At our most recent AutomationXchange event, 32 end-user organizations participated in a frank discussion of the state of the analyzer market. This end-user-only meeting revealed a glaring need for reliable, accurate and reasonably priced online analyzers.
End users have long been deploying measurement devices on basic parameters, such as pressure, level, temperature and flow. These devices are reliable and accurate. Standardization and resulting intense competition among suppliers have reduced prices to a few hundred dollars or less per device.
Low prices and solid performance have caused end users to find new applications for these devices, creating a virtuous circle of increased demand, lower prices, more increases in demand and still lower prices.
But when it comes to analyzers, the circle is vicious instead of virtuous. Suppliers see little demand for most analyzers, so production runs are limited and prices are high. Limited field experience gives suppliers little real-world feedback data, hampering improvements to reliability and performance. End users see high prices, poor reliability and questionable performance, so they limit their analyzer purchases to must-have applications.
It is easy to see why the analyzer market doesn’t work for end users, but it is harder to find a solution. Clues can be found in one small part of the analyzer market that is improving rapidly.
Analyzer sampling systems used to be like online analyzers: custom-built, expensive and unreliable. The New Sampling/Sensor Initiative (NeSSI) has addressed these issues by simplifying and standardizing sample system design.
The primary objective of NeSSI was to reduce the cost to design and build process analyzer sampling systems by 40% and the cost to own them by 35%.
Goals were met, and end users are enjoying reduced design time, faster assembly, easier installation and reduced testing and commissioning time. Because NeSSI is a standard, multiple manufacturers build interchangeable components that can be mixed and matched like industrial Lego systems. Standardization has reduced costs for end users and increased vendor sales by over 50%. A virtuous circle has been created.
Manufacturers fear standards because they think interchangeable products will create commoditization, but NeSSI has shown that standards can increase sales by such a tremendous amount that the overall market improves for both end users and suppliers.
End-user analyzer applications run the gamut from simple to esoteric. Larry Megan, the manager of advanced control and simulation R&D at Praxair, wants to replace measurements that typically require a gas chromatograph or a mass spectrometer with simpler devices. He is also interested in online and reliable measurements of hydrogen, carbon monoxide and carbon dioxide to parts-per-million levels.
Users from Kraft Foods expressed a need for analyzers specific to food applications. “We need online sensors for food color, flavor and degree of cook,” said Kraft Fellow Vijay Arora.
Rineco Chemical’s analyzer applications are for anaerobic bacteriological systems, including optical measurement of cell density in a highly gassed fermentation process.
Most of the end users I talked to said analyzer suppliers were not meeting their needs, but John Davidson, senior automation engineer at Bristol-Myers Squibb (BMS), had a success story to tell.
BMS implemented and validated a NIR moisture analyzer in a fluid-bed dryer to measure moisture levels in a final product. This online measurement eliminated lab testing, saved time and money, and increased accuracy.
According to Davidson, the only ongoing concern is that analyzer maintenance and calibration is difficult and critical. Davidson credits success to the fact that BMS knew its product inside and out prior to analyzer implementation.
[Editor's Note: To hear the discussion from the AutomationXchange analyzer meeting, click the Download Now button below, or right click to save the MP3 file for later listening.]
Podcast Length: 24:00
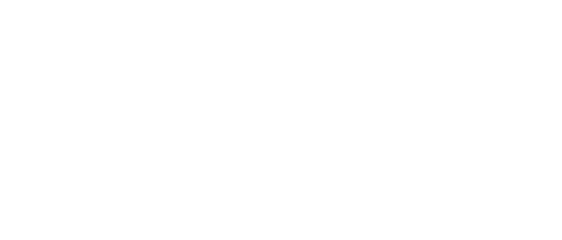
Leaders relevant to this article: