Stan: Last month we talked about how to get at the size of the opportunity in process control and how the first and last thing to do was tune the loops. Where do we go from here?
Greg: Well I am going to a rodeo, but before I get a view of the best of the West, I lassoed some ideas. What first comes to mind is the big reduction in batch cycle time of 25% or more for reactors and distillation columns by the simple addition of feedback control loops. Hopefully these stories have no similarity to extreme bull riding event I am headed to see.
Stan: Nearly all of the literature on process control is on continuous processes. This would lead one to believe it doesn’t apply to batch operations.
Greg: Also, the mode of thinking for batch is discrete and sequential. Even when loops exist, the batch sequence or conditional logic directly manipulates the controller output through the DDC, output tracking, or ROUT modes. While these preemptive actions can help get a loop started in the right direction or forestall problems, most of the time the actual output setting is an educated guess. The control loop needs to be set free to do its thing. The very terms “feedback” is the key to the advantage a loop has over a guesstimate of the coolant, feed, reagent or steam flow needed at a particular juncture in the batch. There are always unmeasured disturbances, whether they originate in the raw materials (concentrations), utilities (e.g. temperature), equipment (e.g. fouling), or valves (e.g. stick-slip).
Stan: A loop may need a good kick to get it going, but if it needs to be continually kicked, something is wrong with the kicker and/or the kickee. Therefore, most pre-positioning of control valves is momentary and judiciously used. Of course, once an interlock is activated, the controller output should be coordinated, and the manipulated flow held at the value consistent with the interlock.
Greg: The foremost example was a batch reactor being operated way beyond original design capacity because the product was sold out. The feeds were faster, and the total charge larger than the plant design basis. The exothermic reaction produced a gaseous byproduct that was recovered in an overhead system. The level would swell, and gases would burst into the overhead condenser and recovery system. The coolant and vent gas systems were pushed beyond their limits, particularly when the peak usage times of various batch reactors coincided or hot weather prevailed. As a result, the reactor’s interlock systems would momentarily have to shut off the feeds for any one a dozen different conditions, such as high condenser temperature, high vent system valve, high reactor volume and high reactor temperature and pressure. Override controllers were put on each of the process variables that triggered a trip. The output of the controllers went to a low-signal selector that set the permissible feed rates of reactants. The amount of time each override controller was active was displayed and historized for the operator.
Stan: One of the biggest challenges in the implementation of a sophisticated control system is keeping the operator in the loop. Consider “walking a mile in his or her shoes.” In designing the interface, diagnostics and metrics put yourself in the position of being responsible for operating a unit safely and profitably when you have no idea what the control system is doing. At the first sign of trouble, your tendency would be to put it in manual.
Greg: Fortunately, the operator display showed what each loop thought the feed rate could be and the time each loop’s output was selected for a batch. Of course, it helped that the reactor trips were eliminated and the cycle time was reduced by over 25%. Both of these results were very visible. It also made the operator job less stressful. The restart of a batch was a major headache.
Stan: An important takeaway is that an advanced control system will operate in its highest mode if the benefits and actions are clearly displayed and understood. Often improvements in yield or cost of goods by advanced process control (APC) are not so evident to operations, especially in the short term or tspan of attention (minutes to hours). Furthermore, APC must make the operator’s job easier—assist rather than interfere with corrections for abnormal operations—and keep the operator engaged. This last item is especially overlooked. Ideally, you want the operator to move to a higher level of supervision for optimization and abnormal situation prevention.
Greg: For this batch reactor application, patterns in the selected controller output (feed rates) started to become recognizable. The operator could tell when utility and vent systems were having problems and when the raw materials had changed. Also, it became readily evident that doing a good job of keeping four controllers from exceeding their set points (high constraints) could eliminate the need for eight of the override controllers. Starting with all the candidates is the right thing to do so you don’t miss a governing constraint if you have the right metrics.
Stan: Good APC applications increase and integrate process knowledge in their development and deployment and add to the process understanding during their operation. Some real-time optimization (RTO) and large-model predictive control (MPC) systems have failed in this last respect by making counterintuitive and unexplained moves to the process, creating discouraging transients in process performance. In some cases, a modeling expert would have to study the models, optimization criteria and operating conditions for a day or more to figure if the moves were right and beneficial from a longer term view.
Greg: Fortunately, my experience with the addition of loops to batch reactors and batch distillation columns did not have these issues, and reductions in batch cycle time were immediate and obvious. I have seen equal or better results from the application of a small MPC to batch operations despite the widely held academic opinion that batches are too nonlinear.
Stan: In many cases, the improvements resulted in a more intelligent selection and schedule of targets. It is important in an opportunity assessment to challenge every setpoint and not be deterred by “war stories.” Many reasons for not operating at a setpoint that increases production rate turn out to be no longer valid or can be addressed by an improvement in the automation system (measurements, valves, strategy and tuning).
Greg: Several examples come to mind where moving or adding sensors have increased plant capacity. The relocation of a pH sensor upstream of a heat exchanger in a recirculation line in a batch neutralizer reduced the batch cycle time by 25% by eliminating the overshoot of the end point and the associated manual sampling and addition of reagent. The addition of Coriolis slurry feed meters with centrifuge amp measurements for override control increased centrifuge production rate by 10% through a more complete and consistent basket loading. One of the great opportunities out there is the addition of bioreactor probes (e.g., capacitance, dissolved CO2 and NIR) and at-line analyzers with automated sample systems for broth measurements (e.g. cell density, glucose, glutamine, lactate, and ammonia). These additional measurements should enable feedback control of bioreactor batch substrate concentration, cell growth rate and product formation rate. To be part of this great future, we encourage you to become a member of the Adorable Automators Association (AAA). Here are the top ten reasons.
Top Ten Benefits of Adorable Automators Association Membership
(10) Travel discounts for exotic offshore plants—ride elephants to plants in Thailand
(9) Free admission to the Adorable Automator’s Hall of Fame—the hottest ticket in town
(8) Discounted admission to the Cinemax film “Famous Control Scenes” - 3D trend charts
(7) Special label underwear: “Freak in the Room”
(6) Fuzzy logic memorabilia: “Fuzzy is Cute” buttons
(5) Dating service - “Let us automate your pleasures”
(4) Simulation services - “Almost as good as the real thing”
(3) Calendar - “Adorable Automator of the Month”
(2) Souvenir T-Shirts - “My boss went to the ISA executive meeting and all I got was this shirt”
(1) Cowboy Hats - hardhats that can double as extreme bull-riding helmets.
This Month's Puzzler
What are the major sources of changes in the total loop dead time?
Send an email with your answer to the Puzzler, Control questions, or comments to [email protected].
Latest from Home
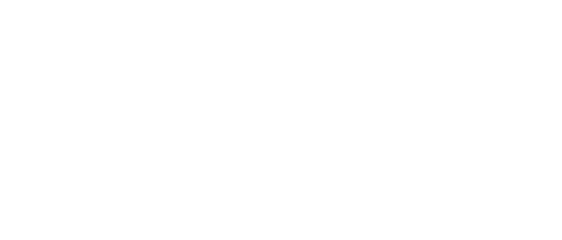
Leaders relevant to this article: