If you work in a process plant, you probably have had some frustrating experiences with analyzers. They’re vital to process measurement and control, but keeping them running can be a real pain. Why can’t someone make an analyzer that works as well and as reliably as a pressure, a temperature or a flow transmitter?
The problems with analyzers are twofold. First, the measurements that have to be made are often complex and frequently involve chemical reactions. Analyzing chemical composition is always going to more difficult than measuring pressure.
Second, many analyzer vendors have roots in making lab instruments for controlled and continuously monitored environments. Adapting these analyzers for on-line operation and field installation while making them rugged enough to not need daily maintenance has been too high a hurdle for many lab instrument vendors.
Now, new entrants from completely different industries are making their mark. For example, SpectraSensors was started in 1999 to commercialize products adapted from the NASA/Caltech Jet Propulsion Laboratory. Because the original products were designed for mission-critical aerospace applications, high reliability and low maintenance were a given.
The challenge was to adapt these aerospace-quality analyzers for industrial use and make them affordable. So, SpectraSensors focused on optical, laser-based gas analyzers for energy and petrochemical industry applications.
The company’s tunable diode laser (TDL) technology measures moisture and carbon dioxide. SpectraSensors also provides custom configurations for measurement of other compounds, such as methane, acetylene, ammonia, hydrogen chloride, hydrogen sulfide, carbon monoxide and nitrogen monoxide.
A leading application for SpectraSensor’s TDL analyzer is in refinery catalytic reformer units. These units convert naphtha streams into higher octane aromatic compounds that can be used in gasoline blending or chemical plants.
All of these compounds must be accurately measured and controlled, or their concentrations can increase until they poison the catalysts in the reactors. Hydrogen sulfide and ammonia must be minimized, while the right balance of moisture and hydrogen chloride must be maintained to extend the time between catalyst regeneration cycles and improve yields.
“All of the measurements can be performed on-line with TDL analyzers, which require less maintenance and are more reliable than previous methods,” says Bill Jenko, SpectraSensors’ director of process product line management.
“The most compelling is hydrogen chloride measurement, which typically is done manually with stain tubes, a handheld off-line measurement method subject to operator-induced variability. Some refineries use stain tubes to measure sulfur and ammonia as well. The ability to move these measurements from manual off-line to continuous on-line reduces operational costs, and improves the production of the reformate and the hydrogen,” adds Jenko.
Concentrations measured vary by application, but a typical dual-range analyzer might measure 0 ppm to 50 ppm and 0 ppm to 1,000 ppm moisture/ 0ppm–50 ppm and 0 ppm –1,000 ppm hydrogen chloride.
“Some plants have existing on-line analyzers for moisture measurement, but I haven’t heard of any other proven technology for on-line hydrogen chloride or ammonia measurements in these streams,” claims Jenko.
Jenko says TDL has some advantages that improve reliability and reduce maintenance. “TDL analyzers require no carrier gas or other consumable gases, and this lowers cost of ownership over other technologies. TDL hydrogen chloride and ammonia analyzers need a scrubber because they’re based on differential spectroscopy, but the scrubbers are the only consumable and typically last at least a year.”
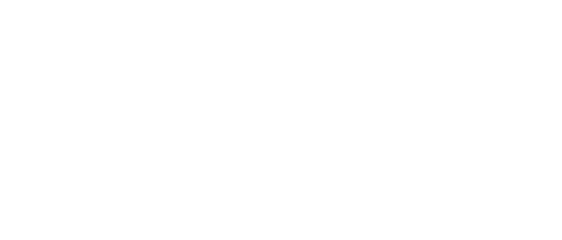
Leaders relevant to this article: