barrier and reaching more than $1.1billion by 2012.
The continuous process industries have lagged behind discrete manufacturing in deploying wireless both because of the problems posed by its larger, outdoor sites and because of the specialist issues raised by hazardous environments. Now, however, says ARC, the picture is changing with the imminent arrival of standardized wireless sensing products and hardened wireless Local Area Networks (LANs).
Explosion in sensing
The report anticipates an explosion in wireless process sensing, currently a tiny proportion of the total market, but set to become the largest segment within five years as the result of a deluge of new sensing products compliant with either or both of the WirelessHART or ISA100 standards, both of which are based on ZigBee. The report repeats ARC senior analyst Harry Forbes previous assertion that the dramatically lower installation cost of wireless process sensing will cause the normal change-averse process industries to use it wherever they can, leading to more rapid adoption.
Less spectacular, but significant nonetheless is the rapid growth that ARC predicts in Wireless LAN usage, driven by the availability of new access point products that can be safely installed in hazardous areas and by the longer range and clearer signals of future IEEE 802.11n wireless. Forbes also sees significant potential for wireless in coordinating the huge numbers of different tasks, contractors, suppliers and materials involved in major equipment turnarounds for which ever-shorter outage periods are acceptable. Manufacturers in the process industries know that they need better visibility into operations that occur inside their own fence, said Forbes. ARCs end- user research indicates that manufacturers believe better visibility has huge potential value in the form of more consistent use of best practices, higher plant utilization and improved operational safety.
More wireless news
- Get used to Emerson trying to build on its WirelessHART lead by releasing a continuous stream of new devices, each of which will almost certainly claim to be the first of their kind. Most recent addition in this category is the Rosemount Analytical Model 6081-P wireless pH/ORP transmitter, which claims to reduce installation costs by up to 90% compared with traditional wired devices. Diagnostic messages available via HART include calibration error, high and low temperature warnings, glass failure, reference failure, ROM failure, sensor failure, CPU failure and glass and reference warnings. The 6081-P can be purchased alone or as part of Emersons Wireless SmartPack Starter Kit.
- Honeywell is promoting wireless as a cost-effective means of extending or replacing existing wired systems in process plant with the introduction its XYR 3000 wireless multiplexers. Part of the OneWireless portfolio, they support a wide range of legacy communication protocols, including Modbus and OPC, providing the means to connect existing wired instrumentation into wireless networks. Offering bi-directional communication for monitoring and control, they are being offered for applications in such areas as safety showers, tank-level monitoring, remote pump control, video monitoring, gas detection system connection and the addition of off-the-shelf sensors. Honeywell claims that the multiplexers can be deployed in less than 30 minutes, providing the means to avoid the costs both of conventional wiring on greenfield sites or of digging up and replacing damaged wiring in older facilities.
- Former Wonderware president Mike Bradley continues to build up his team at wireless technology pioneer Apprion by the simple expedient of raiding his previous company for talent. Bradleys own appointment earlier this year had already raised speculation that Wonderwares parent, Invensys, might be interested in a much closer relationship with Apprion than its current use of the latters technology. That speculation can only increase following the appointment of Mike Sullivan, formerly vice president of sales at Wonderware distributor Wonderware West, as vice president of global sales; of Rick Crider, former Wonderware vice president of strategic alliances as director of sales channel development; and as director of system integrator market development, Tony Bustamante, who held a similar position at Wonderware.
PI resorts to a lawyer to validate its node count
Its almost exactly a year since INSIDER last approached Profibus UK chairman Bob Squirrell in search of a reasonably reliable estimate of the number of ProfiNet nodes installed in the field. That follow-up to an earlier unsuccessful enquiry had been prompted by the claim that Ethernet IP and Modbus TCP had between them a 51% market share and thus, by implication, more nodes than ProfiNet. After a short hiatus, Squirrell extracted a response from Carl Henning at the Profibus Trade Organization (PTO) in the U.S. who, having asked his own series of rhetorical questions along the lines of What is a node? assured us that Well have an answer to define and accurately count ProfiNet nodes probably early next year. And well state our methodology (and what exactly were counting) then.
That promise seems to have been fulfilled with data released by Profibus International (PI) towards the end of last month, and its clear that PI has gone to some lengths to define what it means by a ProfiNet node― an automation end device with a ProfiNet interface―and what it doesnt ―Devices such as switches, hubs and routers; i.e., structural components of the Ethernet infrastructure, are not counted. Moreover, one suspects in an attempt to forestall any criticism from such quarters as the Fieldbus Foundation, it has made a significant effort to establish the objective credentials of the counter by appointing a notary to determine the number of installed nodes. Its also worth noting that, whereas other figures have previously been quoted on the basis of nodes installed and shipping, devices ordered or even, in the case of earlier Profibus data, of ASICS sold, this latest data mentions only installed nodes.
Outgrowing the market
As a result, PI is now claiming that the total number of ProfiNet nodes installed between its launch in 2002 and the end of 2007 was 1.14 million. ARC predicts an annual growth rate of 27.5% compound for the industrial Ethernet device market as a whole over the next five years, but PI deputy chairman Joerg Freitag expects ProfiNet to do significantly better than that and to increase its market share further. We estimate that 3 million ProfiNet nodes will have been installed by the end of 2010, he says. This corresponds to an average annual increase of 37%.
Arguably more surprising than the rate of ProfiNet growth, which might in fact have been expected to have been greater, has been the continuing strength of the market for conventional Profibus. According to PI, 2007 saw the highest growth ever of installed Profibus nodes with the number purchased in the year reaching an all-time high of 4.5 million. As a result, the total number of Profibus nodes installed reached 23.3 million by the end of 2007, comfortably exceeding the late Edgar Kuesters prediction of 20 million nodes by 2008. That success, however, hasnt done a lot to help former Profibus marketing chief Geoff Hodgkinsons prediction back in 2004 that the ProfiNet node count would overtake Profibus by 2010. With the difference at the end of 2007 a mere 22 million and with Profibus nodes growing at 4.5 million a year compared with ProfiNets current 420,000 a year its clearly going to be a year or two yet before that Hodgkinson prophecy is fulfilled. Indeed with Profibus doing to ProfiNet, what HART continues to do to fieldbuses in general, one cant help feeling that its time to put aside some of the rosy predictions for industrial Ethernet, let alone wireless, and look a little more closely at why users are so reluctant to enter the promised land. Cue further incisive analysis from Walt Boyes.
Meanwhile, what of specifically process-oriented solutions? Again, the Profibus data doesnt so much point to resounding success, as to the continuing resilience of nonfieldbus, or in other words 4-20mA and/or HART solutions. Thus, while the total number of Profibus nodes installed in what PI defines as process industry applications now amounts to 4 million, and while that figure grew by 700,000 nodes or 23% in 2007 ―almost exactly the same rate as Profibus nodes in general―Profibus PA devices increased by only 120,000 or 19% to total 750,000 nodes by the end of 2007.
Process failure
That seems to suggest two things: first, PA is pretty much level-pegging with Foundation fieldbus, for which the last figure we had was 800,000 nodes installed or shipping ,but second, and arguably more significant, that users who are quite happy to install a fieldbus solution in the non-process areas of their process sites are still reluctant to adopt the technology in continuous process applications requiring power over the bus and in hazardous areas. As has been pointed out a number of times before, that represents a failure for both PI and the Fieldbus Foundationespecially when one compares this level of success after so many years of supposed evangelism with the meteoric rates of growth achieved in the arguably far more contentious area of safety in discrete applications where, in 2007, PROFIsafe nodes increased by no less than 180,000 or 78% to 410,000 and PROFIsafe systems by 15,000 or 58% to 41,000.
One development that could further boost both ProfiNet and Profibus uptake is the release of the documents specifying the integration of IO-Link which, together with the existing physical layer and protocol specification, forms the basis for the wider deployment of IO-Link in both Profibus and ProfiNet systems.
Many sensor and I/O manufacturers have already introduced IO-Link products and some 30 companies have joined the IO-Link consortium. The IO-Link physical layer and protocol specification is fully independent of Profibus and ProfiNet, which means that IO-Link can be subordinated to any fieldbus or Ethernet-based system, with only the integration being specific to the particular bus. Work is currently in hand to define an appropriate independent IO Device Description (IODD).
Iconics presses home its Vista advantage . . .
Ever since PLC and DCS vendors began buying up small, innovative PC-based SCADA developers in the mid-1990s, industry watchers have debated whether it was possible to develop a thriving platform-independent software business within an organization primarily focused on moving its own hardware. Pretty much everyone whos tried seems to have found at some stage that theres just no way of stopping the hardware guys giving away the software to shift the boxes.
Its a subject open to endless debate, not least because, for example, Wonderwares relationship with Invensys Process Systems is vastly different from that of, say, the WinCC team to Siemens. What does seem significant, however, is that while the integrated vendors seek to extend their reach into the MES space either organically or through acquisition, it is the independents such as Copa-Data in Europe and Iconics in the U.S. who are actually driving the technology.
First Vista-based historian
Thats been most recently highlighted by reaction to the release of Windows Vista with Copa-Data first to market back in June of 2007 with a Vista-certified version of its flagship zenOn package, closely followed by Iconics with certification for Vista and Windows Server 2008. Now Iconics is rubbing that message in again with successive announcements first of the release of Genesis64, the latest 64-bit version if its HMI/SCADA suite, and second of Hyper Historian, claimed to be the first plant historian to be certified for Microsoft Windows Vista and Microsoft Windows Server 2008.
With the principal objective of reducing engineering costs, Genesis64 is described by Iconics president and CEO Russ Agrusa as the first product for manufacturing and automation to take full advantage of the growing popularity of 64-bit computing technology. As such, it ties into a host of Microsoft and Microsoft related technologies including the enhanced security features inherent in Vista.
Tightly integrated with SQL Server 2005 and 2008, the newly released Hyper Historian is claimed by Agrusa to be the the first 64-bit, real-time, plant-wide data historian in the market. It uses a robust swinging-door algorithm to achieve data logging rates of greater than 50,000 data events per second on reference machines. Hyper Historian is configured through Iconics Workbench Web-based development environment which also forms part of Genesis64 and provides integrated layout and project management and remote pack-and-go deployment.
- The latest release from Schneiders Citect SCADA/MES subsidiary is CitectSCADA Reports V4.1, which CitectSCADA global director Stephen Flannigan describes as the industrys most open historian. It is claimed to be unique―or at least unusual―among historians in using 100% Microsoft SQL Server 2005 as its embedded historical data store and provides multi-cluster support together with industry-standard connectivity via the OPC HDA Server. The standard offering comes with a range of pre-configured alarm management reports based on EEMUA 191 and an integrated reporting and analysis solution available out-of-the-box.
- Interesting phraseology from Siemens in announcing the latest version of WinCC: Rather than describing the universal scalable visualization system as Vista-certified, it says it now offers operation in accordance with Windows Vista. What that means apparently is, for example, that WinCC objects for operable elements have been adapted to provide optical responses with elements such as GIFs or displays changing color when touched by the cursor or displaying semi-transparently. Similarly, alarm and trend displays are available both in a classic version and in a new version based on Vista that allows the user to create individual buttons and run the export function from every control and to configure selections for display of alarms and trends online. Enhanced security includes prevention of the unintentional activation of Internet pages to avoid the potential risk of trojans while a new text distributor simplifies handling of multiple languages.
. . . while Yokogawa takes Vista into safety
Latest release of Yokogawas ProSafe-RS integrated safety instrumented system (SIS) is claimed to be the first major safety instrumented system to support Windows Vista. ProSafe-RS R2.01.00 is designed to integrate smoothly with the recently announced Centum VP DCS which itself is Vista-based. The combination enables the SIS to take advantage of Centum VPs ergonomic and intuitive operational environment, providing what the company claims is improved visibility of information and enhanced operability, with operation and monitoring of the DCS and SIS performed in a common operational environment.
As well as the new security features inherent in Vista, the new system enhances the security of PC components by restricting communications, controlling access to folders and the registry and preventing unauthorized access from outside. Yokogawa is targeting the enhanced system at emergency shutdown, fire prevention and burner management applications in the oil & gas, petrochemical and other process industries.
Windows Vista compatibility is also a key feature of the latest release of Yokogawas Stardom network-based control system along with support for AGA3, 7 and 8 gas calculations, a new data-logging function for the FCN/FCJ autonomous controllers and the addition of network templates to the engineering tool to improve the reusability of applications.
Innominate joins Industrial Defender program
Signs of European and U.S. cybersecurity specialists pooling their expertise comes with the announcement that Berlin, Germany-based Innominate Security Technologies has joined Boston, U.S.-based Industrial Defenders Industrial Defender Enabled Partner Program.. The program is described by Industrial Defender as enabling technology providers focused on the real-time process control/SCADA market to collaborate on expanding their technology offerings and providing comprehensive integrated cyber security solutions based on its Defense in Depth offering.
Innominates mGuard product line provides hardware firewall, VPN and virus protection which can be readily integrated into networked industrial systems, as well as enabling secure remote maintenance of industrial machinery and equipment. By joining Industrial Defenders Enabled Partner Program, we make it easier for our customers to utilize award-winning mGuard technology within a comprehensive Industrial Defender network security system, explained Innominate CEO Joachim Fietz. Customers requiring state-of-the-art security technology in combination with industry-specific expertise and experience in designing, deploying and servicing network security solutions will find that with us.
Monitoring
Under the program, partners undergo a comprehensive technology validation process which enables their devices to be monitored by the Industrial Defender Security Event Management (SEM) console, thereby enhancing the overall cybersecurity posture of the process control or SCADA network. End users who purchase the Industrial Defender (SEM) console can monitor all Industrial Defender Enabled devices on the network including Innominate mGuard devices from a single central console. The process manufacturing industries are increasingly looking to enhance their cybersecurity protection from a broad range of threats, both internal and external, commented Industrial Defender president and CEO Brian Ahern. By integrating Industrial Defender Risk Mitigation technology, Innominate is furthering its commitment to providing unparalleled network security tailored specifically to the global industrial market.
OPC Foundation focuses on integrators
The OPC Foundation has created a new program aimed specifically at aiding system integrators and distributors in the deployment of products from different vendors. The Foundations original focus had been on vendors developing shrink-wrap products and providing specifications, technology and certification to facilitate interoperability. However, this new program focuses on integrators and distributors who build custom systems from products from multiple OPC vendors and in particular their development of custom software that adds value by incorporating custom OPC components to complete integration projects. The aim is to meet end-user expectations for integrators to increase their proficiency in the use of the OPC technology by providing a mechanism and membership class under which they can design, develop and certify custom software. Initially, the system integrator makes the end user happy by putting together a system that consists of certified OPC products from multiple vendors, explained OPC president Thomas Burke. However, problems sometimes arise as small pieces of custom software are developed to extend the functionality, which then compromise the integrity of the system.
OPC gets the blame
Frequently, the OPC component is not developed exactly to specification and, when making things work together becomes difficult, it is often OPC that gets the blame. The Foundation wants this to stop, for the benefit of all, said Burke. So we are calling on the myriad of OPC system integrators out there who routinely use OPC to solve problems in the field to sign up and help raise the overall quality and reliability of OPC products.
The need is all the more urgent because of the launch of the OPC Unified Architecture that covers all levels of enterprise connectivity, including aspects outside the direct automation arena. We especially urge companies thinking of implementing an OPC Unified Architecture system to join us now, said Burke, so that end users do not become disillusioned with our next ambitious step into the future.
OPC Foundation membership fees have traditionally correlated with company annual revenue. However, because project values tend to be high in the automation business, a different pricing model has been developed and a new System Integrator & Distributor (SI&D) membership category created with a fixed membership fee of $1500. For this, the SI&D member gains access to OPC specifications and reference implementations (sample code) on which to base its products, together with the Foundations free Compliance Test Tools to self-certify its own custom OPC components. A special listing of SI&D members is to be maintained and end users will be actively encouraged to use members from it for their projects.
Supporting activities will include a fresh round of specialist SI&D training events and a series of webinars. Were also developing a certification scheme which will award successful attendees at our training classes Certified OPC Provider status, said Burke. We are now establishing a network of new Test Lab services to ensure top product quality and reliability, particularly for Unified Architecture components, and our goal is to ensure that all developers, including the new SI&D membership, take full advantage of the services we offer.
Latest from Home
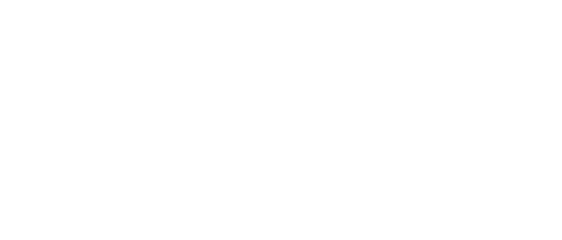
Leaders relevant to this article: