Thermal imaging is ideal for examining electrical equipment, and this plant has plenty of itapproximately 115,000 kilowatts coming in. Until recently, the facility used a secondary contractor to conduct annual thermal imaging surveys of its key electrical equipment. This was a problem, however, because this thermographer was located 6.5 hours away, which was too long to wait for problem assessments, especially in downtime situations. Subsequently, new thermal imagers became available that were more affordable and easier to use than traditional models, but still powerful enough for facility maintenance. So, Alltech bought a Fluke Ti30 thermal imager, sent operations manager (and co-author) Barry Ungles to training, and began inspecting Jayhawks plant equipment.
An engineer gathers thermal images of electrical components at the Jayhawk plant.
Each year, Alltech spends about three days scanning the Jayhawk plant for electrical problems. The two power control rooms are divided into sections, or buckets, which contain switchgear and breaker sources for power supply and distribution. The electricians monitor everything in the buckets, checking all the operating stations, and making thermal images of all the electrical connections, from relays to transformers. They also use the imager to look for loose connections, which is where major problems, such as meltdowns, often occur.Because Ti30 can measure components to 0.25 degrees, we can find wire lugs that are loose, but only overheating slightly. This means that we can detect potential problems long before they become serious problems. In some cases, we can tighten lugs on the spot, if its safe to do it. For more serious problems or for equipment carrying very high voltages, we take a thermal image and a digital photo of the unit, and send a report to the supervising plant technician. Besides monitoring electrical components, we also use thermal imaging to check the plants sludge catcher, which is a big vessel that collects waste from the natural gas. At one point, plant personnel werent sure their level indicators were working correctly, which meant they werent sure how much sludge was in the vessel. We made thermal images of this unit at the end of a hot day, when the vessel had begun to cool. Those images revealed the line between the heated sludge and the unrefined natural gas above it in the vessel, which had cooled faster. Thermography proved to be a failsafe backup to the level indicators. Using manual verification to determine the sludge depth would have required a major plant shutdown and an extremely dangerous vessel entry procedure. With thermal imaging, we were able to determine this depth for a fraction of the cost of conventional methods.FIGURE 2: PRETTY COLORS
IN ANOTHER case, we wanted to determine which valve in a faulty system needed to be replaced. Conventional troubleshooting was ineffective due to operating constraints, but replacing all of the valves would have cost $15,000. So, we used the thermal imager to locate temperature deviations in the system, found the faulty unit, and replaced just one valve.
The imager also saved a $100,000 project at the plant, which had been at risk due to faulty pump seals after the vendors engineers couldnt solve the problem. Thermal imaging revealed that the seal failure stemmed from overheating caused by insufficient flow and coolingnot from a faulty unit. If the pump seal had simply been replaced and the real problem left uncorrected, the failure would have led to a spill.
Other Applications Find You
In the gas fields, Alltechs electricians use the Ti30 Imager to monitor mechanical devices. Thermal images can detect alignment problems in rotating equipment, for example, between a motor and a compressor. With a thermal image, they can quickly discover when a bearing is heating up due to misalignment.
They also use thermography to monitor 24 V control circuits. On these low-voltage installations, the imager lets users pinpoint loose connections as potential problems, tighten them, and prevent future failures. Using its Ti30, Alltech found loose 24 V connections that werent problems yet because of their wires rating. However, they might have caused shutdowns later if those connections had kept vibrating until their screws and wires came out of their sockets.
Thermography, PdM and Teamwork
Because thermal imagers capture otherwise invisible images of infrared (IR) radiation, and show temperature ranges as color or tone variations, observers can easily pick out hot or cold spots that might signal electrical or mechanical changes and/or process flow problems. This is a natural ally for any predictive maintenance (PdM) effort to regularly collect measurements, track indicators to predict needed repairs, and reduce maintenance costs and production losses.
In addition, with basic imaging training and good plant-floor communications, many different facility teams can benefit from thermal imaging. For example, our plant uses extremely cold processes to remove unwanted gases from the natural gas. In one case, a nitrogen pump had a persistently leaky seal that had to be changed out regularly. The electricians took a thermal image of the pump, and an engineer immediately saw there was a restriction preventing the seal from receiving enough cooling airflow, which was causing the seal to overheat and melt. Another problem solved.
"Using thermal imaging, we determined that insufficient airflow and cooling were causing a particular pump seal to fail. Learning this saved a $100,000 project from experiencing ongoing seal failures." |
About the Authors |
Latest from Flow
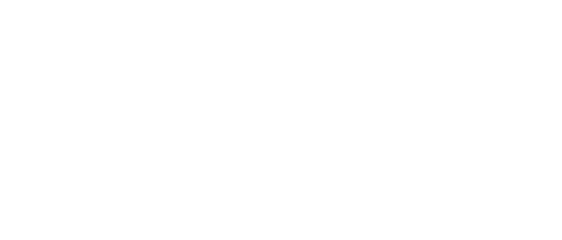
Leaders relevant to this article: