ALMOST HALF OF THE controllers in a typical process plant are flow controllers, and the next most c ommon regulate liquid level, many of which set flow in cascade. Level loops differ from others in their economic objectives, in that there may be no economic penalty associated with a particular deviation from set point–yet a loss of level control can shut down an entire plant. They also differ in that their task is to regulate a process that is fundamentally non-self-regulating. This characteristic leads to limit-cycling of a PI (proportional + integral) controller in the presence of any deadband in the control valv e, avoided by using either a valve positioner or a cascade flow loop. This combination of properties results in the need for different rules for tuning level controllers than are applied to flow, temperature, pressure and composition controllers.
There are different categories of level loops based on the vessel being regulated, and different tuning rules apply to each. Four categories are suggested here:
-
Surge tanks feeding critical processes
-
Material-balance regulators between process stages
-
Levels affected by shrink-swell and inverse response, such as boiler drums
-
Levels with resonance (manometer effect)
Surge Tanks Serve to Deliver
A surge tank accumulates feedstock from one or more sources–some may be batch–and serves to deliver a smooth average feed rate to a critical downstream process such as a reactor, evaporator, distillation column, or recovery boiler. To minimize disturbances to the downstream process, its feed rate should be constant, but must represent the average value of the total flow entering the surge tank. Averaging takes place over the closed-loop time constant of the surge tank–typically 20 minutes to several hours–and this application is called “averaging level control.” The tank accumulates volume based on the integral of the difference between total inflow and manipulated outflow rates. Its integrating time constant is the time required to empty the tank from 100 to 0% level with zero inflow and 100% outflow (or by any other percentage level with the same percentage difference between inflow and outflow rates).
Simply Proportional Only
The simplest method of averaging level control is proportional-only. Consider the case of 100% proportional control, where the controller at 100% level sets outflow at 100%, and at zero level sets outflow at zero. This produces a closed-loop time constant equal to the integrating time of the tank. The outflow at any point in time consequently represents the exponentially weighted average value of the inflow, averaged over the integrating time constant of the tank. The closed-loop time constant of the tank is that portion of the tank volume covered by the proportional band P of the controller.
It could only exceed the time constant by setting P beyond 100 %, but then outflow could not be manipulated over its full range, and the controller could not prevent the tank from overflowing or emptying. In most cases, operators choose a safety margin such as 10% at both ends of the tank, which requires a proportional band of 80%.
Proportional Controllers
A proportional control algorithm manipulates outflow m in relation to the deviation of controlled level c from set point r where b is an adjustable output bias also known as “manual reset.” Ideally, m should be the set point of a linear flow controller.
If r = 50 and b = 50, then the proportional band will be distributed uniformly across the level measurement. One drawback of proportional control is that the level will almost never be at set point, leading operators to suspect that the controller is not working properly. One way of avoiding this misconception is to set r at the desired low limit of level, and b at zero, so that flow is zero when the level falls to that low limit. Full outflow is then reached when the level rises.
Some digital controllers are unable to execute pure proportional control, in that bias b cannot be fixed, but floats, changing every time the controller is transferred between automatic and manual. Such a controller cannot be used in this application. But a proportional controller can be made from a digital scaler or calculation block, performing the function: where cl and ch are set low and high limits respectively.
Proportional-lag Control
The maximum rate-of-change of outflow following a step change to inflow fi occurs immediately following the step. The initial steady state is at 50% flow and level. Because the proportional band of the controller is 80%, the level change is 80% of the steady-state flow change.
Its value can be reduced by inserting a first-order lag at either the input or output of the controller. The upper set of curves in Figure 1 shows the effect of a lag whose time constant f = 0.4. This is about the highest value recommended, in that it produces a second-order closed loop with a damping factor of 0.707–note the slight overshoot in flow and in level. At the same time, it reduces the maximum rate-of-change of outflow to a factor of 0.65 of what is calculated. It also effectively filters noise and other high-frequency transients.
Nonlinear Proportional Control
To further reduce the rate-of-change of outflow, some have used a nonlinear characterizer on the controller deviation, such as an error-squared function or a three-zone characterizer, both of which provide a reduced gain to small deviations. (Note: the “error-squared” function is really the product of the deviation and its absolute value.) However, the low gain around setpoint necessitates a substantially higher gain elsewhere, to satisfy the same high and low limits of level.
With a linear proportional controller, the steady-state level is linear with steady-state flow. With one of these nonlinear controllers, the steady-state level will remain in the middle of the tank over only a narrow range of flow, for the most part settling above or below the low-gain range, where the controller gain is higher than that of a linear controller at the same flow. Therefore, their use is counter-productive, and they have been removed from service in most cases where they have been tried.
Only if the flow has a very narrow probability distribution about a known operating point, with the low-gain zone of the controller centered around it, is the nonlinear proportional controller useful. However, these characterizers can be of some help to a PI level controller, as described later.
Material-Balance Regulators
The most common use of level controllers is to regulate the material balance between interconnected stages of a process. For example, a multi-effect evaporator has a level controller manipulating flow from one effect to the next, and from the last effect to the product tank. Most distillation columns have two level controllers–one at the base of the column or in its reboiler, manipulating bottom-product flow, and one at the reflux drum, manipulating distillate or reflux flow. They are scattered through any process plant, essential to its operation, and must be in service before the plant can start.
Here again, there may be no economic penalty for deviation from setpoint, but overflow and emptying must be avoided. As in a surge tank, rapid changes in manipulated outflow are undesirable, but these vessels have shorter time constants–in the range of 20 seconds to 5 minutes. Proportional control may not be acceptable, and there may be an optimum setpoint, designed to keep reboiler tubes covered for example. The level measurement may also be very noisy due to agitation or boiling, and the noise should not be passed along to the manipulated flow.
Proportional-Integral Control
The maximum rate-of-change of manipulated flow is still governed by Equation (4), but the addition of integral action to the controller forms a second-order system, even in the absence of additional dynamics. Its damping factor varies with both controller settings.
Damping factors have been fixed at values of 0.5 and 1.0 by the integral settings of 0.5 and 2 respectively, the proportional band being 50 % for both cases. They represent reasonable limits: the value of 1.0 represents critical damping (no overshoot) and 0.5 has some overshoot. Lighter damping is not particularly desirable in a level loop.
The selection of proportional band needs to be made on the basis of maximum rate-of-change of flow, or of peak level deviation for a given load change. The effect of changing proportional band on the step load response where has been fixed at 0.5 by setting the integral time is a function of the proportional band.
Observe that the proportional setting determines the peak deviation for a given damping factor. However, the amount which the manipulated outflow overshoots the inflow step is independent of proportional band. The time of occurrence of the peak level deviation is determined entirely by the integral setting, and that of the peak change in outflow is exactly double that value. Peak deviation is ep and peak change in outflow is )mp.
Select a desired damping factor, then estimate the largest expected load step and the acceptable peak deviation resulting from it. Then calculate the proportional band required to satisfy this relationship.
Where f(.) is the coefficient in the third column of the table. As an example, consider a desired damping factor of 0.707, with a load step of 30 % resulting in a peak deviation of 20 %: P = 100(20/30)/0.66 = 100%. Then I = 2 (100/100) = 2.
Additional dynamics in the loop have little effect, up to a limit. For example, a loop with 0.707 can tolerate a dead time up to 0.2 I with no loss in damping and only a small increase in the maximum rate-of-change in outflow; the dead time must be as high as 0.5 I to approach the limit of stability. Inserting a first-order lag of 0.4 reduces the maximum rate-of-change of manipulated outflow by the same 0.65 factor as in proportional control, but causes the peak deviation and overshoot in manipulated flow to increase by half, as well as extending the settling time. Filtering up to this point does not destabilize, but its effects should be limited to noise reduction.
References
1. Wade, H.L., Basic and Advanced Regulatory Control: System Design and Application, 2nd ed., ISA, Research Triangle Park, NC, 2004, pp. 168-169.
2. Shinskey, F.G., “Taming the Shrink-Swell Dragon,” Control, March 2004, pp.35-40.
F.G. (Greg) Shinskey, process control consultant, has more than 34 years experience as a systems engineer. He is author of several textbooks on control systems design and is based in North Sandwich, N.H. Contact him atshinskey@msn.com.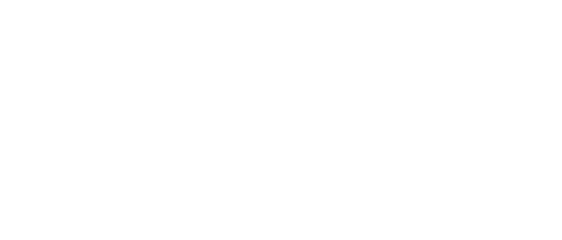
Leaders relevant to this article: