THE HART Communication Foundation recently released the latest update to its HART protocol. Version 6 enhances HARTās ability to meet needs of modern asset management solutions that track the health of field devices. Users worldwide are paying more attention to their field devicesā condition because they know more than 60% of requested maintenance is unnecessary, and that more than 80% of all automation maintenance is spent on field devices, while only about 2% goes to host control systems.
The Inertia Effect
When asked how asset management systems will affect how work is done, recently retired automation professional Terry Molloy, PE, replied, āIām familiar with all of these issues you raised questions about, as I got to suffer through this process in the 1970ās as we moved from pneumatics to electronic instrumentation in the utility industry.Ā As I used to say when making presentations to students about our industry, āWe use state-of-the-art technology with fifteen to twenty years of proven reliability.āā This statement sums up the sentiments of several respondents though there are several companies in the resource sector who are making serious attempts at overcoming inertia.
Wilfred Hartmann, an engineer with one of the largest chemical companies in Europe confirms Terryās sentiment since his field calibration tools continue to consist of field voltage/current meters, mA-calibrators, mA-simulators, RTD-calibration, level detectors, ultrasonic flowmeters, and handheld configuration tools for HART-signals. However Hartmann continues, āIntegration of calibrator signals in a Central Maintenance System (CMMS)? Hmm, why? Normally only temporary information is of interest. Explicit calibration is normally not done in the field (lack of accuracy of field calibration tools or bad calibration conditions) or documented elsewhere (paper certificate).ā
So even though the calibrator companies are rushing to put the ability to interface with the CMMS, some industry professionals are wondering whether the gains talked about at the beginning of this article are real. If they are real, there are just as real hurdles that must be overcome, on either end of the wire, to make the data from calibrators useful to the enterprise.
Leaping the Hurdles
HART devices typically have an ASIC to contain all the information on its capabilities and functionality. Because of this, they normally require a complete instrument replacement to add new features or capabilities. The host systems do not have the ASIC limitation so they will be able to take advantage of HART 6 as soon as the appropriate software release becomes available from the suppliers. Because HART 6 is fully backwards compatible with all existing HART installations, there will not be any impact on the installed base.
Of course, if a new field device is necessary to obtain HART 6 features, the question posed by Jim Sprague, a member of CONTROLās Editorial Advisory Board, and an engineer at a major Saudi Arabian oil company, says, āWe should be concerned about this issue, especially with FF coming on strong.ā
Jim Sprague says, āOur company -- and I believe the Middle East in general -- is woefully behind in integrating smart instrument calibration & verification systems into our central maintenance systems.ā
āThe biggest problems are,ā Sprague continues, āthat we have a wide mixture of installed smart instrument protocols.Ā In our refineries, gas plants, stabilizing plants, and many GOSPS, we have mostly Honeywell DE & Foxboro FoxComm instruments, with a smattering of Yokogawa Brain, HART, and now FF. Thus, any calibration system has to be developed at a plant basis, rather than company-wide.Ā Iāve seen Druck, Fluke, Loveland, Beta, and many others being used (and not used) in our plants.āĀ
Furthermore, Sprague notes, āThere is no legislation here (yet) forcing us to develop a centralized recordkeeping system.āĀ
āWe seem to have lots of supervisory turnover in our plant maintenance organizations ā it seems to be stepping stone to other jobs,ā Sprague goes on. āPlus maintenance is a stepchild, with only functional ties to our engineering organizations, so they donāt get the central direction needed for change,ā he concludes.
Wilfred Hartmann, of the worldās leading chemical company, adds to this list of impediments the additional requirements for a calibrator to be, āExplosion proof, and have a battery or rechargeable battery power supply.ā
Coming Soon to a Calibrator Near You
The three main manufacturers of portable calibrators, Emerson Process Management, Beamex and MTS will soon incorporate the capabilities of some or all of the new HART 6 however until these features are available at both ends of the wire they will be of little value to End Users. Therefore, just like any new technology it will be up to the End Users to vote with their wallets and purchase the equipment with the features they require.
How HART Works
Simlar Like most communication protocols, the HART protocol also follows the OSI 7-layer model using layers 1, 2 and 7, and is based on the Bell 202 telephone communication standard and operates using the frequency shift keying (FSK) principle. The digital signal is made up of two frequenciesā 1,200 Hz and 2,200 Hz representing bits 1 and 0, respectively. Sine waves of these two frequencies are superimposed on the direct current (dc) analog signal cables to provide simultaneous analog and digital communications. The digital communication signal has a response time of approximately 2ā3 data updates per second without interrupting the analog signal. A minimum loop impedance of 230 ļļ is required for communication.
The bit stream is organized into 8-bit bytes that are further grouped into messages. A HART transaction consists of a master command and a slave response. Media access consists of token passing between the devices connected to the channel. The passing of the token is implied by the actual message transmitted. Timers are used to bind the period between transactions. Once the timer expires, control of the channel is relinquished by the owner of the token.
The Application Layer, Layer 7 defines the commands, responses, data types and status reporting supported by the Protocol. In addition, there are certain conventions in HART (for example how to trim the loop current) that are also considered part of the Application Layer. While the Command Summary, Common Tables and Command Response Code Specifications all establish mandatory Application Layer practices (e.g. data types, common definitions of data items, and procedures), the Universal Commands specify the minimum Application Layer content of all HART compatible devices.
To learn more about the HART protocol, you can complete the on-line tutorials and Download the HART Application guide on the HART Foundation web site.
Whatās New in HART 6
HART 6 adds the following new features to the existing HART protocol:
- Device Variable ClassificationĀ (Required)
Provides master applications with a simple mechanism to determine the number and type of process related variables (pressure, temperature, etc.) that are available within a device. A key enabler for many HART 6 improvements, this mechanism provides master applications with considerable information about device capabilities. (Commands 0, 8) - Extended Device StatusĀ ( Required)
One additional byte of well defined status information with Command 0 and new cyclic data access Command 9. This new Extended Device Status byte is in addition to the current device status byte returned with each command response. Provides additional device status alerts such as āDevice Needs Maintenanceā plus more. (Commands 0, 9) - Device Variable Status (Required)
One byte of well defined status for each Device Variable returned by new cyclic data access Command 9. Enables field devices to self-validate and report on the quality of the data in the command response (good, poor, bad, fixed) plus more. (Command 9) - Long Tag (Required)
This new Long Tag with international (ISO Latin 1) characters allows consistent implementation of the longer tag names required by many industry users. The specifications currently reflect the length of this tag to be 32 characters as outlined in the Long Tag proposal approved by HCF members in January 1998. However, the recent discovery that some existing I/O systems will not āpass-throughā the 32 character tag, may cause the number of characters to be reduced in the final specification. The need for this new Long Tag is unquestioned. Only the number of characters is being reconsidered. (Commands 20, 21, 22) - Configuration Change Counter (Required)
Improved mechanism for master applications to determine that a field device configuration has been changed. Protects integrity of plant configuration databases. (Command 0) - Device FamiliesĀ ( Optional)
Establishes standard commands and status indicators for devices based on the type of process connection. Standard commands allow simple master applications to more fully communicate and configure devices without having to rely on the complexity of DDL. Initial Device Families for Temperature and PID Control are included in the specification package. The Valve Positioner / Actuator Device Family is in final preparation. - Transducer Trim Commands (Optional)
New Common Practice commands for performing transducer trim (calibration) operations.Ā Reduces need for device specific commands to perform this common function.Ā Standard commands make it easier for master applications such as field instrument calibrators to perform calibration functions on all HART devices. - Sub-Devices (Optional)
A simple mechanism using Common Practice Commands to support āHART device within a HART deviceā functionality. Potential uses include flow computers and multi-channel temperature devices. - Block Data Transfer (Optional)
An updated mechanism to support the movement of large blocks of data between masters and field devices. Potential uses include the movement of diagnostic information stored in the field device and upload/download of device configurations. - Catch Device Variable (Optional)
A simple mechanism using Common Practice Commands to support the sharing of process data between field devices on the same HART network. Allows a listening field device to capture process data from another field device to be used in calculations such as tank gauging, flow computers or PID control functions. - Write Device Variable (Optional)
New Common Practice Commands to support forcing the digital value for any Device Variable to a specific value to aid in commissioning and troubleshooting. - Lock Device (Optional)
New Common Practice Commands allow a master application to lock the ālocalā front panel of a field device while performing remote configuration functions. - Squawk and Find Device (Optional)
New Common Practice commands to support commissioning and troubleshooting of HART devices in multi-drop and multi-pair cable installations.
Ā About the Author |
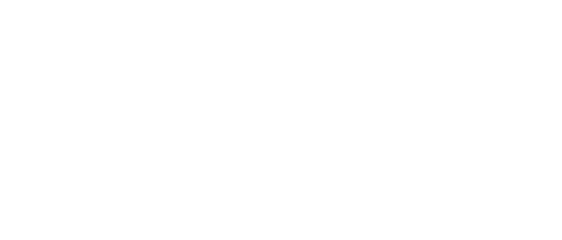
Leaders relevant to this article: