Q: We have weighing hoppers on three load cells (Figure 1). During charging, the vent valve is open and the pressure is atmospheric (zero). When filling is complete and the weight is registered, the vent valve is closed and we pressurize the hopper to 2 bars. As the pressure rises in the hopper, the weight measurement signal drops. Can you tell me why the scale reports a drop in weight during pressurization and returns to the pre-pressurization reading once the pressurization is over and the pressure has stabilized?
Ashish Garg / [email protected]
-----
[sidebar id =1]
A: For the benefit of readers who are not familiar with the steel industry, I will start with a brief description of the blast furnace process, because in order to properly control a process, we must always fully understand it.
Mr. Garg, yours is a bell-less top (BLT)-type blast furnace, and within that category, it is of the two-hopper variety. This design is a good one as it keeps the furnace closed, which prevents escape of exhaust gases, while charging the alternate layers of a mix of iron ore and lime from one hopper, followed by charging a layer of coke from the other. The "tilting rocker" above the two hoppers alternates filling the hoppers, while the inlet and outlet seal valves isolate it and the flexibility of the expansion bellows at the bottom allows the hoppers to be supported only by the load cells while being weighed. The operation is such that when one of the hoppers has been filled, it is pressurized until its pressure matches that in the furnace before its contents are charged into the furnace. While one hopper is being emptied into the furnace, the other is filled simultaneously, or it can be filled only when the other has been emptied.
The fact that in your case a pressure rise in the hopper causes a drop in its apparent weight indicates that either the pressurizing gas has some lifting effect (unlikely to be large enough to be noticed) or the hopper itself expands as the pressure rises and that this expansion causes a lifting effect, either through the supports, piping or conduits connected to the hopper, or due to damaged seal valves or expansion bellows under the hoppers. You write that after the hopper pressure is stabilized, the apparent weight returns to its original value (the drop in weight disappears). In other words, the error is present only during the period when the hopper pressure is above the inlet and below the outlet pressures. This to me suggests that either the inlet/outlet seal valves are leaking or the expansion bellow is defective (leaking).
So, what should you do? Some would argue that you need to do nothing, because the error is present only when the weight is constant, the hopper is closed at both ends and therefore during pressurization nothing leaves or enters, and once pressurization is over, the weight error disappears. Others might suggest that while waiting for the next maintenance shutdown, you can fix the symptom (but not the cause)—if the underweight vs. pressure curves are repeatable—by using the curve so obtained to electronically correct the measurement.
If you want to find the cause of this strange phenomenon, I would first check if it happens on both or only one of the hoppers. If it occurs on both, I would focus on checking the supports (connected piping, conduits, etc.), because they are probably identical on both hoppers and therefore they would have the same effect. If it occurs on only one hopper, I would first check the seal valves and expansion bellow under that hopper, because the probability that they would deteriorate at the same time on both hoppers is minimal.
I might also note that Figure 1 does not clearly show the location of the load cells, but that makes no difference, because whether the hoppers are suspended from above (load cells in tension) or the cells are located below (compression), they only report the weight, they do not cause temporary variations in its measurement.
Béla Lipták / [email protected]
-----
A. One of the problems I have experienced with load cells on hoppers is arch formation, because in the inverted conical vessels, an arch or bridge formed, so the load cells temporarily registered less weight than was coming down the hopper. This problem is fairly common in mill chutes such as those used in coal-fired power plants. Such collapse and the sudden release of the coal particles can cause severe damage (erosive wear) to the mill chutes.
Another application was in weight measurement of ash in hoppers. Arch formation followed by a sudden release of the handled material have caused a complete bending of a six-foot-long, stainless steel tuning fork having a diameter of about 3 in. The tuning fork had a crystal in it for measuring the weight of the ash in the hoppers.
You may like to examine the physical nature of the materials flowing in your hoppers. My investigations on similar problems suggested three possible solutions, in which unfortunately, the worst one was picked. The root cause was related to moisture in the handled materials causing material accumulation within the hoppers.
1. Mechanical fix: Use pneumatic hammers to periodically knock the hoppers.
2. Chemical fix: Line the internal surface of the hoppers with Tyvar, which is a kind of engineering plastic that reduces friction so the handled materials can slide down easily.
3. Electrical fix: Use heat tracing cables to keep the hopper warmer, so as to evaporate the moisture content in the handled materials.
The electrical fix was a wrong choice, because coal particles easily catch fire. Unfortunately, this was exactly what had happened. A mill chute fire (costing more than the hopper) occurred after the electrical heat tracing cables were installed. Therefore, it is advisable to examine if any patching or welding has been done. Minor leaks can cause a fire if the materials are combustible.
Gerald Liu, P. Eng. / [email protected]
-----
A: Load cells are notorious for issues like this. My first guess is that the geometry changes with pressure and that this changes the force on the load cell. Even the connected pressuring piping may deflect with pressure and change forces on the system.
This appears to be a very large vessel. So even the building structure could deflect due to vessel distortion. We have found it necessary to inspect all the connections to any system with weighing instrumentation. Stay bars are used to enforce alignment and geometry. All rigid conduit must be replaced with flexible conduit or should be so arranged that even tiny deflections will not change the weight on the load cells. Sometimes we have found it necessary to threaten electricians who refused to believe that vertical conduit runs must be avoided as they can change the apparent vessel weight.
Of course, if the temporary effect on the weight can be accurately measured and if it is found to be repeatable, you could compensate for the temporary upset electronically and hide the problem.
Cullen Langford / [email protected]
------
A: Load cells measure strain and this is not necessarily the same as the weight of the vessel. I suspect (but do not know for certain) that the 2-bar nitrogen pressure is "expanding" the hopper slightly, in a way that reduces the loading, by influencing how the hopper it supported.
The mechanical supports needed to isolate equipment such as hoppers from the rest of the plant's equipment can be a quite complex design, while the load cell itself is a relatively simple device. From what I can tell, the hopper is supported off the tilting rocker, and is isolated from the lower structures by the expansion bellows. Is it possible that the expansion bellows are pressurized during the pressurization by the 2-bar nitrogen (a leak)?
It is hard to see if there is any interference that comes from something expanding at the top of the hopper near the tilting rocker. If I am correct, the hopper is suspended with the load cells, so for a reducing weight, I would suspect that expanding the bellows would reduce the measured weight. Think of the bellows as expanding and pushing off the lower equipment.
Simon Lucchini / [email protected]
-----
A: It is my expectation that during the process of charging, a dynamic force is applied by the movement of the charging gas within the piping. This is noted by your load cells as momentarily changing weight, i.e. a force. If the transient weight change is a problem, a detailed analysis needs to be made. Such a study is most likely to show how the charging pipes need to be reconfigured, relative to the sensing axes of the load cells, to minimize the dynamic forces on the load cells. Typically, a very expensive undertaking.
Otto Muller-Girard, PE. / [email protected]
This column is moderated by Béla Lipták (http://belaliptakpe.com/), automation and safety consultant and editor of the Instrument and Automation Engineers’ Handbook (IAEH). If you have an automation-related question for this column, write to [email protected].
Latest from Pressure
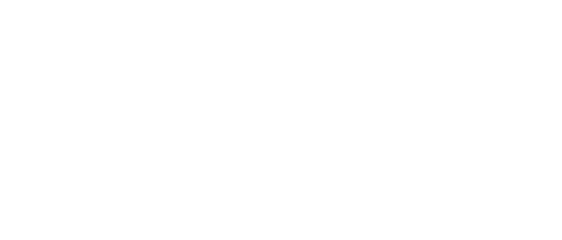
Leaders relevant to this article: