A |
ccurate instrumentation ensures accurate measurements that keep processes under control, prevent waste, and may protect human life as well. Field calibratorsalso known as handheld calibratorslet engineers and technicians apply secondary calibration standards to devices and instrumentation without having to lug around heavy equipment. Todays field calibrators work hand-in-hand with software, logging essential data when technicians use them on site. The software receives the original device data from the calibrator and provides it to the handheld calibrator when its time for the technician to make additional site visits.
Measuring and Calibrating Current Loops
Electrical engineer John Gale is responsible for the development, design, programming and engineering of industrial control, data acquisition, and continuous emissions monitoring systems for ACS, Inc. (www.acs-acs.com, Bellingham, Wash.), a company that designs and manufactures incineration and scrubber systems. Some of ACS systems have 24 current-loop inputs and 12 current-loop outputs that must be calibrated at commissioning and during routine maintenance and calibration intervals. To verify the accuracy of the equipment under calibration, Gale typically had to go through each loop several times.
GOES BOTH WAYS
Using Flukes (www.fluke.com, Everett, Wash.) ProcessMeter (Figure 1) which combines the functions of a traditional multimeter with a current loop calibrator, Gale reduced the time needed to calibrate the systems. In addition, on site visits he was able to eliminate one piece of equipment as well as extra batteries and test leads. With more than 30-years experience in the electronic/electrical industry, Gale has used several manufacturers meters and finds the ProcessMeter to be rugged, accurate, reliable, and with its large display, easy to read.
Smart Manometer Calibrator
BC Group International (www.bcgroupintl.com, St. Louis) is a leading provider of test and measurement equipment for the worldwide technical services marketplace. It is a one-stop-shop, offering sales of test equipment and tools, plus calibration and repair services for most types of test equipment. Over the last five years, BC Group has sold several hundred Meriam (www.meriam.com, Cleveland) Smart Manometer calibrators to a wide variety of instrumentation and control customers in a variety of industries including refining, chemicals, manufacturing, pharmaceuticals, food, and medical.
According to Mike Clotfelter, BC Group vice president, Business Development, what makes the Smart Manometer calibrator desirable is the display that provides engineering units in mm Hg, mBar, and psialong with eight other engineering units. The accuracy specification is 0.05% full scale, approximately 72 psi on the Model 350DN2000 (Figure 2).
Documenting Acquired Data
The Industrial Company (TIC, www.tic-inc.com), through nine regional operations, provides industrial construction services to a diverse client base across the U.S. Headquartered in Steamboat Springs, Colo., the company typically uses its own engineering and construction people for the commissioning and startup of control system instrumentation.
According to Jim Mitchem, technology manager, checking out the hundreds of newly-arrived instruments and calibrating them prior to installation is largely a manual job, and recording these activities is often a problem. If the documents become illegible or lost, or the data itself is not secure, the calibration has to be redone, resulting in lost time and significant cost overruns. In addition, extra personnel are often needed to collect, review, edit and organize turnover documentation to determine that the calibration has been done correctly, and that all documentation is complete and accurate before presentation to the owner. The extra work can lead to missed project milestones and delayed completion dates.
At the Front Range power project (Fountain, Colo.) more than 1,200 field devices in a 480-MW power station had to be calibrated and documented prior to turning the plant over to the owner. Engineers at TIC had been evaluating calibration management systems for years, looking for an effective way of documenting the data obtained through the use of field calibrators. Although not looking for a predictive maintenance system, Mitchem noted that Emerson Process Managements (www.assetweb.com, Asset Optimization Division, Eden Prairie, Minn.) AMS Suite: Intelligent Device Manager (Figure 3) filled the bill because it provides device data and calibration parameters for all commonly used field instruments.
Emerson Process Management's Calibration Assistant snap-on application works with AMS Device Manager and common hand-held calibrators such as Fluke's Model 744.
Save Time, Effort, Dollars
Handheld field calibrators make it easy for technicians to visit instrumentation sites without the need to carry heavy equipment. Whether theyre used to calibrate instruments that measure temperature, pressure, or other process variables, these portable devices save time and money. When engineers couple calibrators with the right software, they find that keeping track of a large number of field instruments is much easier, eliminating all sorts of manual recording of information.
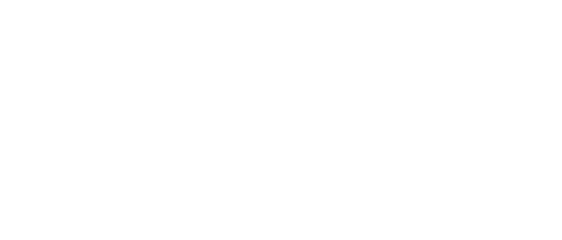
Leaders relevant to this article: