A half century of automation innovation
Next year, AVG Automation, parent company of EZAutomation, a midwestern U.S. manufacturer and factory-direct purveyor of industrial automation systems and components, will celebrate 50 years since its founding in 1975. The automation technology landscape has changed dramatically since that time, but many of the underlying industry needs remain unchanged. To learn more about what’s changed (and what hasn’t), Control caught up with Shalabh “Shalli” Kumar, AVG founder and chairman, at the company’s Carol Stream production facility in suburban Chicago.
Get your subscription to Control's tri-weekly newsletter.
Q: To get things started, perhaps you can share with us some perspective about the road you’ve traveled since starting AVG Automation now almost half a century ago?
A: AVG was founded in April 1975, and like you say, it has been quite a journey. I'm an electronics engineer, and new product development is my passion. The company was founded with the introduction of the programmable limit switch (PLS) that replaced rotary cam limit switches on a metal stamping press. Before this invention, it took two men two shifts to adjust and fine tune the timing of various functions such as feed and blow off in a press cycle for a particular die. Because of so much downtime to change over settings, the same part was often stamped for three or six months without a die changeover.
I thought of doing this electronically and the PLS was born, a whole new industry was created, and America changed the way metal stamping plants run. Now, die settings can be changed for a new part in less than 10 minutes. Applications for the PLS spread to the manufacture of metal cans, packaging plants, steel mills, control of water dams and even the gates of the White House.
EZAutomation was launched in 2005 in the midst of a sad and serious falling out with a former marketing partner. We had agreed to be the exclusive manufacturer of HMIs for them, but unfortunately, this partner copied our EZTouch series of HMIs to have them manufactured by another supplier in China. AVG sued, and in 2010, a Chicago jury found this former partner of ours guilty on 42 counts of breach of contract and misappropriating confidential intellectual property. Subsequently, both parties settled out of court. Today, the EZAutomation portfolio has grown to include more than 1,000 SKUs. Not only HMIs, but PLCs, I/O, LED message displays (marquees), power supplies, encoders, timers and proximity sensors.
Q: It’s clear that, despite running such a large and successful organization, it’s really the ability to create and bring to market innovative new solutions that both improve productivity and make life easier for our readers—and your customers—that satisfy your soul. Can you share with us some of the principles and priorities that guide your development efforts?
A: We were born in the Fisher Body metal stamping plants of General Motors, where two priorities were top of mind for the control engineers, maintenance engineers and technicians. Number one, to improve productivity. Number two, to reduce downtime. All my patents are geared toward addressing these issues, and in the process AVG developed five traits that are expressed in our products.
The first two include the highest processing power per cubic inch relative to other products on the market paired with the strongest immunity to electrical noise and conducted interference. That is what you would expect from a company born in automotive stamping plants. The third is the simplest human interface, and EZTouch is a legend in that respect. Number four is the highest reliability products. Our Uticor and Autotech products deployed 40 to 50 years ago are still running and producing American goods. Number five is highest operating speed. How about solving 40,000 digital setpoints in less than 20 microseconds?
Q: You’ve often spoken and written about the marked decline of American manufacturing since the turn of the century, and especially its migration to China, which today accounts for some 30% of the world’s products, including 60% of all electronic goods and 80% of automation products. But you’ve seen success producing automation products here in the U.S., and even some that outperform foreign competitors at a lower price. To what factors do you attribute this success?
A: First of all, there needs to be strong will and a commitment to make in America. Make no mistake, China is out there to become the sole superpower in the world by 2049, the 100th year anniversary of the current regime. They had a master plan to destroy American and European manufacturing industries, one by one with subsidized labor and factory overhead paid by the Chinese government from 1996 to 2008. They have waged an unrestricted war on American manufacturing, increasing our reliance on its exports, and stealing intellectual property and tens of millions of jobs.
Now, how AVG and EZAutomation can make and sell better products that are made in America as compared to those made in China at the same or lower price to the user is something of which we are extremely proud. I can’t give out all our trade secrets, but I will tell you that DFM, or design for manufacturing, is where it starts. DFM, highly automated production lines and selling factory-direct makes this seemingly impossible task easy, just like our name.
Q: One of the latest EZAutomation products that I think exemplifies innovative features that go out of the way to make products easier and more flexible to work with over their lifecycle is the EZTouch 7 Series HMI. It has truly innovative features that help to head off process downtime, which, as you’ve already mentioned, is a huge issues for process manufactures that sometimes don’t shut down for months or years at a time. With the Series 7 HMI, you can make configuration changes on the fly—or even swap out the display with minimal disruption to the process. Usually, you’d need a full-blown distributed control to do that. Can you tell us how you make that work in a touchscreen form factor?
A: Again, one of our core competencies is to reduce downtime in our customers’ plants. Because of that, we took another giant leap in the form of the EZTouch Series 7 HMI. The weakest components in an HMI are the touchscreen and the display. Operations may require the frequent pressing of a particular button on the screen, limiting the life of any HMI. Unlike the CPU and communication electronics, the touchscreen and the display are subject to the plant environment, such as oil fumes, dust, chemicals and the like. So, what did we do? We split the HMI into two parts, with the touchscreen and display housed in a front panel of the HMI and the CPU and the rest of the electronics in a back panel.
The two halves are connected through an HDMI cable running through a 3/4-in. hole in the door of the cabinet. There’s no longer a need to cut a big hole in the door. If the touchscreen needs to be replaced, it takes less than two minutes to disconnect the two and put in a new front panel. No need to program and set up the new HMI. No programming software or programming cable are needed. Further, the HDMI cable can now be 4-ft. long, allowing the backend electronics to be mounted away from the front-facing door of the control panel in a more convenient place in the cabinet.
The EZTouch Series 7 also shares the patented ability to edit displays, while online with the company’s other HMI and PLC products. Display graphics can be edited and updated without interrupting machine operation—even from a Wi-Fi-enabled PC up to 50 ft. away. We have dual memory system in all our HMIs. One is active, and the other, a back-up system, can be edited without shutdown, compared with the half-hour interruption required by competitive offerings. This is especially important for owners of new machines because studies have shown that the typical HMI user wants 10 display changes in the first three months of operation. And that means lots of money and lots of interruptions—if you don’t have EZTouch, that is.
Latest from Industry Perspectives (sponsored)
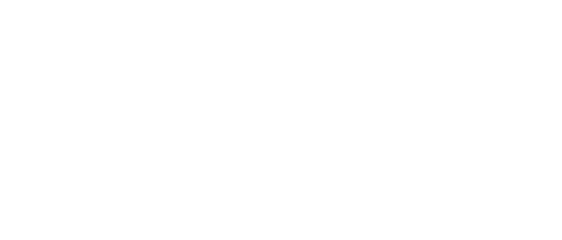
Leaders relevant to this article: