By David W. Spitzer, CONTROL Contributor
One of the cardinal rules of liquid flow measurement is to ensure that the flowmeter and its associated piping are completely full of liquid and that no noncondensable gas, such as air, remains in the metering run. Locating the flowmeter in a vertical pipe, configuring the piping so that the flowmeter remains submersed and orienting the flowmeter so it remains full of liquid can often eliminate noncondensable gases from accumulating in the metering run.
But what if the process itself has practical limitations that prohibit the elimination of noncondensable gases? Perhaps more perplexingwhat if the gas is a necessary and desirable component of the product whose flow you want to measure? In such cases, removing the gas is simply not an option. Doing so may make the product unsaleable. Yet the flow must be measured.
Jim Reizner, a flow specialist at Procter & Gamble, Cincinnati, Ohio, confronts this problem on a regular basis. Measuring the flow of shampoo is not that difficult. However, recent shampoo formulations include bubbles of air that enhance the appearance and hence salability of the final product in its translucent container, he explains.
Traditionally, ignoring the issue was the approach to measuring two-phase flows. This typically entailed installing a single-phase flowmeter that may or may not have had a correction factor to account for two-phase flow. Single-phase flowmeter suppliers often fostered this paradigm by citing theoretical performance without the results of testing under two-phase flow conditions. Other suppliers tested their flowmeters, but did not release detailed information describing the tests they did perform.
Measurement of two-phase flow involves the measurement of the mass or volumetric flow of the liquid phase, the gas phase or total flow. Applications exist for all permutations of these parameters. However, the total mass flow and the volumetric flow of the liquid phase where the gas-phase volume is relatively small are the most common two-phase flow measurements encountered.
Reizner adds, We are interested in assuring that the consumer receives the proper amount of product that is sold in volumetric units. Therefore, we need to measure the volume of the liquid phase accurately, so that we do not charge the consumer for bubbles.
One approach to solving the two-phase flow measurement problem is to remove the gas phase and measure the liquid phase that remains with a single-phase flowmeter. This approach adds cost and size to the installation and creates the secondary problem of how and where to vent the gas phase.
Two-Phase Coriolis Mass Flowmeter
Many two-phase Coriolis mass flowmeter problems involve accuracy degradation in certain processes.
(Courtesy Endress+Hauser)
In this article well limit the discussion to liquid flows containing entrained gas with phase distributions that exhibit bubble flow and slug flow. These phase distributions tend to be present in fluid flows with a relatively low gas-void fraction that travel at relatively high velocities. Identifying the phase distribution is not necessarily easy because the piping affects the type of phase distribution present. For example, bubble flow in a vertical pipe can change to stratified flow in horizontal piping because the bubbles tend to rise and form a large bubble at the top of the pipe as the fluid travels.
Coriolis Mass Flowmeter Issues
Single-phase flowmeters applied to two-phase flow include Coriolis mass, differential pressure, turbine, ultrasonic and vortex-shedding flowmeters. In theory, turbine, ultrasonic and vortex-shedding flowmeters measure the velocity of the entire flow stream. The velocity measurement generated by these flowmeters poses a fundamental measurement problem when the liquid-phase flow is desired because varying amounts of gas affect their measurements. Pressure effects create additional measurement problems. Coriolis mass flowmeters exhibit similar problems when they are used to measure the volume of two-phase flow. Differential pressure flowmeters are affected by density so that varying amounts of gas and its pressure also create measurement problems.
Coriolis mass flowmeters can accurately measure the mass flow of liquids or gases. In principle, Coriolis mass flowmeters to measure the total mass flow and fluid density to allow calculation of the flow of all of the permutations cited above. However Reizner notes that approximately 80% of flow measurement problems involve Coriolis mass flowmeters. Further, approximately two-thirds of Coriolis mass flowmeter problems involve some aspect of gas entrainment. In particular, higher frequency straight-tube designs tend to be more affected by two-phase flow conditions.
Nitrogen Padded Tank Causes Entrained Gas
A two-phase flowmeter sometimes can handle entrained gas in a padded tank.
(Courtesy Invensys)
Blake Howe, process engineer at Nestle Nutrition, Eau Claire, Wis., uses a nitrogen blanket to transfer oil out of a pressurized vessel. The amount of oil is totalized using a Coriolis mass flowmeter where the slug-flow feature detects oil flow and starts/stops totalization.
This was a standard practice the time that the instruments were installed. However, a new transmitter with two-phase flow algorithms can measure liquid flow directly and more accurately compensate for partially full pipe conditions that are present at the start and stop of the transfer process.
Stevens remaining applications, largely include high-solid slurries or higher-viscosity liquids that tend to trap gases. Some such products require air or gas in their formulation. Many of these applications can be improved by judicious flowmeter orientation and backpressure elements that reduce the effect of entrained gases.
Matt Watson is a senior process engineer at BASF, Louisville, Ky. He installed some Coriolis mass flowmeters in the late 1990s to charge batch reactors. In that case, Each material used one flowmeter that could feed several reactors. The original hydraulic design had design flaws that made the flowmeters subject to transient slug flow, entrained air and finely dispersed bubbles.
Watson says the sources of the problems included low levels and vortexing in the storage tanks and the inability of the flowmeter piping to remain full of liquid. The downstream control and shutoff valve piping created additional opportunities for the introduction and collection of air that adversely affected the flow measurement.
Even after remedying some hydraulic issues, the flow measurement system still occasionally faulted due to two-phase flow conditions, says Watson. Many flow tests were performed on the flowmeters that exhibited zero shifts of between 5% and 15% percent after two-phase hydraulic events. This was so problematic that flowmeter fault alarms were interlocked to flag events and stopped the filling operation. The net result was a system that could overcharge or undercharge the reactors because the flow measurement system was not tolerant of process faults that caused reliability, safety and quality issues. The introduction of Coriolis mass flowmeters that could measure with entrained gases provided a solution to our problemsalbeit at a high price. During the last year or so, we were able to justify, purchase and install three Coriolis mass flowmeters in this service. All have performed well in handling intermittent two-phase flow conditions.
By way of advice, Watson says to, pay close attention to the hydraulic design in two-phase or potentially two-phase flow applications because seemingly small details are important and can render an installation useless. In particular, try to keep the flowmeter full of liquid. If you cannot do this, install a flowmeter that is tolerant to two-phase flow conditions. Do not forget to consider carefully the hydraulics of the feed lines and valves to ensure that the flowmeter accurately measures the flow of material into the vessel and not the flow of material that fills or empties the pipes. In short, hydraulic design is critical but somewhat less critical now that flowmeters are available that can tolerate two-phase flow conditions. The availability of these flowmeters is not an excuse for poor hydraulic design.
Two-phase Correlation Flowmeter
Correlation flowmeters can measure the flow rate and gas void fraction for some continuous liquid-gas mixtures.
(Courtesy CiDRA)
Wade Mattar, consulting engineer at Invensys Foxboro agrees that traditional Coriolis mass flowmeters have their issues. In practice, measurement errors approaching 10% occur in Coriolis mass flowmeters under two-phase flow conditions with only 5% gas (by volume). Increasing gas volume in single-phase Coriolis mass flowmeters causes the energy required to operate the tubes to increase excessively and stall the flowmeter so that it no longer functions properly. Accurate measurement of two-phase flow under these conditions is not possible and can cause major process problems.
The Two-Phase Solution
Invensys researched this problem for almost a decade before launching its two-phase Coriolis mass flowmeter. Matter explains that, the key to measuring two-phase flow with a Coriolis mass flowmeter is to sense when two-phase flow is present and to what extent it exists. Doing so allows the electronics to adjust the energy to the tubes so that the flowmeter continues to measure flow and density without stalling. When the flowmeter does not stall, the phase distribution can be identified, and the electronics can compensate the raw flow signal to measure the mass flow and flowing density more accurately.
This type of flowmeter addresses the two-phase problem and actually measures two-phase flow. However, it does have its limitations, including limited size availability, pressure drop considerations and limited phase distribution applicability.
Endress + Hausers Stevens agrees that, Coriolis mass flowmeters need to recognize the presence of two-phase flow conditions and take action to ensure that the flowmeter does not stall. Coriolis mass flowmeters designed for two-phase flow typically measure bubble effect and plug flow. Each application is individually reviewed for applicability with regard to the fluid temperature, viscosity, velocity, bubble distribution and installation effects to determine the anticipated measurement accuracy. In particular, a more uniform phase distribution occurs in low-viscosity liquids flowing in vertical piping as compared to the same flow in a horizontal pipe where stratification might occur. Higher-viscosity fluids tend to exhibit measurement problems due to relatively poor bubble distribution at low velocities. Fluids flowing at higher velocity that use a backpressure element have better bubble distribution and exhibit less measurement error.
Stevens adds that uncompensated flow measurement errors can approach 40% of the measured flow in some services and installations. Overall, addressing two-phase flow issues means that the flowmeter design needs to be able to recognize flow changes. This is largely accomplished by using high sampling rates and robust sensor drive circuits to increase measurement stability. Digital electronics are designed to identify and accurately compensate for these changes.
Micromotions Patten agrees with the potential magnitude of the error, but states that, Coriolis mass flowmeters are relatively unaffected by two-phase flow when the presence of entrained air is approached as a transient condition. As such, the mass flow and density can be accurately determined from first principles when measurements are performed sufficiently fast.
Previous Coriolis mass flowmeter designs alarmed and turned the flowmeter off when air was present. This reinforced the notion that Coriolis mass flowmeters were not able to measure two-phase flows. However, current designs account for two-phase conditions so flow errors have been reduced from approximately 40% to less than 2%. Similarly, current designs allow the measurement errors associated with filling applications that start and stop with empty pipes have been reduced from approximately 2% to negligible.
Sonar-based correlation flowmeters can measure the flow rate and gas void fraction for continuous mixtures with up to 20% entrained gas (by volume). Dan Gysling, chief technology officer at flowmeter manufacturer CiDRA explains, Sonar-based correlation flowmeters use an array of passive pressure sensors clamped to the outside of the pipe to measure the mixture velocity to determine the flow rate and speed of sound through the mixture to determine the gas void fraction. Combining these measurements provides the liquid flow rate and gas-void fraction for two-phase gas/liquid mixtures operating in the bubbly regime. This eliminates many of the measurement challenges associated with applying single-phase flowmeters to two-phase flow.
Measuring two-phase flow in industrial applications is a perplexing problem. Using single-phase flowmeters to measure these flows has often been far from effective and has created additional problems and increased installed costs in many applications. Fortunately, off-the-shelf non-custom flowmeters designed to measure two-phase flow are available and can solve many of these problem applications.
Latest from Home
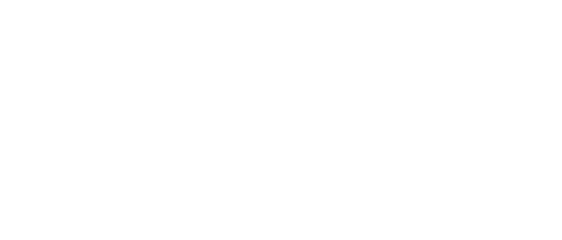
Leaders relevant to this article: