Many years ago, HART became and now remains the most pervasive digital communications protocol in process control—if you have analog 4-20 mA, you probably have HART. But it’s also axiomatic that HART capabilities often go underutilized, and many end users aren’t aware of the latest developments. Here’s a rundown on what you can do with today’s HART, guided by best practices and inspired by creative examples.
Today’s HART actually encompasses four physical layers: FSK and PSK modems, WirelessHART, and HART-IP. The fundamentals are explained in detail in HART Technology: A Technical Overview. Plus, every major control and asset management system in the world supports HART.
WirelessHART brings the benefits of wired HART to applications where it’s too expensive or impractical to run communication wiring. Once a WirelessHART network is established, instrumentation can be added inexpensively and flexibly virtually anywhere.
HART-IP puts HART on internet-protocol (IP) networks, allowing high-speed configuration and applications that use Ethernet. The expected future adoption of two-wire Ethernet-APL technology will vastly simplify the critical infrastructure requirements to deploy HART-IP devices en masse.
HART’s unique position as a protocol that’s already in a huge installed base of process control devices, with up-to-date capabilities provided by wireless, IP and myriad developments to enhance deployment, configuration and the usefulness of HART data, have led to many interesting applications.
Ethernet connects to higher-level systems
The ability to use existing industrial Ethernet and wireless networks in process manufacturing plants and automation systems has made data exchange within a facility, and even throughout global corporate networks, easier than ever. Process and diagnostics data from smart HART digital field instruments is being shared with mid- and higher-level control, asset management and data information systems without having to upgrade expensive process control systems. “At Moore Industries, we are seeing numerous customers using the HES HART to Ethernet Gateway System to collect and transmit valuable, smart HART device data to these higher-level systems over Ethernet via MODBUS/TCP or HART-IP for predictive analysis and control decision-making,” says Charlie Fetty, regional sales manager, Moore Industries.
Figure 1: The stem position HART data is collected from the smart positioners and sent to higher-level systems, no longer requiring the valve controller to communicate the controlled variable (CV), or desired stem position, output. Source: Moore Industries
In a recent application (Figure 1), a Moore Industries customer needed to control two valves that had Siemens smart HART positioners installed, and had a further requirement to communicate actual valve position over Ethernet using MODBUS/TCP to their higher-level systems.
“Originally, the customer wanted to use the Moore Industries PID controllers to control the two valves in order to balance and/or limit each valve’s travel, but the controller’s communication capability did not support MODBUS/TCP as their DCS and historian required,” Fetty says. “Moreover, the higher-level monitoring systems wanted to monitor and record where actual stem positions currently were.This could only be obtained by reading the HART data from the smart positioners.”
The HES four-channel model was used to pick up the stem position HART data from the smart positioners and send it to the higher-level systems, no longer requiring the valve controller to communicate the controlled variable (CV), or desired stem position, output. “The HES was an effective and economical solution that enabled the customer to take advantage of existing HART data from the positioners and share that critical data with their higher-level systems on their existing Ethernet infrastructure.,” Fetty says.
Flowmeters reply in real time
“FCI’s latest design approach to new flow, level, temperature and pressure instruments recognizes that we are all quickly moving away from single-parameter to multi-parameter process measurement, which also must include diagnostics, event logging and asset management over standard digital communication networks—HART and FOUNDATION Fieldbus,” says Randy Brown, director of marketing, Fluid Components International (FCI).
To get the full benefit of HART, FCI’s six families of thermal mass flowmeters are designed to include communication ports with full, two-way I/O. Brown says, “It is simply inadequate in today’s industrial process environment to be limited to only be able to read HART output. You need to be able to write HART commands as well.
“Building in full two-way I/O is or will soon become a de facto industry best practice. This design approach ensures seamless integration, setup and troubleshooting of instruments over the bus.” A validated and FieldComm Group-certified Device Description (DD) file or FDI Device Package provides additional insurance of instrument compatibility.
FCI’s newest ST80 Series Thermal Flow Meter comes standard with HART (Version 7) protocol. “It’s also currently in the final phases of certification in Austin, Texas, for FOUNDATION Fieldbus,” Brown says.
Wireless saves water in a power plant
WirelessHART allows instruments to be added and moved as needed to monitor and diagnose utility usage as well as process parameters. For example, as part of an energy efficiency program, a power plant sought to better understand water flows throughout its widely dispersed waterhead, industrial pump and circulating cooling tower water supply system, but was limited by a shortage of instrumentation.
To realize automatic measurement of water balance in the whole plant, more flowmeters would be required. However, the installation locations of those flowmeters would be scattered, and the distances relatively far. It would be difficult to add cables, so it would not be feasible to add traditional wired instruments to all the locations.
“Considering the actual situation of power plant, Microcyber Corporation proposes to use intelligent WirelessHART technology to solve the problem,” says Jinchao Wang, WirelessHART engineer, Microcyber. In the solution, “The intelligent WirelessHART network is composed of WirelessHART Gateway G1100 and WirelessHART Adapter A1110 with flowmeter for data collection from a short-distance local area network (LAN). Then, radio solves the problem of long-distance communication between control center and field network. Finally, the data are unified and collected to data center, which perfectly meets the requirement of the intelligent water-saving project.”
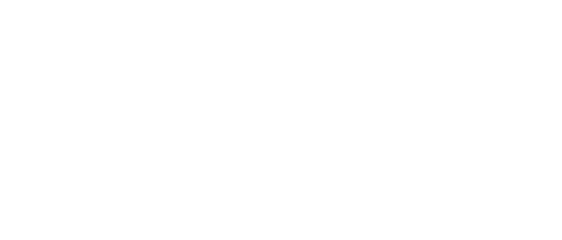
Leaders relevant to this article: