DO YOU ever get the feeling that your control system is hiding the secrets of the universe? After all, it’s supposedly gathering information from the process 24 hours a day. Unfortunately, you only get to see a small part of this information, and only when you go looking for it and have time to analyze it. What plant has the manpower or time to go hunting in the data haystack for information that might or might not pan out into performance improvement? At the same time, can you afford not trying to do whatever possible to improve your plant’s performance?
Michael Kennedy, global process control engineering manager for Columbian Chemicals Co. in Marietta, Ga., says, “In today’s global marketplace, there are enormous pressures to obtain the best overall performance from our manufacturing facilities.”
Performance Supervision Systems
Because it’s easier, given short staffing and a lack of time, many plants still operate on a “run-to-fail” model. That is, the plant runs until either a planned shutdown or an expensive, unplanned breakdown occurs. How expensive? Here’s an easy way to figure it out for your own plant. Find the value of the plant’s output per hour. Take a look at your last unplanned breakdown, and determine how many hours the plant was producing zero output. Multiply the number of zero-output hours by the value per hour of plant output. This gives you a value to put on the cost of the unplanned shutdown. In most cases, the value is very high, and can be a real eye-opener to management when presented as a real cost.
Thankfully, there are solutions to this extremely costly problem, but Kennedy advises, “Considering the limited number of skilled personnel, there are limits to what we can accomplish. In order to remain competitive, we need the right tools to streamline our process improvement, while adding a greater leverage to our existing knowledge and skills.”
One of these solutions is a software-driven Performance Supervision System (PSS). Because it’s software-based and uses your existing control system to operate, a PSS is often the least expensive way to reduce the costs of unplanned breakdowns.
PSS uses the DCS or historian as a window into the process, sorts through mountains of data, and delivers targeted, actionable knowledge about the process. Because it looks at the entire plant, PSS can find all manner of process, equipment, and control problems. Performance supervision has been used to uncover failing pump seals, problematic valves, fouling heat exchangers, improper repairs, process-upset sources, controller tuning problems, and process-behavior changes.
This information is used by process engineers, operations management, and maintenance, as well as the process control community. Every user can customize the information they want to see. Maintenance can focus on valve and instrument issues, while process engineers can look for bottlenecks and other improvement opportunities. At the same time, everyone is working with a standard set of metrics for overall performance, so the overall focus is clear.
Figure 1 below shows a typical display of the highest priority issues in a plant. In this case, the loop shown at the top of the list was identified as having the highest economic impact on the plant, based on a combination of its economic value and its measured performance. By looking at one chart, engineering efforts could be focused. As you’ll see below, drill-down tools enabled engineers to quickly find the problem, which was a series of interacting control loops. However, probably the most important thing PSS can find is time…your time.
Need More Time?
Everyone needs more time these days. Plant budgets are stretched, headcount is down, and everybody is balancing multiple responsibilities and multiple projects. When do you have the time to sit at the control console, and look for ways to optimize your process? Ian Nimmo, president of User Centered Design Services, says, “In a properly run plant, the operator should not have to intervene in its operation, except in the case of an upset, and any time the operator has to do anything it is an upset.”
If you’re spending all your time running around putting out fires, what will you do in a real emergency? In many plants, when multiple alarms go off together, the operators no longer know which are the most critical and which to respond to first. And in alarm cascades, plant operators that don’t know these things are usually going to do something wrong. We’ve seen this many times in many accidents, such as last year’s BP Texas City disaster. In that case, bad decisions were compounded by poor maintenance, which caused the deaths of more than a dozen people.
Installing PSS can help. Not only can it help you optimize the process, but it can quickly pinpoint problems that are just waiting to occur, including potential alarm cascades and maintenance headaches.
Process optimization isn’t way out there. It isn’t necessarily a set of arcane mathematical constructs. Most process optimization issues consist in finding loops that aren’t working properly, pumps with bad seals, or worn motors and shaft couplings. These are simple tasks, but they’re also time sinks. And, again, where are you going to find more time?
Fortunately, PSS can do this automatically for you. It’s watched the entire plant, crunched numbers, and found “hot spots” that need your attention. A custom report is delivered into your hands. You spend little or no time finding the problems, so you can focus on making improvements.
Need Good Answers?
Another consequence of fewer plant-floor people and lower skill levels is that it’s become difficult to get useful answers. “My institutional knowledge walks out of the plant every day at 4 p.m.,” says one process plant manager. An instrumentation engineer at a Lyondell plant recently told CONTROL that he expects his standard technicians to know much more than they used to, and that pay scales and training are lagging behind what they need to know to do their jobs. If you’re in maintenance, you probably have many stories of being asked to replace a perfectly good piece of equipment based on faulty information.
Wouldn’t it be better to follow a problem to its root cause before you spend time on repairs? In maintenance, time also is money, but the cost of replacing a 12-in. control valve when it doesn’t need to be replaced is real money wasted. One of performance supervision’s key benefits is that it helps you drive to these root causes, before committing all that money and time. By using visual, drill-down analysis and ad-hoc reports, you can quickly get through voluminous data and find some real answers. These also can help you justify using PSS to cost accountants that run your business.
Similarly, as Google has transformed the individual’s ability to find information on the Internet, the concept of performance supervision can help transform process optimization.
For example, Figure 2 below shows the results of drill-down analysis and user-defined reports. Several control loops are cycling at the same frequency. The supervision system has looked over the entire plant, saving days of analysis. The data shows, without any doubts, which parts of the process are associated with this problem, and which ones are not. In fact, PSSs often will correctly identify related problems in seemingly unrelated areas.
This is possible because PSS can automatically calculate process models. This allows users to pinpoint the exact timing of process changes, and track them to specific equipment changes, batches, or operator actions. This feature has been used to identify improperly-sized replacement parts. So, when a part was replaced, it was indicated when the process model changed.
“The performance supervision system identified over-sized valves as those with the highest process gain,” says Chris McAnarney, also of Columbian Chemical. “One valve had a process gain of 11. It was like trying to fill a shot glass with a fire hose! Fixing these problems reduced process variation, and helped to build the operator’s confidence that we could help make the plant perform better.”
Need Measurable Results?
High-level performance measures, such as cost, up-time and quality, have been tracked and historically documented for years, and have produced known benefits for plant optimization. Can those short-term performance measures do the same? Using a PSS, you can track and “historize” short-term performance measures that also fuel higher-level performance. For example, there’s a strong correlation between process oscillation and energy loss. If you measure, track, and drive down oscillation, you’ll reduce energy costs too. PSS will detect, track, prioritize, and report oscillations. In some cases, it will even identify the cause as valve stiction, load disturbance, or tuning.
Figure 3 below shows how focus on short-term performance measures can help move a plant to more stable operation. An intervention to improve the process occurred roughly half-way through this chart. The figure shows improvements in measures such as oscillation detection, percent of time in normal mode, and variability. Because the trends are normalized, it’s easy to interpret results.
Does this translate to bottom-line savings? Bet on it. Users are finding savings in energy, increased production rate, and reduced start-up time. PSS is aware of the relative economic value of different control loops, and can help guide you to those systems that deserve the most attention. Users of PSSs often report returns on investment in three months or less.
Call to Action
So, what should you do first? What about CMMS systems, asset-management systems, machinery-health-monitoring systems, and all the other ways vendors claim to improve plant performance? They all work well at what they’re designed to do, but it’s difficult to do much more than throw money at the problem if you’re operating blind.
Installing PSS can give you the information you need to tell you where, for example, it will pay most to install a machinery-health-monitoring system, or in what part of the plant an asset-management system will quickly pay for itself in improved performance, or where a CMMS system can best be used to reduce downtime.
The promise of open connectivity has finally been delivered, but many plants have yet to tap into it. After spending millions of dollars to put DCS systems in place, we are awash in a sea of data.
Fortunately, PSS does more than monitoring. It’s also analyzing, prioritizing, and recommending. It helps unlock the secrets hidden in your DCS. If you need more time, better answers, and measurable results, you need to think about a PSS.
About the Authors |
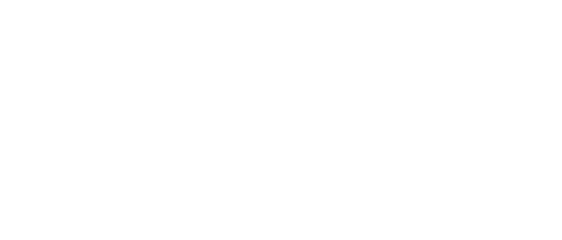
Leaders relevant to this article: