The Fieldbus Foundation website, www.fieldbus.org, offers a number of free technical documents and recommended practices. AG-181, the Systems Engineering Guide, offers some best practices for assigning devices to fieldbus segments, compiled in large part from the experiences of early adopters.
Those familiar with the origins of AG-181 know that the parts concerned with segment loading date back to the late 90s, when devices were testing to ITK-3 (Interoperability Test Kit-3, the mechanism by which device suppliers prove compliance to the specs and obtain their checkmark), and fewer than three major host suppliers were selling an H1 interface for their core DCS offerings.
Segment loading was based largely on loop criticality, and AG-181 puts forward a systematic way to categorize loops on up to four levels. The most critical loops (Level 1) are those where a failure typically a valve going to its fail position would immediately result in a major system shutdown, environmental release or economic loss a boiler fuel control loop, for example. The guide suggests that such loops should be alone on their own segments. Level 2 loops, such as boiler feed-water loops, are similar, the main difference being that they have an inherent capacity to allow swift operator action to avert a total shutdown.
The guide says the objective of segregating critical loops is to minimize interaction with the network. This segregation is done to reduce the likelihood that human error will disrupt a segment. With that in mind, those with excellent organizational discipline may choose a more liberal interpretation. Not at my site though Murphy lives here.
The other issue we consider when loading segments is how fast do you want to go. We normally put proportional-integral-derivative (PID) functions in valve positioners when a valve is the final control element. If another device is running the PID, it can be complicated to run the valve in manual when it the other device is being serviced. But the valve positioners of the 1990s did not solve PID equations terribly fast. 120 ms was not uncommon, and when adding an AO (analog output) and AI (analog input), each running at 50 ms apiece, trying to run a loop four times a second a 250 ms macrocycle was nearly impossible. Consequently, AG-181 advises a lightly loaded loop if a fast macrocycle is desired.
Whether any final control element can make a meaningful move every 0.25 seconds is open to debate. Most valves have an inherent first-order time constant of at least a second. Most are pneumatically actuated sliding-stem designs whose actuator diaphragms are at least a foot across. Theres also the matter of process noise noise thats a fundamental part of how we make a measurement. So we filter out this measurement noise with first-order time constants of 3 to 6 seconds or more. If we are filtering the measurement this much, and we know the final element will respond at best in a second, does it make sense to compute a new output four times a second?
Despite the limitations of measurement technology and final control elements, there may still arise cases where fast update times are necessary. Maybe the company that licenses your process technology wants to say fieldbus is too slow because of a study they did in 1996. Thankfully, most of the transmitters and positioners were getting these days show marked improvement in the execution times of function blocks. Many of these devices are now solving PID in 25 milliseconds (ms) less time than it takes for a typical compel data command on the fieldbus network. AI and AO are even faster: A macrocycle could be less than 100 ms assuming your host will support this, and the loops are very simple. In any event, a 250 ms macrocycle segment can now accommodate three control valves, again assuming the loops are relatively simple and dont interact significantly with each other.
Revision 3 of the Systems Engineering Guide, AG-181, is in the works, and will need to take the capabilities of recent-generation devices into consideration. If you are looking to apply Foundation fieldbus to a loop or loops where you believe fast macrocycles are needed, be sure to specify the speed you need carefully, since these capabilities are not equal among device suppliers.
Latest from Home
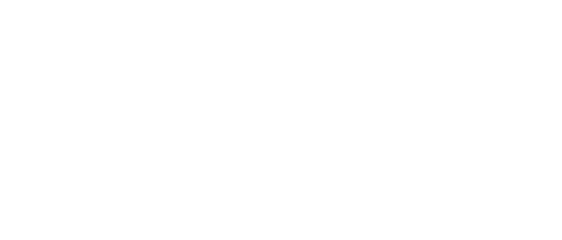
Leaders relevant to this article: