While the use case for off-line, on-demand HART connectivity is compelling, further leaps in plant productivity and reliability await users who pursue full-time, integrated HART connectivity among their field instruments and control and asset management systems.
With off-line HART, the emphasis is on bringing productivity and efficiency to routine and reactive maintenance tasks. But with full-time HART connectivity, users can begin to leverage the HART Protocol's diagnostic power to drive predictive methodologies that can both reduce maintenance costs and improve plant reliability. Integrated HART connectivity also allows instrument and host system manufacturers to implement new synergistic features and functionality not possible over a simple 4-20mA connection. And despite its many years of widespread, proven use, "many people are still unaware of what's possible with HART," notes Scott Saunders, chief operating officer for Moore-Industries International. "HART Communication is about more than just the handheld."
Over the past quarter century, HART usage has evolved from using a handheld communicator for initial configuration, commissioning and occasional troubleshooting tasks to full-time connectivity for online diagnostic and operational alerts. A just completed survey of Control readers indicates that a full 48% of users are using full-time HART connectivity to some extent. And while 32% of survey respondents using integrated HART connectivity indicated full-time communications with at least 80% of their instruments, the median respondent had full-time connectivity to 20-40% of their instruments.
Percentage of HART Users with Integrated Connectivity
- Permanently integrated HART connectivity - 48%
- Used for off-line, user initiated activities - 22%
- Used for real-time alerts and other automated actions - 32%
Percentage of Instruments Permanently Connected
- < 20% = 33%
- 20-40% = 20%
- 40-60% = 12%
- 60-80% = 2%
- 80-100% = 32%
Further, the large installed base of HART-based field instruments in many process plants means that integrated HART connectivity need not be an overly ambitious, all-or-nothing proposition. A first step might be extracting and translating a handful of critical HART diagnostics into digital or analog I/O signals for alarming in an existing control system. In a stepwise fashion then, users can tackle as much HART connectivity as is practical with little risk and tremendous upside as they learn the benefits.
Alternatively, multiplexers provide a relatively straightforward way to pluck HART signals from existing analog I/O cards and wiring without disturbing the current control system installation. For example, a HART interface module can effectively extract the extra process variables gathered by today's increasingly powerful multi-variable transmitters, says Chris Costlow, Yokogawa business development manager for meters and instruments.
And if your plant is among the many out there with an aging control system that must soon be replaced, most modern control systems on the market today offer out-of-the-box HART connectivity at the I/O level that can be used directly in control system strategies or passed through to a complementary plant asset management system, offering a speedy return on a small incremental investment.
Ray Azizian, technical support engineer in Yokogawa's VigilantPlant Services group, notes that while handheld devices have their role, especially for use in hazardous areas, integrated connectivity offers significant visibility benefits. For example, with the company's Plant Resource Manager (PRM) plant asset management software, "you can look into assets and HART devices from the comfort of your desk or maintenance shop," he says.
Diagnostics Drive Reliability Gains
At the Dow Chemical Company's complex in Deer Park, Texas, HART-based diagnostics have helped slash plant trips attributable to instruments and control valves by 70% over the past three years, delivering "millions of dollars in savings," according to Dow's Shadrach Stephens, instrument reliability engineer, and Christopher Garcia, instrument/electrical technology leader.
In order to prioritize their efforts, Stephens and Garcia first analyzed sources of downtime and found that five reactors accounted for a full 48% of instrument- and valve-related outages. "We needed to identify the opportunity so we could justify the return on capital to our leadership. Where could we make the biggest bang for the buck?" Stephens says.
Their first priority was to deploy continuous monitoring via HART for the plant's most critical control valves, which also were the biggest contributors to downtime. The plant now uses HART connectivity to Emerson Process Management's AMS Suite software to help mitigate failures but also to push out preventive maintenance intervals, Stephens says. "We can proactively work with operations to resolve issues without incurring downtime."
"And as we get into more root cause investigations, it definitely helps to have more data," Stephens continues. " HART helps us mitigate problems by creating a culture of making data-based decisions." Up next for Dow Deer Park is dynamic analysis of flow measurement data to identify and rectify issues such as fouling and plugging. "That's the next tier for us," Stephens says.
Instrumentation and host system suppliers can leverage full-time HART connectivity to deliver new features and capabilities not achievable with standard 4-20mA signals. For example, the recently introduced Smartline series of transmitters from Honeywell Process Solutions (pictured) works with the company's Experion PKS control system to increase the combined systems' value proposition, says Ted Dimm, marketing manager for field instruments. The Smartline transmitter's integral graphic display can display messages initiated from the control room (Calibrate me!) as well as indicate the transmitter's readiness for maintenance activities. Also included as part of the pairing's Smart Integration Suite is the ability of the transmitter to send tamper alerts to the supervisory system if an unauthorized configuration change is attempted in the field.
At the MOL Group's Danube Refinery in Százhalombatta, Hungary, diagnostics also are the primary focus of the plant's efforts to stay ahead of valve problems, according to Gábor Bereznai, head of the petroleum refinery's automation and electrical department. "Our PSA [pressure swing absorption] unit is full of control valves and on/off valves, and any valve failure will shut down diesel production at a cost of $300,000 a day," Bereznai explains. With HART- and Foundation fieldbus-based diagnostics "we've avoided many unplanned shutdowns," Bereznai says, "and diagnostics give us more confidence to run longer as well."Having a better handle on valve performance also allows MOL to pull fewer valves at turnaround time, substantially reducing maintenance costs and shortening the time needed before production is resumed. "Ten years ago, we pulled all of the valves," Bereznai says. "Now, we pull two dozen instead of 200, saving $20,000 to $70,000 per turnaround."
Dow and MOL aren't alone in their renewed awareness of asset management's potential or in their push for improved equipment reliability. "Today I hear from many global companies that are investigating methodologies to ensure that devices are working properly," says Frank Fengler, head of device integration for ABB.
Integrated HART from the Start
At Dow Chemical's Deer Park, Texas, facility, the company's drive to increase instrumentation reliability (notably by leveraging HART communication) is promoted internally with its own program logo inspired by the periodic table. The numeral 5 represents the key types of measurement and control devices (pressure, level, temperature, flow, control valve); 34E+03 represents the more than 34,000 devices installed at the facility; 8 represents the scope of the program's reliability services (Subject Matter Expert Investigations, Real-Time Equipment Monitoring, Instrument Assessments, PPM program, Equipment Maintenance Strategies, Top Ten Opportunities, Technology Upgrades, Facility Condition Assessment); and 365.242 is the number of days in a year.
While multiplexers often are used to extract HART data from 4-20mA signals, shunting it off to a standalone plant asset management system, many newer analog I/O modules and associated control systems offer integrated HART connectivity built-in from the start.At Rockwell Automation, for example, no fewer than six different I/O platforms include integrated HART capabilities. "Scalability is important," notes Yuri Zelenkov, product manager for process networks. "If you don't have a full-blown plant asset management system, you can still have that diagnostic information at your fingertips in the control system. Then, once you're up and running, you can begin to programmatically implement basic asset management strategies to go after the low hanging fruit."
Similarly, Honeywell Process Solutions supports integral HART communication in several generations of I/O, including its latest Series C I/O platform offerings. "For an end user migrating to a new system, it really is a plug-and play situation," notes Joe Serafin, product manager, open protocols, for Honeywell. "There aren't any big struggles any more. You're opening the floodgates of information."
And because HART diagnostics are so readily available within modern control system architecture, some 50% of modernization projects also include a companion plant asset management system, estimates John Yingst, product manager for Honeywell's Field Device Manager plant asset management software.
And with WirelessHART of course, all that richness of diagnostic information automatically comes along for the ride, and can be readily integrated into control and asset management strategies, notes Bob Karschnia, vice president, wireless, Emerson Process Management. "It's all about providing more information to keep the plant up and running, maximizing productivity and ensuring safety and environmental protection," Karschnia says. "HART Communication will continue to evolve for decades to come."
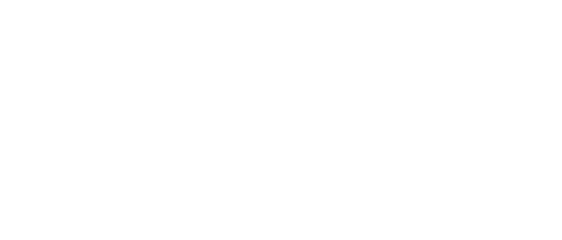
Leaders relevant to this article: