For additional online materials go to controlglobal.com/CT0712_procan.html
In the previous articles in this series,Ā (More about cost estimating process analyzer projects) we explored the lifetime costs of analyzer projects from the standpoint of savings through adequate scope development and estimating the fully vetted scope. Additionally, we spent time on safety and ergonomics for analyzer systems and analyzer shelters, especially from the standpoint of the analyzer technician who must service the analyzer systems daily. However, these activities are largely addressed in the engineering and capital construction phases of the analyzer project.
In this article, we shall explore how the ongoing operation and maintenance phase of the analyzer system is anticipated during project engineering and construction. We re-emphasize the distinction between analyzer systems and āconventionalā process instrumentation like pressure, temperature, flow and level. While the latter are relatively simple field devices, analyzer systems are often complex integrations of chemical, electronic and mechanical technology.Ā From this, we can conclude that analyzer systems generally require a higher level of technical knowledge from technicians and supervision.
Earlier in this series of articles, we approached reliability as encompassing the entire analyzer project from concept development to disposal, rather than as a mathematical exercise that would reduce the concept of āreliabilityā to calculations of mean time between failure (MTBF), root cause analysis (RCA) for failures, failure mode effects analysis (FMEA) and optimum levels of personnel and parts inventory. Although all of the aforementioned are important in reliability, it would be misleading to limit āreliabilityā to these activities.
Therefore, during the remainder of this article, we shall discuss how life-cycle costs associated with the ongoing operations and maintenance phase of analyzer systems projects can be addressed during capital engineering and construction phases of the project. This is important because certain costs related to operations and maintenance can be capitalized, along with the hardware associated with the analyzer project; others must be expensed. This distinction is important to the folks who must account for the analyzer system asset during its lifetime, and sometimes it also is important to receiving approval for the project. We note that ācapitalizedā refers to project costs that affect cash flow during the year(s) in which the analyzer system is engineered, constructed, and started up, whereas āexpensedā items affect cash flow each year during the life of the system.
Some of the ācapitalizeā or āexpenseā decisions may be left to the analyzer or project engineer; others, such as analytical hardware, are easy to label as capital items; other decisions may not be as obvious. This is a good time for the analyzer engineer to consult with project accounting to decide what is capitalized or expensed; this is part of due diligence, since the decision related directly to adherence to the Sarbanes-Oxley Act. For example, accounting rules often allow for the initial investment in vendor-recommended spare parts to be capitalized, but probably require subsequent spare parts, after commissioning and startup, to be expensed. Table 1 lists items which are typically capitalized or expensed.
It is important to differentiate reactive, preventive and predictive maintenance. Currently, most petrochemical plant maintenance and service is moving toward, or already is, preventive or predictive.
Reactive maintenance is typically described as āfix the analyzer system only when itās broken.ā This service and maintenance approach assumes the fallacy that there are no secondary costsāsuch as safety and environmental incidents, lost production, breakdowns of collateral equipment, overtime and callout costs, and contaminated product, for exampleāassociated with equipment failure.
Predictive maintenance is an important improvement over reactive and preventive maintenance because it avoids the secondary costs of reactive maintenance and the waste of predictive maintenance. Bob Call (See Analyzing The Relationship Of Preventive Maintenance To Corrective Maintenance) suggests a 6:1 ratio of preventive (predictive?) maintenance to reactive maintenance, because predictive maintenance often reveals some type of reactive work to be done on an asset.
Analyzer maintenance can incur unnecessary costs because, for simplification, it treats āidenticalā analyzer systems identically. For example, one process chromatograph may measure hydrogen in a clean gaseous stream and another apparently identical chromatograph may perform a similar measurement in a liquid stream laden with residual tars. Therefore, the analyzer system on the gaseous stream, under preventive maintenance, may incorrectly be assumed to have the same maintenance requirement as the analyzer system that can be contaminated by tars. This is an example of preventive maintenance that can result in reactive maintenance, when predictive maintenance would be superior because the latter anticipates actual failure.
Extending the example of the two chromatographs from the previous paragraph, predictive maintenance would distinguish the two analyzers with the chromatograph on the gaseous streams as requiring predictive maintenance perhaps monthly and the chromatograph on the tarry stream requiring similar service as frequently as weekly.
Continuing the example of preparing for lifetime preventive maintenance for a new chromatograph system, according to the Ramon Vorne article referenced in the sidebar, we must identify key performance indicators, or KPIs, that quantify waste, provide an early warning system for analyzer system failure, and provide information as to where improvements should be made. KPIs should be current or forward-looking metrics. The referenced article by Bob Vavra add that the key is to extract useful information from the KPIs to improve business and operating profitability.
Atkins and Rehaja suggest beginning the development of predictive maintenance procedures with a session including operations and analyzer maintenance personnel in a failure mode effects analysis (FMEA) to document what has gone wrong or can go wrong with the analyzer system. Paul Gruhn suggests that a similar team approach should be used for the Management of Change (MoC), which is usually required for analyzer projects. Most reliability texts provide guides and data sheets about FMEAs, or go to website www.isixsigma.com/tt/fmea/. The KPIs should emerge from the FMEA exercise. Table 2, taken from the Patton article, offers possible predictive maintenance information to include in a computerized maintenance database of equipment records. Table 3 offers possible KPI measures for the performance of ātypicalā gas chromatograph system. A more complete list of suggestions for the analyzer system database and KPIs can be derived from the lists of engineering and maintenance, plant, analyzer system vendor and safety lists in Battikha.
Gary D. Nichols, PE, is a principal control systems engineer at Jacobs Engineering Group. He can be reached at [email protected].Ā
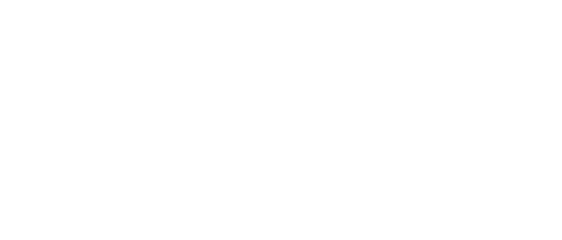
Leaders relevant to this article: