By Paul Miller
“Reliable measurements enable our plant to operate within limits, improving the safety and reliability of the plant, while maximizing profit,” says Greg Breaux, instrumentation specialist at the Motiva Enterprises Norco Refinery, located just outside New Orleans.
“DP [differential pressure] technology is perhaps the most simple and reliable technology for measuring level as well as flow. It is usually the right technology in applications where the specific gravity of the process does not change more than the desired accuracy of the measurement,” said Breaux. “DP technology is simple to understand, and simple to design and install. The basic technology has been around so long that everyone understands it, even when you add the new advancements, such as remote seal diaphragms, Foundation Fieldbus, etc.”
“Simple, reliable,” and “well-understood” are three expressions commonly used to describe pressure-based level measurement approaches. This reflects the fact that, while radar, ultrasonics and other new level measurement technologies are rapidly gaining acceptance, the majority of continuous level measurements in today’s process plants continue to be made using pressure or differential pressure transmitters.
Still Popular after All These Years
[sidebar id="1"]“Of the nearly two million DP transmitters sold every year, approximately 25% are used for level measurement applications. This represents a sizable number of transmitters,” commented Wil Chin, research director at ARC Advisory Group, Dedham, Mass. According to ARC estimates, two-thirds of the overall automation market is for existing plants, where replacement-in-kind makes a lot more economic sense than introducing new technology that would require different installation practices and additional training. DP transmitters do a very decent job for most level measurement applications and offer some benefits not always available with other approaches. For example, many DP transmitters are mounted with isolation manifolds that make it relatively quick and easy to replace the entire instrument, if necessary, without having to shut down the process.”
According to Jesse Yoder at Flow Research, Wakefield, Mass., “Installed base is the single biggest factor that has sustained growth in the pressure transmitter market. Many companies have invested very heavily in pressure transmitter technology and are not likely to abandon this investment. Changing technologies often requires changing suppliers and has additional start-up and educational costs. Many end users will choose to stay with their pressure transmitters unless they have a particular problem with them or are required to change technologies by regulations or because they need to move to a higher performance level. Even in this case, technology improvements by pressure transmitter suppliers may persuade end users to stick with pressure transmitter technology.”
“Due to the infinite flexibility of process connections, operating limits and system configurations, DP level can be used in almost any liquid level application,” commented Jeff Graupmann, DP level marketing manager at Emerson Process Management. “Pressure has been used to measure level for more than forty years, so it is well-established and trusted for continuous measurements ranging from simple monitoring to advanced control applications. Differential pressure is a simple reliable technology, which can be used for level, pressure and flow measurements, so it is well-understood by everyone in a plant. Recent technological advancements include new practices, such as direct mounting and advanced diagnostics. Digital sensors can also be linked together to create multivariable systems.”
The basic principle behind hydrostatic pressure-based liquid level measurements is fairly simple. Pressure and DP transmitters measure level based on the principle that pressure is proportional to the level of liquid multiplied by the specific gravity (the ratio of the fluid’s density to the density of water). Another way of looking at it is that level equals the hydrostatic head (pressure) measurement divided by the density of the liquid.
In open (vented) tanks or vessels, the DP transmitter is mounted at the bottom of the vessel. The high side or the sensor measures the hydrostatic pressure exerted by the fluid in the vessel. The low (reference) side senses atmospheric pressure.
In sealed (pressurized) tanks or vessels, a diaphragm mounted on the vessel at a point above the liquid is connected to the low side of the sensor to provide a reference leg. With conventional analog transmitters, the pressure difference between the high and low sides is converted into a pressure-proportionate output signal. With intelligent transmitters, the pressure difference is converted directly into engineering units.
“The original installation method for using a DP transmitter for level was to use impulse tubing to connect the high and low pressure sides of the DP sensor to the bottom and top of the vessel,” Graupmann explained. “The impulse tubing used for the low-side reference is called a ‘dry leg’ system when used on dry, non-condensing vapor space applications. The impulse reference leg is filled when the vapor space might condense and is called a ‘wet leg’ system. Capillary/seal systems were introduced to eliminate the measurement uncertainty and maintenance of impulse tubing installations.”
While capillary/seal systems have helped improve pressure-based level performance, they can also add a bit of complexity. “One issue we have had to deal with regarding remote seal DPs is that we have so many with different tap dimensions,” commented Motiva’s Breaux. “This requires us to stock many spare devices, with different capillary lengths. Sometimes we must replace a device with a new device from stock with excessive capillary length, because it is the shortest one that will fit. Stocking of spare parts is an issue for a long-term, run-and-maintain operation.”
Breaux adds, “We have created a short checkout procedure we perform during installation of remote seal DPs. We first check the accuracy of the device on the bench, then as installed on the vessel open to atmosphere before lining it up to the process. This resulted from our early experience, where we found a few devices reading incorrectly after they were installed. We removed them and found damaged diaphragms, probably from shipping or handling.”
Since density variations, which are commonly caused by temperature fluctuations, can result in pressure-based level measurement errors (especially in closed tanks), additional pressure and/or temperature measurements are also often required to be able to continuously calculate the density of the liquid in both the vessel and reference leg(s). These additional measurements typically are performed using separate transmitters with the density and level calculations performed in the control system.
With the wide variety of different process connections (direct-mount, flanged, remote seal, etc.), process-wetted materials (carbon steel, 316L stainless, Hastelloy C, titanium, Monel, etc.), and fill fluids available for DP transmitters, they can be adapted for the majority of liquid level measurement applications encountered in process plants, including high-temperature, high-pressure, corrosive and sanitary level measurements.
Some Recent Developments
Emerson Process Management, Endress+Hauser, Invensys Process Systems and other leading automation vendors quietly have been enhancing their pressure instrumentation families in recent years to be able to provide process industry end users with improved pressure, flow and level measurements in increasingly challenging applications. These are helping to maintain the viability of well-proven pressure-based level measurements against newer and “sexier” technologies, especially in existing plants where pressure-based level measurements are already being used.
Ceramic pressure sensors
For example, new ceramic pressure sensors from Endress+Hauser are made from 99.9% pure aluminum oxide to provide extended chemical compatibility. The physical durability of the ceramic pressure sensor makes it appropriate for use for abrasive fluids or applications requiring frequent buildup on the diaphragm. According to Endress+Hauser the dry (no fill fluid) ceramic sensors can also be used to measure deep vacuums at elevated temperatures without damage to the diaphragm.
Asymmetrical diaphragm seals
In the past, the standard practice for measuring level with DP transmitter remote seal was to specify symmetrical systems with the same diaphragm seals and identical capillary lengths for both the high and low pressure process connections. In an effort to reduce the temperature-induced errors inherent to diaphragm seal systems, Emerson has developed an asymmetrical approach, with each system specially tuned for the individual application. According to Emerson’s Graupmann, these “tuned system assemblies” combine direct-mounting of the high-side seal to the DP transmitter with the optimal seal system to improve performance, reduce response time and reduce installed costs as compared to conventional balanced-seal systems with equal seals and capillary lengths. In effect, the asymmetry of these tuned systems compensates for the temperature-induced errors.
According to Emerson product literature, “Tuned-Systems are an asymmetric configuration of a differential-pressure diaphragm seal system. The simplest form of a tuned system directly mounts the diaphragm seal to the high-pressure process connection. Eliminating the excess high-pressure capillary immediately improves response time and performance, while reducing installed costs. Total system error is compensated by leveraging diaphragm-induced temperature errors against head-effect temperature errors.”
Due to the number of variables involved―including the physical characteristics of the fill fluid, capillary length and diameter, and the mechanical design of the diaphragm seal system itself―Emerson offers a software tool that simplifies the design of a fully compensated, or “tuned” DP seal system. This toolkit provides the capability to calculate numerous potential compensated seal systems for any given application condition quickly and easily.
“Electronic” remote seals
For specialized applications or in situations where the installation or maintenance of hydraulic systems may be an issue, both Emerson and Endress+Hauser are promoting a pressure-based level measurement approach that replaces a DP transmitter and its associated wet legs, dry legs or long capillaries with separate pressure transmitters that are made into a multivariable system using fieldbus communications. Emerson calls this approach, “electronic remote seals,” since it replaces the conventional hydraulic systems with digital communications.
According to Emerson’s Graupmann, “Electronic remote seals can improve measurement performance by eliminating dry/wet legs or capillaries. Dry/wet leg installations can introduce measurement uncertainty if there is any variation in these references caused by condensation in a dry leg or evaporation in a wet leg. Both lead to a shift in the DP zero reference. Capillary systems have head temperature effects caused by the change in density of the column of fill fluid in the capillary. This column is eliminated in an electronic remote seal system where the sensors are direct-mounted to the vessel fittings. Capillary systems also have seal temperature effects related to the fill-fluid volume change. These temperature effects are minimized by direct-mount seal systems.”
Graupman continues, “Electronic remote seals can also help reduce maintenance costs. Keeping the wet/dry leg reference stable is key to measurement performance. This typically requires extensive maintenance. Periodic draining or filling of legs, insulation and heat tracing maintenance costs can all be minimized by eliminating the wet/dry leg installation practice.
“Installed cost is a little more difficult to compare as you need to compare the instrumentation cost of the different installation approaches. The electronic remote seal system has two pressure sensors, so it will more expensive than a DP transmitter with two capillaries most of the time. But to be fair, you also need to consider the other installation costs like heat tracing that might be required for a particular transmitter installation.”
The Ziemann Group is the world’s largest manufacturer and supplier of beer brewing plants. At the company’s pilot brewing plant in Ludwigsburg, Germany, liquid level in the closed vessels of the fermentation and storage tanks is monitored using two Siemens’ digital pressure transmitters equipped with stainless steel housings and sanitary flush mounted diaphragms. One pressure transmitter, mounted at the bottom of the vessel, measures the hydrostatic pressure plus the superposed overpressure. The second pressure transmitter, mounted toward the top of the vessel, determines the pressure above the liquid level. The liquid level then is calculated in the control system using both measured values.
However, in the pilot plant’s open brewing vessels, a single Siemens pressure transmitter is used to measure the hydrostatic pressure of the liquid column at the bottom of the vessel to determine the liquid level.
With a measuring range up to 150 °C, these Siemens pressure transmitters are well-suited to sterilization-in-place, without showing any drift effects.
Multivariable level transmitters
Multivariable transmitters offer yet another approach to obtaining highly accurate pressure-based level measurements in either open or closed vessels.
Bristol Babcock introduced the first multivariable in 1992. Since that time, Emerson (Rosemount), Honeywell, ABB, Invensys (Foxboro), and Yokogawa have entered the multivariable market. Multivariable transmitters measure more than one process variable, typically pressure, differential pressure and temperature and can use these measurements to calculate fluid flow, mass flow, density or level.
According to Flow Research’s Yoder, “Much of the growth in the pressure transmitter market is due to growth in the multivariable transmitter market. The market for multivariable DP transmitters for flow has more than doubled in recent years.”
Foxboro introduced the first dedicated multivariable level transmitter in 2004. This transmitter uses pressure, differential pressure and temperature measurements, plus on-board physical property tables, to compensate for density changes in the tank liquid and vapor and density changes in both vapor or liquid in external dry or wet legs. According to the company, this makes the transmitter ideally suited for critical applications, such as boiler drum level and for other high-performance applications where fluid densities are significantly affected by variations in pressure and temperature.
“For these types of applications, the conventional pressure-based level measurement approach was to install three separate transmitters―gauge pressure, differential pressure and temperature―and run these wires back to the control system where the level calculations were made,” said Pat Cupo, pressure and temperature product manager at Invensys Process Systems. “Now, a single Foxboro multivariable level transmitter can handle all three measurements, compensate for density changes and make the level measurement calculation right in the transmitter. We believe that these result in better level measurements, reduce installation and wiring costs, and reduce the bandwidth load on the control system. What’s more, some level applications, boiler-drum level, for example, are not all science and still require quite a bit of art to properly locate and configure the instruments. With multivariable transmitters, there’s only one instrument to deal with, rather than three. This helps to keep things a lot simpler.”
Cupo continues, “That said, many end users tend to treat multivariable transmitters as ordinary DP transmitters, and that’s clearly not the case. For example, if you relocate the transmitter, it’s important to update the transmitter’s database so that it can make the appropriate compensations. Safety is another consideration, particularly with high-pressure, high-temperature boiler-drum level measurements where the wet reference leg can go dry due to steam boil-off. This would result in incorrect drum-level measurements that can cause bad things to happen. We’re working to eliminate this type of problem through improved documentation and configuration procedures. This is critical, since we’re finding that as ‘old school’ maintenance technicians retire, their knowledge and experience often retires with them. This is a huge issue, particularly since the new generation of maintenance technicians are often more familiar with information technology than with instrumentation technology.”
However, despite the obvious advantages, multivariable transmitters have not yet achieved the market acceptance for level measurement applications as they have for flow measurement applications.
According to Emerson’s Graupmann, “Multivariable transmitters continue to be associated mainly with flow measurements, and to date, have gained only limited acceptance for level measurements. Multivariable transmitters are used when pressure and temperature level compensation is required. Multivariable transmitters can save on installation costs by combining three transmitters into one. Acceptance levels depend on a user’s willingness to adopt new installation practices based on resulting operating or maintenance improvements.”
The continuous investments being made in DP level measurement technology by automation vendors, combined with the widespread acceptance across the user community, mean that pressure-based level measurements will remain a viable approach well into the future.
Paul Miller is a Control contributing editor.
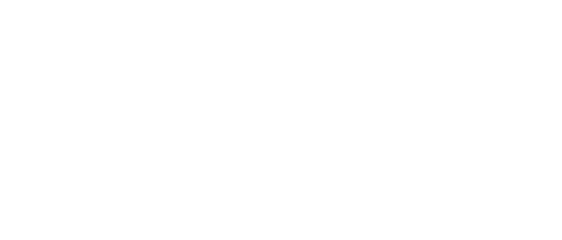
Leaders relevant to this article: