By Anil Sharma, Essar SteelINDUSTRIAL AUTOMATION technology for the process industries is changing at the speed of light, enabling companies to respond to industry trends and market opportunities while continuing to meet quality and compliance requirements.With these advancements in technology, distributed control systems (DCS) in turn have become more intelligent and can now detect very minute disturbances in the automation process without affecting plant operation.Recent studies and personal observation, however, show that merely investing in the latest automation controls technology does not guarantee the expected benefits, until and unless its applications are fully utilized. Yet there are so many applications and functions within today’s control systems that many go unnoticed and unapplied.Process is identified as having one or more variables associated with it that are important enough for them to be controlled. And of all the process parameters in the process industry, temperature is one of the most important. Temperature is the one parameter that doesn’t change drastically even in the trip/startup mode or during adverse conditions. Its rate of rise and fall is always linear.The Power of VL
In any process application, a DCS is an integral part of the automation process, performing many functions depending on the process requirements. In a DCS, there are many alarm check functions that detect abnormalities in process signal and input signal converters. Some of these functions include Input Open Check, High/Low Alarm Check, Deviation Check, and Velocity Check. Yet one of these functions, Velocity Limit (VL), which can be used to detect and take corrective action against faulty signals, is not being used as much as it should be.This article will outline the power of VL functionality and explain how it can be used to avoid false alarm tripping, especially when related to faulty indication of temperature and level. The VL function is very much suitable for faulty indications of these two parameters, as these don’t change drastically with the process.
In any process application, a DCS is an integral part of the automation process, performing many functions depending on the process requirements. In a DCS, there are many alarm check functions that detect abnormalities in process signal and input signal converters. Some of these functions include Input Open Check, High/Low Alarm Check, Deviation Check, and Velocity Check. Yet one of these functions, Velocity Limit (VL), which can be used to detect and take corrective action against faulty signals, is not being used as much as it should be.This article will outline the power of VL functionality and explain how it can be used to avoid false alarm tripping, especially when related to faulty indication of temperature and level. The VL function is very much suitable for faulty indications of these two parameters, as these don’t change drastically with the process.
To avoid plant alarm trips because of faulty indications of temperature and level, utilize the VL function already existing in your DCS.
Temperature loops are very critical for steel industry plant operations, and faulty indication from any of these loops can trip the process and make it unstable. One such loop is the discharge temperature of a process gas compressor, which is the heart of the process. Gas is compressed in two stages. Suction temperature of the gas is brought down from 300 deg. c to 50 deg. C by passing it through different cooling arrangements. Suction pressure is around 400 mBar in normal load conditions, and final discharge pressure is 2.0 Bar. Flow through the compressor is approximately 100KNMdeg. 3/Hr. Gas discharged from these compressors becomes the feed gas for the reformer.The range of the temperature instrument is 0-100deg. C. Suction temperature is approximately 50deg. C, and discharge temperature is maintained at about 70deg. C with the help of spraying water. Discharge temperature is important from the point of safety of the compressor, and process also demands that temperature should be within limits so as to maintain the chemical composition of the gas. This indication comes to the DCS as a trip value; output from the DCS goes to the PLC through NDO, which actuates the relay and thus trips the compressor. This, in turn, trips the complete process.The cause of faulty indications are many. They may be attributed to faulty RTD assembly, some loose connections in the loop, problems with the barrier, problems with the transmitter, or problems with a particular channel/loop in the DCS, to name a few. Because of any of these reasons, the temperature indication may start fluctuating. When it reaches the trip value, it actuates the NDO and trips the compressor. After a 10 second delay, trip value is 90deg. C and alarm comes at 85deg. C. The rate of rise in this particular loop is 5deg. C/min. in extreme conditions. If there is no problem in the loop, it will take approximately three minutes to reach the trip value if the extreme condition is 75deg. C.But why not sense this fluctuation and use it to avoid faulty tripping? If fluctuation is more than 5deg. C, the value I had assigned for VL, the instrument comes to the calibration mode and thus the PV value gets held up at the value assigned in the calculation table. This prevents the NDO from actuating, and thus the logic remains healthy in the PLC and avoids tripping the process.The operation of VL depends on the process. Setting smaller check time intervals makes it possible to detect smaller changes. If an alarm is generated, the alarm status continues at least until the next checking time interval.Providing one more element in the same line will help, but this is not applicable in the normal running of the plant. It requires a plant to shutdown, purge the lines, and make the provision for another tapping, which is impossible under normal running condition of the plant. Moreover, there are often limitations in the DCS to accommodate extra loops.To avoid plant alarm trips because of faulty indications, I assigned a value of 5 for VL to sample the PV, computes the change during the scan period, and generates an alarm if the change were to exceed +/- 5deg. C of the process value in one scan of the DCS.If there is an actual problem in the process, the rate of rise in temperature will be linear and will not occur abruptly. It will not occur at more than 5deg. C in one scan of the DCS. So the actual tripping will not be bypassed, but instead can be taken care of by the operator if it is not immediately possible to rectify the problem in the stipulated time the plant trips or shuts down. But if there is a problem anywhere in the loop -- such as loose connections, cables, particular channels of the DCS, or primary sensing elements which will cause indication to fluctuate – or if temperature fluctuates by 5deg. C or more in one scan of the DCS -- this particular loop comes in the calibration mode. This is done in the sequence table in which the condition of VL loops in the calibration mode holds the PV to the value which was there at the time of detection of fault in the loop by 5deg. C or more. This prevents NDO from actuating and thus logic in the PLC remains healthy, avoiding the trip and alarm. Operators are alerted that a particular instrument has come in the calibration mode and that there is a problem in the loop of a particular instrument.I assigned a safe PV of 70deg. C in the calculation list, which becomes the PV of this particular loop if it comes in the calibration mode. The idea behind keeping this value in the calculation list is to ensure that faulty indication does not trip the compressor. If PV is fluctuating near the trip value and is sensed by VL at that time, that same PV will take hold and will actuate the NDO, which will actuate the relay in the PLC and thus trip the compressor. The value assigned in the calculation table ensures that any fluctuation of 5deg. C or more throughout the range of the instrument (0-100deg. C) will put the instrument in calibration mode. PV will be 70deg. C, which is below the trip value and thus will bypass the faulty indication.The safety of the equipment/plant is in no way bypassed in this application. The instrument in calibration mode will show if there is a faulty indication and will point out if there is a problem somewhere in the loop of that particular instrument. If there is, the genuine indication will trip.The moment that particular instrument comes into calibration mode, an alarm will alert the panel operator. False trips not only add costs to the company, but also disadvantages associated with them, as it takes a long time for the process to become stabilized again.No doubt there are many other methods to avoid trips due to faulty indication, including monitoring the quality of the instruments, redundancy, etc., but no one can be sure of perfect instruments in the complete loop. So why not utilize the VL function already existing in your DCS to avoid faulty indications and trips of temperature and level?Advantages of VL Over Other Systems:
- PV and VL allows 100% surety that any fluctuation will put the instrument in calibration mode, as there is no other instrument involved in between. It also rules out any time delay in taking the corrective action ,as only one system is there in which both the data are processed.
- No extra instrument is required to detect the fault.
- Does not affect the operation of the existing DCS system, as it does not require much memory for application of this function.
- Operator cannot change the value assigned to VL as this can be changed only in the engineering mode of the DCS.
- PLCs can be utilized for this application, but are not as sensitive. A PLC doesn’t handle the same number of tasks as a DCS does, so it cannot concentrate in solving logics.
- In the process industry it happens many times that by fault another instrument is checked, in this case if by fault it is done that instrument will come to calibration and thus will avoid tripping and will warn the panel operator.
- If there is any loose connection in the complete loop, the instrument will come into calibration because of the fluctuation in the PV.
- VL has an edge over the IOP, which vendors normally supply with the system. The instrument goes to the fail safe value if IOP when the PV reaches the extreme values. It will not detect the readings in between. Normally the trip value is within the range specified, so by the time IOP is detected, the instrument reaches the trip value and thus actuates the NDO and trips the process.
- Whereas VL detects any fluctuation throughout the range of the instrument, if any fluctuation is detected the instrument will come into calibration mode and thus avoid tripping the process.
About the Author |
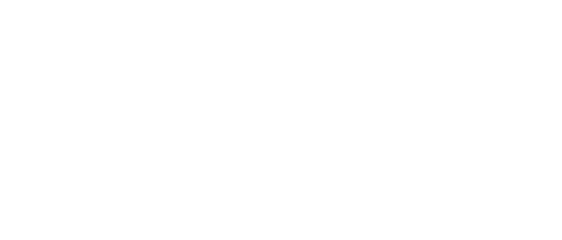
Leaders relevant to this article: