Back when Micro Motion debuted the first Coriolis meter some 45 years ago, the chemical industry was really the first to recognize the inherent advantages of direct mass flow measurement. At first, it was all about the ability to precisely control the molecular ratios of reagents, which after all is what chemical reactions are all about. But over the intervening years, Coriolis technologyāalong with a range of complementary Emerson instrumentation technologiesāhave proven their worth along with many other dimensions as well.
To further explore the transformative aspects of Coriolis technology and associated instrumentation for chemical industry operations, Control caught up with Michael Machuca, director of chemical industry marketing, Emerson.
Q: What do you see as the key challenges demanding the attention of the chemical industry?
Marketing Director, Chemical Measurement Solutions, Emerson
A: Traditionally, three things have been of foremost concern for chemical makers. First, safety remains the highest level of focus. The second focus area is maintaining consistent levels of product quality, which has become especially challenging when you consider the increasingly diverse formulations demanded in the specialty chemicals space. The third has to do with supply chainsāthe ability to meet customer demands by delivering the right product at the right time.
Two additional concerns that have moved to the forefront more recently are increased sustainabilityāwhich it seems every customer and government agency is clamoring forāand dealing with the recent effects of inflation. Increasing material and energy costs are having a significant impact on the operating margins of chemical manufacturers.
Q: In the past several years, digital transformation has emerged as a key initiative for manufacturers of all stripes. From an instrumentation perspective, how is Emerson helping to advance digital transformation in the chemical industry?
A: In this context, digital transformation is all about using the ancillary data that instruments generate to offer advanced diagnostics about instrument performance as well as process conditions. Smart Meter Verification, which Emerson debuted back in 2010, was ahead of the broader digital transformation movement and was a real breakthrough. By ensuring that a Coriolis meterās unique vibration signature had remained unchanged, it provided an extremely high assurance that the meter continued to operate as it did when installed or last calibrated. This allows users unparalleled confidence in our Micro Motion Coriolis meters and obviates the need to pull them from service for calibration as often as other flowmeter technologies.
Q: Coriolis seems to be expanding its footprint more broadly across the application landscape. What's changed?
A: Users are moving to Coriolis meters over other flow metering devices for their critical attributes, including direct mass measurement, multivariable output and no moving parts. Micro Motion 4200 two-wire transmitters have made the shift to Coriolis technology easier with existing 4-20 mA infrastructure. Meanwhile, we expanded the range of meter sizes available, and adapted them to higher pressures and temperatures.
Q: Batch applications are a particularly good fit for Coriolis meters relative to other flow measurement technologies. Can you explain why this is so?
A: Batching brings a different set of complexities than continuous processes, and when you look at specialty chemicals that are produced primarily in batches, Coriolis meters have proven to significantly reduce batch cycle time, increase batch predictability and even reduce waste and energy use. Many specialty chemical makers use multiple recipes and multiple feedlines that converge on a single flowmeter to be dispensed into a batch reactor. Traditionally, they used volumetric measurements and no density check to track product changeovers, resulting in inconsistencies from one batch to the next, and even the wrong product being erroneously batched in, resulting in loss of the entire batch. Weāve seen users, who changed over to Coriolis, use density to verify that the correct ingredient is added. Between reduced scrap, reduced cycle times and savings in energy, weāve seen the switch to Coriolis meters pay for itself in as little as two months of operation.
Q: Speaking of batch applications, Emerson has broadened its portfolio of related instrumentation to include insertion meters for density and viscosity measurement as well as Coriolis meters. Can you give some examples of how these instruments are being used to precisely define, for example, reaction endpoints more precisely than other methods?
A: Both density and viscosity are qualitative measurements and can confirm that a desired degree of reaction or endpoint has been reached. For example, we worked with an acrylic manufacturer that had a 20-second window in which to stop a polymerization reactionāand if they failed to quench the batch in time, it was wasted. Adding a simple fork viscometer to the reaction vessel increased visibility of reaction completion, and dramatically reduced wasted batches.
Q: It seems that sustainability, specifically in the context of reducing greenhouse gas emissions, has displaced predictive diagnostics as the ākiller appā for industryās digital transformation initiatives. Emersonās instrumentation technologies certainly play a role in providing greater visibility and accountability when it comes to greenhouse gas emissions, but theyāre also being used in more active roles to advance sustainability. How are Emerson instrumentation technologies making a difference, and how do they fit into Emersonās larger sustainability commitments?
A: Emerson has a three-pronged focus on sustainability, which includes āgreening ofā our own operations, āgreening byā which is what we help do for our customersā operations, and āgreening withā in which as we invest in university and other programs to innovate and advance new technologies in the sustainability arena.
One key area weāre working on with partners is carbon capture using amine-based absorption processes. Density, it turns out, is a critical control parameter that correlates directly to the concentration of absorbed carbon dioxide. The custody transfer of high-pressure carbon dioxide and hydrogen is also an ideal application for Coriolis. The production of lithium batteries used for electrical energy storage involves very corrosive processes, where flow measurement and pH analysis are needed. Plastics recycling, too, is pushing toward catalyzed pyrolysis to convert plastic wastes back into reusable monomers or polymers, and our instrumentation technologies are helping to make these processes a practical reality.
These are just a few of the broad range of customers and organizations across the chemical industry that Emerson is engaging with to better understand how they can improve and optimize their processes, all with an eye on more sustainable operations. Across our company, Emerson is highly relevant to a more sustainable future with expertise, technologies, solutions and a global perspective that can help the world find a path forward.
Latest from Flow
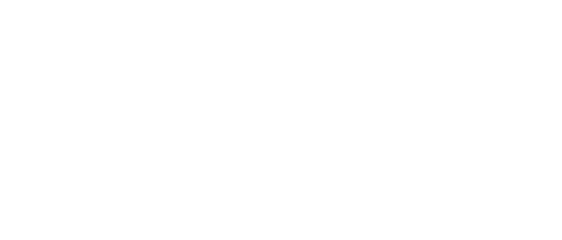
Leaders relevant to this article: