Connecting the world of process automation
Process automation is getting complicated, and it is moving quickly with new software systems hosted by multiple vendors, new field-instrumentation devices, and emerging protocols intended to welcome slow-moving process industries into the digital-transformation era. “We’re still at the infant stage of digitalization in process-automation sectors,” says Paul Sereiko, FieldComm Group director of marketing and product strategy, who shares his Industry Perspective on that changing landscape here.
A: Historically, the industry has been focused on simply creating something—creating gasoline out of oil or developing clean water. But over the past 10 years it has become engaged with digital transformation; the notion that all of this information from field devices and in your processes can be used to optimize your plant, get more return out of your assets, and do condition-based monitoring.
But you need to be able to access that information. What’s really changed in the last 10 years is taking the smart devices and making that information accessible to create a smart industry, a smart process automation industry.
Q: We’re reaching a point where we’re scaling these initial smart efforts and mainstreaming these tools. What does the near future look like here?
A: Process automation is an industry that moves slowly; we’re still at the infant stage of digitalization in many sectors. I like to talk a lot about oil and gas because many FieldComm Group members have large oil and gas businesses, and it takes a long time for them to adopt new technologies. They have a large installed base of instruments that support the HART communication protocol, which is one of the protocols that we manage and own. The effort in just getting information out of those HART devices, which had been really difficult, is getting a lot easier.
And when you’re doing new builds and upgrading your existing infrastructure, you want to make sure you’re adopting technologies that are built for the long haul. You want to buy the version that supports the new technologies and digitalization tactics.
Q: How does multi-vendor interoperability of instrumentation devices factor in here?
A: As the technologies become more complex, the registration, certification and testing associated with these products becomes more complicated. A big part of Field-Comm Group’s activity is the testing and registration businesses. So, if a host system is being used with instrumentation from any vendor that has gone through the test and registration process at FieldComm Group, you can be assured that you’re going to have multi-vendor interoperability.
This is unique in the process-automation industry and in the operational technology (OT) sector, as opposed to the IT sector, where you’re principally concerned that the packets are transported to the right place and in the right order. With OT technology we’re dealing with more “application-layer stuff” where you’re concerned about getting the right data and that it’s being read and interpreted correctly by both systems.
Q: How is the evolution of field instrumentation influencing the larger process automation industry?
A: This is all about IT/OT convergence, because previously all of these processes were managed by the OT organization, which was responsible for producing, say, 85,000 gallons of beer a day. The IT organization really had no influence there, aside from wanting to drink the beer!
But what you’re seeing now is converging OT and IT organizations that require common languages and models for communication. Consider OPC Unified Architecture (OPC UA), which is used by both teams to help transform data-digitalization and data transfer from OT silos into IT organizations to enable complex analytics, monitoring and alarming.
The bottom line—as instrumentation has grown complex and as we’ve reduced barriers to moving data, we’re experiencing a new world of advanced analytics, monitoring and optimization.
Q: What is your take on the debate between private clouds and public clouds for industrial-data storage?
A: What we see in the industries we serve, particularly oil and gas, is the closer you are to upstream operations, where you’re doing drilling and exploration, the less you want proprietary information in the cloud. You don’t want that available in the public domain. As a result, we’re seeing large enterprises build their own cloud-data centers.
The challenge is to recognize that there’s not one single cloud; the cloud itself is composed of many clouds. We have to define standards that take that into account and not be tied to any single platform.
Q: Let’s talk about the FieldComm Group and OPC Foundation collaboration.
A: We’ve worked with the OPC Foundation for a long time, but we recently collaborated with them on two specific initiatives.
The Process Automation Device Information Model (PA-DIM) is a way to structure information from process automation devices. It is adopted by organizations in the industry because it is a well-rounded standard that enables an OPC UA server to serve process automation device information to an OPC UA-enabled client that can read, structure and do analytics and monitoring on that information.
The second collaboration with the OPC Foundation is with their OPC UA FX initiative, which is the field-level communication (FLC) initiative within the OPC Foundation.
A few years back we independently started thinking about what a next generation process automation system might look like. For example, the OPC Foundation asked, “If two controllers were communicating using OPC technology, what standards and profiles would be needed within the OPC modeling framework?” Similarly, FieldComm Group asked, “If a device was speaking with a controller that was native OPC UA, what information model would be needed to implement the common use cases?”
So recently, we announced that the FieldComm Group working group addressing native OPC UA device-to-controller communication would now work within the FLC as part of a new instrumentation working group under the OPC umbrella.
These are both examples of how previously competitive organizations in the industry are now starting to collaborate, simply because of the growing complexity of the technology, both down at the field-instrument level and up at the systems level and the cloud level. You just can’t do everything on your own anymore.
Simply put, collaborations like this make it easier for end users to make decisions to adopt new technologies.
Ethernet-APL, the new two-wire Ethernet standard for device level communications in the process industries, is a great example. From a user viewpoint, there are 12 major suppliers and four standards organizations behind it. And guess what? It’s Ethernet, so I don’t have to decide between having a HART network here and a FOUNDATION network there and a PROFINET network somewhere else. It’s all Ethernet and you can run your automation protocol over it. You can achieve efficiency at a very high level as you’re not having to make a choice between competing standards.
If you think about it as an IT person who’s trying to build an analytics platform or a monitoring platform, you don’t care what the underlying communication protocol is, you just want to know the mass flow rate—whether it’s deviating from one unit to another, and why it might be deviating. You’re seeking the value in the information that the device is presenting. And we want to help make that job easier!
Latest from Industry Perspectives (sponsored)
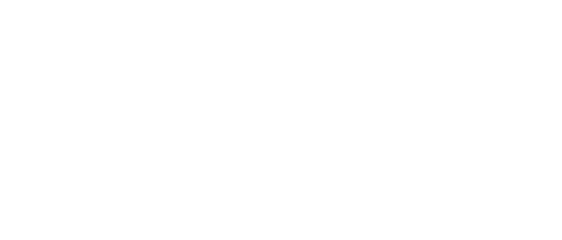
Leaders relevant to this article: