A total of more than 14,000 visitors were expected to descend on Chicago's new McCormick Place West for as Rockwell Automation's Automation Fair 2007 kicked off today.
He also indicated that key considerations for the industry include building machines for agile and flexible manufacturing; creating production optimization strategies; and building relationships with OEMs, system integrators and end users.
Brent Stromwell, managing partner and vice president of business development at Polytron, then offered his perspective on industry drivers, industry reactions and approaches, before introducing a variety of case histories that demonstrated the ability to adapt to changing conditions.
Stromwell identified seven drivers affecting the industry. They included food and product safety; workforce or labor; energy and transportation costs; informed, demanding customers; costs and competition; off-shored supplies and suppliers; and automation and information. We had the opportunity to do some research, he said. Food and product safety was the top issue. Second place was workforce, and third was energy and environmental resources. Three-quarters of the people who responded said theyre taking some action about food and product safety.
Trigger words like spinach, peanut butter and Taco Bell all conjure up risks, said Stromwell. Industry reaction to this includes increased quality checks, investing in tracking, investing in security systems and transferring costs to consumers.
The workforce or labor driver has created different industry reactions. Increasing expectations of employees, searches for higher-skilled resources, the need to increase competency levels of employees, and the retiring Baby Boom generation all are taking place, said Stromwell.
The industry is reacting to changes in energy and transportation costs by strategically locating distribution centers and manufacturing facilities closer to consumers, conducting energy audits and negotiating with energy suppliers.
The changing import lines of food and food ingredients are a large component of the off-shored suppliers and supplies. The world is flat, said Stromwell. Competition is coming from everywhere. Companies are analyzing risks associated with off-shoring, revising methods to track and monitor ingredients and shipments and including methods to check quality.
As a result of these drivers and reactions, Stromwell offered three approaches being taken by the industryexporting processes, importing labor or realigning automation and information. Exporting processes can increase energy needs like shipping and increase the risk of food integrity and exporting intellectual property, he said. By importing labor, there are issues of technical competency, work ethic, fundamental language skills, cultural hurdles and immigration laws and controls.
But with automation, we expect a higher degree of plant-floor competency, significant capital demands and increased process-knowledge requirements. He emphasized the need for better process understanding by plant-floor employees because the gears and wiring are no longer visible for diagnostics. Its all about checking the process with new automation.
All of these drivers and reactions and approaches are forcing companies to re-evaluate, said Stromwell. Its foundational that your HR department is where you start. Approaches are dependent on your main assetyour people.
Each groupmanagement, technical and operational employeesrequires a different strategy. Operational folks have a high turnover rate, said Stromwell. The demands for these people are increasing, and their technical knowledge base is increasing. For technical people, Stromwell noted no growth in engineering graduates since 1984 in the United States, despite a strong and increasing market demand for them. As a result, standardization is more critical, he said. Were requiring those folks on the plant floor to do more troubleshooting without our assistance.
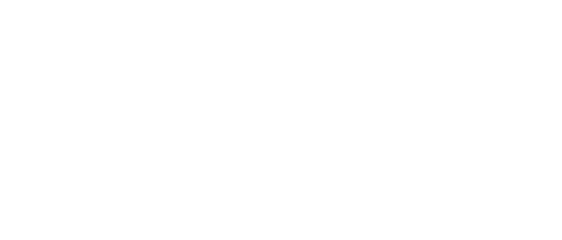
Leaders relevant to this article: