Because accurately measuring product level in a tank, silo or reactor can be quite demanding, the process instrumentation professional has at his or her disposal an impressive array of technologies based on just about every conceivable difference in measurable physical properties between two media. But nowadays, identifying an appropriate technology that meets accuracy requirements for continuous level—or detecting the presence of material at a particular point—is really only the first step in choosing the best instrument for a given application. Indeed, today’s smart instruments boast an array of functions and features beyond the nominal process variable (PV) that can make life better in myriad ways—or not, if you don’t take them into account.
Endress+Hauser is a global leader in the realm of process instrumentation, and Control recently caught up with Scott Peterson, national product manager, level, for Endress+Hauser’s U.S. operations, to discuss how today’s intelligent level instruments can bring a tremendous amount of value to process operations above and beyond a stable and accurate PV measurement.
Q: Let’s start out by putting the current state of level instrumentation technology in context. I'd argue that choosing a suitable technology that meets accuracy requirements for a given application is a relatively easy step, and that further, if that’s all you’re interested in, you can have your pick of a number of quality instrument suppliers at a range of price points. Why not just take the cheapest one?
National Product Manager, Level, Endress+Hauser USA, [email protected]
A: Certainly, if the measurement is a simple and straightforward application, cost may very well be one of the considerations, and many different level technologies will yield satisfactory results. But oftentimes, other factors beyond measurement accuracy come into play.
Radar level gauges, for example, are benefitting from improved performance and functionality, even as their price points have been coming down. Some of today’s radar instruments offer sophisticated digital signal processing to filter out false echoes, for example, and advanced algorithms for PV tracking increase the probability of success in even the most demanding applications. Plus, intelligent diagnostics with clear messaging can provide timely alerts to problems with the device, or abnormal process conditions such as foam or build-up on the antenna.
Q: It seems that most of the differentiation when it comes to today’s smart instruments fall into three major buckets: features and functionality that contribute to improved safety, simpler work processes, and/or greater productivity. Let’s talk first about improved safety. Short of a redundant setup or overfill protection switch, what capabilities aboard a smart level transmitter itself contribute to improved safety?
A: For a level transmitter used as part of a layer of safety protection, there's unlikely to be a large difference between the statistical risk of an undiagnosed failure between two similar devices from reputable manufacturers. So, the key aspect to consider is how can this instrument reduce my overall risk of systemic failure? That's where differences arise. Wizards that guide operators through the periodic proof tests required of safety instruments are one example. With some point-level switches, proof testing can be as easy as a push of a button.
Think of the dozens, if not hundreds, of instruments in a process area that require proof testing. Each is going to have a slightly different proof test procedure, and no technician is going to have them all memorized. So, many operators refer to a written manual—and hope they don’t get interrupted in the process. But a wizard that leads you through the process helps ensure that proof tests are done correctly 100% of the time. You're not actually making any changes to the instrument, but it's asking you questions. Did you check this? Yes. What was the response? The instrument leads you through all the steps exactly as identified in the functional safety manual. And when you’re done, you can automatically generate a PDF documenting the test.
Q: Simpler work processes seems to be a phrase that can be applied throughout a level transmitter’s lifecycle, from installation and commissioning to operations, calibration and maintenance. What level instrument features and functionality can make instrumentation professionals’ life easier at each stage?
A: Practices for the installation and commissioning of devices have been complicated by the ever-increasing number of smart devices—each with slightly different interfaces and menu structures—and the ongoing attrition of experienced technicians. The recent arrival of commissioning wizards helps simplify that setup process, eliminating uncertainty along the way.
Bluetooth communications are simplifying that process even further. Before wireless, the service tech had to locate a laptop or handheld communicator, ensure the correct DTMs were loaded into the software, then connect physically at the device or at the marshalling panel. With Bluetooth, a lot of that goes away. You really only need a smartphone and appropriate companion app. Also, the numeric or hieroglyphic error codes of yesteryear are being replaced with meaningful language a technician can directly understand, rather than have to look up.
Those wizards we discussed earlier in the context of proof testing are also available to guide calibration and other maintenance processes.
Q: Improved productivity can have two contexts, one that applies to productivity of personnel, and a second that applies to the production processes at hand, such as avoiding unscheduled downtime. How can one’s choice of level transmitter contribute to improvements in both these spheres?
A: Two key aspects that come to mind are onboard diagnostics—for the device and for the process itself—that are increasingly prescriptive in nature, plus instrument verification processes.
In the past, the first thing your control room operator did when it got an alarm warning from an instrument was to send a technician out to first find the instrument, who then radioed back to the control room for help interpreting the diagnostic code on its display. However, with today’s advanced diagnostics, you’re not getting just an error code but also an understandable warning or alarm that also informs you just how urgent the problem is.
If you’re in the field, you can access this information via Bluetooth or via the local display with a couple pushes of a button. You also have the information you need to decide whether to deal with it immediately, or if it’s something you can put into the regular maintenance schedule for a few days from now. That’s a ton of productivity from both process and personnel perspectives.
Instrument verification is a qualitative assessment that the instrument is still operating as intended. Importantly, verification isn't the same as calibration, which is a quantitative assessment, but it does check that the gauge’s electronics are operating within the specifications established when the transmitter was first installed. The nice part of verification is that it can provide assurance well into the 90th percentile that the gauge is operating properly. It’s an in situ test that doesn’t require that you pull the gauge out of the tank, break the seal on the a vessel or pipe—or even interrupt the signal back to the control room.
The peace of mind that verification provides can boost personnel and process productivity along several dimensions. It’s just one way that today’s smart instruments can bring greater value to the process as a whole.
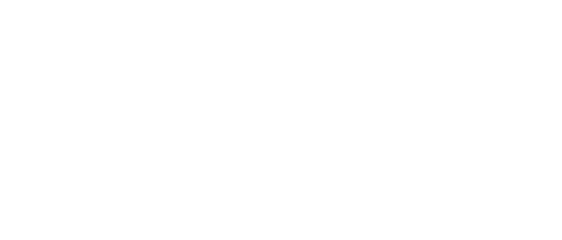
Leaders relevant to this article: