TheyĀre often a fact of life to be borne like the trials of Job, but not always. Control interviewed three different end users of SiemensĀ new Sitrans LR-series radar-level transmitters. Facility applications ranged from recycling to steel to plastics, which all reported little trouble with the Siemens units.
Safety Kleen HoldcoĀs plant in Denton, Texas, processes clientsĀ discarded chemicals into fuel for cement kilns. These processes require precise level measurement in difficult environments. Bill Bakus, Safety KleenĀs plant engineer, reports his facility has been using seven Sitrans LR200 radar level transmitters for about two years, with only one unexplained failure. He says the units are easy to install and calibrate. Getting the power in conduit to the outside tanks was the biggest part of the installation, with physical mounting of the Sitrans units taking just minutes.
Likewise, almost any electronic application in a steel mill is challenging, and this is the case with 28 silos at the Nucor mill in Decatur, Ala. They contain manufactured or smelted materials for alloying end products. One example, with a special challenge on the dust side, is carbonĀat 8µ-10 µ (by comparison cigarette smoke is ~40 µ)Āwhere SiemensĀ units can ĀseeĀ the material interface.
Andrew Smith, Nucor electrical engineer, reports that since Nucor purchased the plant. it has tripled output, and that plant automation is a key aid. SiemensĀ LR400s reduced maintenance and have been failure-free. By contrast, their predecessors experienced:
- Dust that destroyed bearings and penetrated enclosures,Ā yielding only six-month lives for the four former units;
- Variable material densities, hardnesses and angles of repose that presented difficulties for other units;
- Multiple false reflections and minerals in the silos thatĀ abraded wire ropes used for suspension.
Smith says LR400 is easy to aim, can be kept out of the fill stream and accounts for the measured materialsĀ angle of repose. With plant device manager (PDM) software, a profile can be set up for each siloĀs material. He adds that, while the units are connected to the plantĀs HART network, maintenance and supervisory personnel can easily monitor the 34 units on their rounds, using handheld infrared monitors.
Smith said Nucor did have some problems with Sitrans. Dust got into the waveguide, but this was solved with pipe tape. Also, with temperatures up to 160 °F-200 °F, there are some freeze-ups or high or low readings.
Preventive maintenance (PM) is conducted every 90 days. Since only four bolts hold down the units, this only takes 15 minutes per unit. PM on prior units could be done only on Ādown daysĀ and needed man-lifts to access the silosĀ sides.
Nucor is putting in another tank farm with 14 more silos for fluxes that will be equipped with Sitrans LR460s. SmithĀs only concern isĀ controlling dust build-up. Dust cap integrity is essential. If dust cakes inside the Āhorn,Ā transmitted and returns signals are distorted.
Smith says he Ālikes Sitrans unitsĀ reliability, maintainability and consistency of measurement.Ā He also was impressed with SiemensĀ rapid tech support that can troubleshoot issues via phone or Internet connection.
Likewise, DuPontĀs SRW plastics and synthetic resins plant in Orange, Texas, is in a tough, 300 °F environment.Ā Veryl Williams, electrical and instrument engineer, says levels in both the feed (prill and pellet wax) and melt tanks are important. Prior level measurement was capacitance-based with a float and dip-tube arrangement that had to be cleaned every six or seven monthsĀwhen the process was down.
So when Williams was looking for a non-intrusive method, LR 250Ās beta version fit the bill. He noted that with the mounting flange 6 in. off the tank wall, SiemensĀ software factored out the nuisance reflections.
The two LR250s have been in service trouble-free at DuPont for two years now. In the future, Williams says these units will be integrated into the plantĀs automation monitoring system.
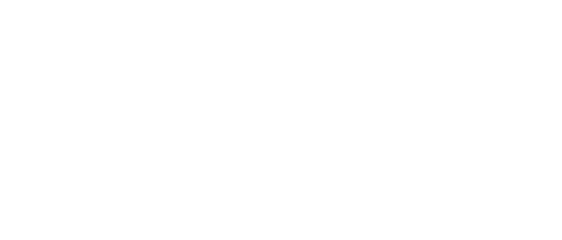
Leaders relevant to this article: