By Jim Montague, Executive Editor
Sometimes you can't see the forest for the trees, and other times you can't see either of them because your vision has grown too blurry. But you may not notice it until you get new eyeglasses and see the clarity you've been missing.
Similarly, to many eyeballs, most of the measurements, variables or processes in control and automation don't stay consistent or in tune for long. As a result, there's just one task more important than sensing and controlling a process application's basic parameters, and this is calibrating that application's instruments, controls and networks.
"We use field calibrators, such as those from Martel Electronics (www.martelcorp.com) and Fluke (www.fluke.com) for all kinds of biochemical batches to monitor and verify temperature, pressure, flow and agitation. I've been using them for 40 years, and they've all gotten better during that time. We used to have separate calibrators for different functions, but now they've combined functions and become a lot more digitized. This has been helpful because there's less hysteresis with digital than with analog calibrators," says Bruce Schmeck, an instrument technician at Merck & Co. Inc. (www.merck.com) in West Point, Pa. The facility produces vaccines like Gardasil that protects against human papillomavirus (HPV), which can cause cervical cancer.
Mental Block
However, despite the advantages that field calibrators can bring to process applications, many people don't use them—some because they don't realize their advantages, and others because they don't want to take the little extra time they require.
For example, Beamex Inc. (www.beamex.com) surveyed close to 2,000 process industry professionals last year and found that 9.9% aren't calibrating their fieldbus instruments, while 13.5% in the oil, gas and petrochemical sector don't do it either. This problem may be caused partly by the 43.1% of the respondents in oil and gas who use a semi-manual calibration management system, while another 15.3% say their calibration management is still paper-based. Only 22.8% in these industries report their system is managed by specialized calibration management software.
"Accuracy and traceability are crucial for compliance with pharmaceutical manufacturing, FDA, EPA and other standards, but I know managers who still don't grasp how important it is to keep after calibration," says Schmeck. "Everyone wants to go the cheapest route these days. They'd rather rather run at risk for a little short-term gain, instead of calibrating and making much bigger gains in the long run. They just don't know how much better it could be. When you use field calibrators, you take a process that you hope will be good and turn it into a process you know is good."
Implementing Education
To combat this ignorance, many field calibration advocates are educating potential users about how to gain its advantages. "Field calibration is still a big paradigm shift for many people because so many processes were historically managed with the seat-of-the-pants methods," says Ned Espy, Beamex's consulting director. "And, though many technicians in the U.S. use field calibrators, the subject isn't in the curricula of a lot of engineering schools. That's why some technical, vocational and community colleges are offering courses on calibration. For instance, Coosa Valley Technical College (CVTC, www.coosavalleytech.edu) is partnering with Georgia Power on an instrumentation technology curriculum, running their people through it, and also making it available to students just out of high school. I think about 40 suppliers, including Beamex, Emerson Process Management and Yokogawa Corp. of America, have donated equipment to Coosa Valley's program that opened last year."
Espy adds that education on field calibrators is vital because so many process instruments and their associated networks are growing more complex. "The old three wires for three separate instruments are being replaced by multivariable transmitters or flowmeters that measure flow, temperature and differential pressure, and also perform compensating flow calculations using static pressure and temperature," says Espy. "Now everything is in one instrument, but users must learn to calibrate the resulting 4-20 mA output signal as three separate indicators. Multivariable transmitters are more accurate and stable, so users may only have to test them for an hour once every couple of years. However, they still have to get out of reactive mode and get into proactive mode to make sure it gets done."
Figure 1: A technician at Mazovian Gas Co.'s plant in Lodz, Poland, uses a Beamex MC5-IS intrinsically safe multi-function calibrator to check its gas conversion equipment to ensure precise delivery of and billing for natural gas.
For example, Polish Oil and Gas Co.'s (PGNiG) Mazovian Gas Co. reports that it's using Beamex's MC5-IS intrinsically safe, multi-function calibrator to calibrate about 750 instruments at its Lodz plant, which produces and delivers about 4.3 billion cubic meters of natural gas to 386,000 individual clients and 350 large industrial firms in the province (Figure 1). Most of the plant's instruments measure pressure and temperature, and they're usually calibrated twice each year with the MC5-IS, which makes automated calibrations and stores all results in its memory. Calibration reports can then be printed out using Beamex's calibration software. "Customers want to pay for the exact amount of gas they've received, so our gas conversion devices must be extremely accurate," says Jacek Midera, Mazovian's instrument specialist. "Most importantly, accurate measurements and calibration ensure proper billing. Calibrating is crucial because the impact of even a small measurement error can be tremendous in terms of lost revenue."Coaxing Cooperation
To help convince still-reluctant colleagues and managers of the value of field calibration, Schmeck says advocates should sell its value and educate others about its benefits.
"In pharmaceutical manufacturing, we stress that calibration can mean better batches. In power generation, calibration can help producers waste a lot less electricity," explains Schmeck. "We use field calibrators at Merck because they make monitoring much easier and because we can have far fewer items breaking sterility. For example, it's much easier today to take one multi-function calibrator into a sterile setting. In the past, we had to break sterility to take an instrument out of production, bring it to a shop, bench calibrate it and break sterility again to reinstall it."
When deciding where to use field calibrators, Jim Shields, Fluke's field calibration product manager, says that potential users need to identify critical tags in their applications; define the appropriate intervals for performing calibration; make sure they're not compromising safety; evaluate process quality and maintenance costs versus returns to the process; examine cost optimization; weigh environmental and non-compliance costs; and identify other tags and longer intervals between calibrations. "You must also evaluate the software and associated calibrators available to do the job. This is not always a one-size-fits-all proposition. All the software packages for managing calibration have different strengths and weaknesses," adds Shields.
Configuration is Not Calibration
Besides talking up calibration's advantages, some users and suppliers find they also must educate potential users about the fact that initial configuration doesn't mean calibration. "The biggest problem we face is when someone sets up a transmitter or loop in the field and thinks that using a handheld communicator to set it up means it has been calibrated. It hasn't been calibrated, but this problem happens a lot," says Tom Fatur, Martel's president. "For example, they may configure a transmitter to transmit at 0 psi to 500 psi, and then think they can walk away. However, they must also verify that it's working properly by hooking up a field calibrator to introduce a simulated physical parameter. "
Likewise, some suppliers may imply that their transmitters or other equipment are more stable than they actually are, and so need less calibration or less maintenance than they actually do. "A salesperson may come in with a new pressure transmitter and guarantee that the electronics won't drift for 10 years," explains Schmeck. "Now, he hasn't actually lied, but the user may not have asked the right questions, because the diaphragms on that transmitter will definitely change over time. So while the electronics may not change, the performance and readings will drift. You can't not calibrate a transmitter for 10 years, even though the sales pitch may make it sound like you can. Most transmitters need to be re-calibrated once per year."
New Realms, New Requirements
Though some process control technologies are shrinking as automation and PC-based control take over, it's likely that field calibration is going to become more important because it gives automated systems an essential connection to real-world operations and is the foundation of precise data on which all their calculations. are based. Plus, calibration helps deliver the documented accuracy and traceability that more applications will require in the future.
"I used to work at a chemical plant, and if the resins we made didn't make the grade, we could just reuse the materials," explain Schmeck. "In pharmaceuticals, if a medicine doesn't meet all the criteria required during each step, we have to throw it all out. So even though calibration is more important in pharmaceuticals now, I think it's going to become more important in other industries. For example, in the U.S., we're trying to find all the natural gas we can, and this is opening a whole new realm of instrumentation and calibration. Also, we're going to have a lot more wind and solar power applications, and they will need instruments, monitors and calibration too." Oh, and get an eye exam.
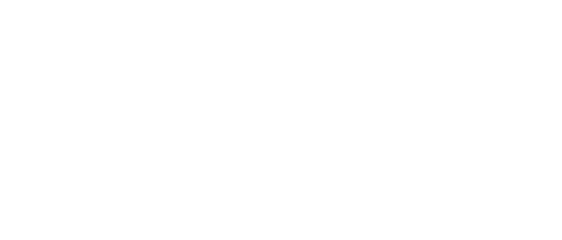
Leaders relevant to this article: