For over twenty years, HART communication has been the largest communication protocol in use in the process industries. There are over 35 million HART instruments installed. HART is simple, reliable and secure. Yet still many HART users are only using only the calibration and configuration capabilities that are the basic features of the protocol.
This is changing, though, and changing fast. As the requirements of end users for more connectivity, more sensors and devices and better maintenance capabilities to enhance production efficiency increased, HART capabilities have kept up with these needs.
But HART has always had the capability to do far more than just calibration and configuration with a hand-held device or a PC. HART was designed from the beginning to connect to control systems and asset management systems.
In order to prosper in the continuing uncertainty of 21st-century business, end users are discovering that they need to have a better grasp of their processes, get faster, more detailed diagnostics, and cut expenses while continuing to improve performance and productivity. When they look at their existing plants, many are surprised to see that they already have the ability to do those things using their existing HART-enabled sensors and devices.
WirelessHART extends the HART protocol for new and nontraditional sensors, such as on/off valves and steam trap monitors. WirelessHART has broken the speed-barrier with one-second update rates and has improved the capability of the HART protocol to be used in closed-loop control.
Most modern control systems are now provided with native HART interfaces. Several vendors provide I/O systems with embedded HART communications. WirelessHART provides, from the gateway, Modbus and Ethernet connectivity to any control or maintenance system, and HART via OPC is in common use.
Ten Essential Best Practices
Leading plants leverage HART communication as much as they can. Here are the ten essential best practices common to all leading plants and their use of HART and WirelessHART. We are going to look at what several leading plants have done with HART.
- Networking and communications protocols are life-cycle solutions.
You cannot every so often rip and replace your networks. This is as true for the plant LAN as it is for the I/O. When designing a network solution, picking the communication protocol is critical for long-term success. In 2005, the MOL Danube Refinery (the 2010 HART Plant of the Year) embarked on a comprehensive maintenance strategy, using HART. The goals of the strategy included:
• Creating an online analysis, transmitter and assembly diagnostics system
• Creating a laboratory and field calibration support system
• Improving plant availability and reduce shutdowns
• Reducing maintenance costs
• Reinforcing CAPEX project support with appropriate assets in the appropriate place.
Having decided to standardize on HART and WirelessHART as the common field device protocol, MOL is able to leverage the functions in the protocol over the life cycle of the 30,000-plus HART devices they already have, while adding new devices and new uses. - Solid planning is essential. Your networks can't grow like Topsy.
One of the most significant benefits of standardizing on HART communication is the flexibility of the protocol. Not only is it backward-compatible to early HART devices, it is the same protocol, whether transmitted over 4-20 mA loops or over Modbus or Profibus or Ethernet or wirelessly. HART has grown and developed and added new features expressly designed to work together seamlessly, interoperably and interchangeably. Through it all, HART has remained simple, reliable and secure.
MOL designed its maintenance system to integrate HART-based device alarms and maintenance alerts all the way to the SAP system. The only way to do that is to plan. Starting with HART makes that planning much simpler. Bruce Power, on the shores of Lake Ontario in Canada, the largest nuclear power plant in North America, planned a redesign of the feedwater heater system to eliminate steam hammer. Using a comprehensive valve control solution based on HART, it was able to run the plant up to full power without the heaters causing alarms and hammer. - Maximize resource availability.
Shifting from preventive to predictive maintenance strategies is the clear choice for maximizing resource availability. Shell Canada Ltd.'s Scotford Upgrader Expansion (located near Fort Saskatchewan, Alberta) has several thousand instruments, of which about 33% are HART-enabled devices. That's still thousands of instruments, and, as Andy Bahniuk, Shell's instrumentation technologist, points out, the company is using 26 different device types provided by several suppliers, including Emerson Process Management (Rosemount), Endress+Hauser, Krohne, Magnetrol, K-Tek (ABB), Fisher Valves from Emerson Process Management, Ohmart nuclear level gauges from Vega International, and Metso valve positioners.
This alphabet soup of different devices and vendors interoperates perfectly—because they are all HART. Shell Canada now uses HART devices everywhere except where a HART device simply is not available. Bahniuk says it is because HART is so easy and is plug and play.
Using HART to drive predictive maintenance allows Shell to increase the availability of its instrumentation resources. - Choose a funding model you can live with for a long time.
Because of the interoperability, interchangeability and backward-compatibility designed into both wired and WirelessHART, you don't have to ever do a rip-and-replace. You can upgrade individual devices and know that they will operate in your system perfectly from the start.
With other device protocols, there may be revisions, interoperability issues and other problems that might cause you to rip out what you have and put in something different. That's a hard sell to a cost-conscious management. It's an embarrassment that can be completely avoided when you standardize on HART. - Establish and nurture team buy-in.
HART is easy to sell to operators and instrumentation engineers alike, because it is simple, yet powerful. Because of the preponderance of HART devices in the field, nearly every engineer and operator already is trained to work with HART commands. Whether it is wired HART or WirelessHART, buy-in is much easier to achieve when the devices are not running a new and different protocol. There is no learning curve with HART. And when there is an upgrade, the operators already know how to use the network—because it still is HART. - Be objective about needs versus wants.
Sometimes, engineers are swayed by other than technical arguments. The drive toward new technology for its own sake often costs more and produces less than a simple concentration on what the plant's goals are and what is needed to produce those results. Shell Canada found that HART fitted its needs better than other fieldbus communication protocols because it was simpler, more reliable and just as secure, if not more. HART, Bahniuk feels, is more straightforward, and he was pleased to note that he can get the same information, including diagnostics and additional PVs, from HART as from any other type of fieldbus.
One project Bahniuk detailed in his application to become HART Plant of the Year was installing a valve position feedback system. Shell felt it had to install some sort of valve feedback system until it realized that HART data could give them valve position on 700 to 800 valves. - Leverage your communications legacy.
MOL already had a significant number of HART-enabled devices when it began its maintenance integration in 2005. By leveraging the use of the entire capability of HART communication, it was able to integrate its maintenance management system with the control system and the enterprise data system easily and without ripping and replacing what was already in place.
One very large benefit of HART communication is that by design it is backward-compatible. Now that MOL, as Gábor Bereznai, head of instrumentation related in the August 2012 issue of Control, is beginning to use wireless instrumentation, it has found that not only can the engineers extend their sensor reach using WirelessHART, but they can also use WirelessHART adapters, such as the Emerson "THUM," to more fully integrate their existing wired devices into the common network. - Integrate your network into all your systems.
As MOL discovered, HART makes it easy to integrate the entire field device network into both the control system and the maintenance system. This makes it easy to deliver the real-time data plant operations needs to fine tune the plant to produce the most revenue at the highest level of productivity.
Shell's Bahniuk related the benefit of HART to loop testing and commissioning—the very first steps to integration of the network. Shell had ordered all the devices pre-configured to avoid having to do it onsite, but only about 50% of the devices were actually configured at the factory. Shell was left to do the others onsite after all.
This, of course, could have produced a huge delay in commissioning the plant. Using the full power of HART, however, Shell created a device database which made device configuration fast and easy, and the engineers were able to show management that the system was 100% accurate. They met their very tight project time and saved a large amount of time and money. - Develop a process to define and minimize risk.
All leading process industry facilities develop risk mitigation plans. Both for operational and maintenance risk reduction, and as an integral part of any security risk reduction plan, HART can serve as one of the key pillars of the plan.
Using the power of HART can produce production alarms as well as maintenance alerts automatically, that can lead to increased functional safety. The fact that neither wired HART nor WirelessHART use TCP/IP means that the field device network is inherently safe from the typical hacker. The WirelessHART security scheme for joining the system and making sure that data transmission is not compromised means additional safety as well. Properly used, HART communications can be a first line of defense against device- and controller-centered attacks, as well as errors inside the plant. - Operate a needs-based solution.
Once you have clearly defined your needs and produced a needs-based plan, you can use the power of HART to help you operate your solution. You have leveraged your existing field device legacy to its fullest extent, avoided any rip-and-replace for sensors or analyzers or final control elements and other devices, and improved the ability of your field device network to handle additions and changes. This built-in agility gives you the confidence to tell management that you are ready for 21st-century operations.
MOL believes that because of its HART-based implementation, it is a world leader in the use of diagnostic information and integration into the asset management system, and thence to the SAP CMMS system via bidirectional communications. It is able to determine the health of the field device system, both individually and as a system and reduce the number of breakdown events and the amount of downtime.
What does this mean? MOL believes that the use of HART technology as the central pivot of both operations and maintenance may yield as much as €700,000 per year in "lost revenue" due to better loop tuning and predictive maintenance.
Leaders in the process industries such as MOL, Shell Canada and Bruce Power leverage fully the power of HART and WirelessHART.
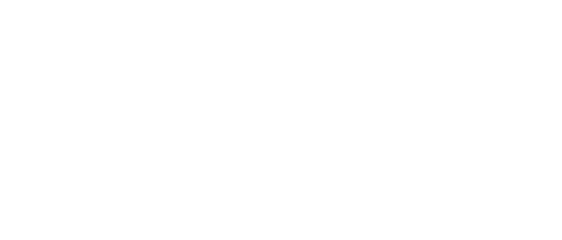
Leaders relevant to this article: