As collective interest in wireless gathers momentum, a growing number of process manufacturers are seeking that first, relatively low-risk application that will allow them to validate the technology within their own cultures and operating environments.
And while the reasoning and justification varies widely, many process manufacturers continue to choose a field-level network of measurement devices as their first foray into the wireless world, according to Emerson Process Management, which today has several years and hundreds of wireless implementations under its corporate belt.
And while none of the applications surveyed in this article may apply directly to your plant’s situation, it’s likely there’s one that has much in common with them. (See figure for application categories.)
Heat Exchanger and Filter Monitoring
Heat exchangers, which often are run until fouling adversely affects unit performance, represent an excellent application for wireless. They rarely are instrumented, even in newer plants, but wireless monitors enable personnel to determine when maintenance is needed.
For example, a major refiner in Europe developed an equipment health system for keeping an eye on its heat exchangers. One of the company’s engineers explains, “Monitoring heat exchangers for fouling allowed us to establish which heat exchanger was the most fouled. This knowledge gives us the opportunity to compare increases in the throughput with cleaning cost and to make better economic decisions.”
Filters present another application opportunity. Many filters are run until they clog, but users can improve their performance significantly and save energy by using wireless monitors. One major refinery uses wireless to detect plugged filters on coker unit pumps, which is critical to prevent damage to the pump on loss of suction.
Tank farms pose a unique instrumentation problem: Each of dozens of storage tanks may have to be monitored for level, temperature, pressure and so on. Because of the cost of running wiring underground over the vast distances involved, tank farms often are not instrumented.
Hunt Refining Company in Tuscaloosa, Ala., U.S., uses wireless temperature transmitters to monitor hot asphalt tanks. When very hot asphalt is added to a tank, the hot fluid can “melt through” the stored asphalt and reach cold pockets, where any moisture present can flash off violently. This can cause a tank roof failure, which costs $200,000 to repair. Wireless temperature transmitters are spaced around each tank to monitor for cold pockets.
Checking Pump and Motor Health
When a vital pump or motor fails, it can cause a very expensive process shutdown, a leak or other problems.
Installing wireless vibration monitors on key pumps and motors is proving a wise investment for process plants. Vibration data is transmitted wirelessly to a control system that detects and diagnoses problems long before the pump or motor fails, allowing the plant to schedule maintenance or replacement at its convenience.
Monitoring Mobile Assets
Some process units, such as skids, pumps, compressors, portable laboratories and test equipment, are mobile. A major life-sciences company installed wireless on its moving skid platforms, which included pumps, filtration and milling equipment. The skids can be moved anywhere in the five-story building, and successfully communicate through 12-in. reinforced concrete floors.
Extreme Environments
Installing instrumentation in extreme environments causes problems for both the instrumentation and personnel. Extreme environments can mean temperature extremes, wet or dusty conditions or hazardous, explosive conditions.
At Usiminas (Usinas Siderúrgicas de Minas Gerais S.A.), one of the world’s top steel producers, wireless temperature transmitters are being used to monitor roll bearing oil temperature at the company’s heavy plate steel mill in Ipatinga, Brazil. “This more accurate and redundant data allows us to better maintain the roll bearings and to avoid unscheduled shut downs,” says Carlos Augusto Souza de Oliveira, Usiminas instrumentation supervisor.
Rotating Equipment and Turbomachinery
Wireless analyzers increasingly are used to monitor rotating equipment, such as turbines, generator sets, reciprocating engines, compressors and other motor-driven systems. Since such machines are often very large and expensive, diagnostic equipment that can predict pending problems allows users to fix small problems before they become very large problems.
Rotating process equipment is also difficult to monitor with wired instruments. At Coogee Chemicals in Australia, wired instruments failed frequently on a rotating reactor, so Coogee installed wireless pressure and temperature transmitters.
Energy Usage Monitoring
Monitoring energy usage is vital, but often difficult to do with wired instruments. When a plant is first built, many measurement points are considered, but not installed because of time or cost. Now, when the measurements are needed, the cost of wiring new sensors is prohibitive.
Wireless lets users go into an existing plant and install the appropriate monitors. For example, at BP Bitumen near Brisbane, Australia, two wireless transmitters were deployed quickly to manage fuel delivery from temporary propane tanks that were rushed into service during a shutdown of the regular fuel system. The wireless transmitters allowed BP Bitumen to monitor the temporary propane system until the main fuel system came back on line.
Temporary Measurements
Wireless allows systems integrators and end users to install temporary instrumentation and monitors in various parts of the process to check on developments during process start-ups or turnarounds, and for troubleshooting.
Heat Tracing
Heat tracing is used in the hydrocarbon industry to keep materials in pipelines and processes at the correct temperature. Wireless makes it possible to monitor heat-tracing temperatures quite easily.
Wellhead Monitoring
Oil and natural gas wellheads typically are located in remote areas, where wiring and trenching are not practical because of long distances. Wellheads often operate unmanned, are rarely visited by maintenance personnel and are potentially hazardous. Wireless makes it possible to monitor these sites. One example is the more than 600 wireless Emerson devices currently on their way to the Morichal District oil fields of Venezuela. PDVSA, the Venezuelan state-owned oil company, will use the devices to monitor more than 180 wells, delivering pressure and temperature data.
“We need more reliable and accurate measurements for better wellhead control in order to increase production and meet our commitment to the government,” comments Euclides Rojas, automation and IT manager at Morichal. “Our long-term goal is to modernize more than 500 wells. Emerson’s wireless communications technology has proven itself in our rigorous field trials and is the cost-effective solution we’ve been seeking for this purpose.”
Consider a Wireless Field Network When Your Application Has…
- Manually collected data: Wireless can eliminate the need to send technicians into the field to read gauges
- “Must have” measurements: Environmental or safety regulations may require additional measurements. Wireless allows the easy placement of instruments where needed.
- Need for diagnostics: Many plants have hundreds of HART-based instruments. Wireless allows access to diagnostic information in HART devices.
- Electrical classification problems: Wireless instruments can be installed in hazardous environments more easily than wired instruments.
- “Want to have” measurements: Wireless permits adding instruments in locations that could not previously be justified.
- Long distances involved: Wireless can eliminate the need for long cable runs and trenching to connect tank farms and similar assets spread over a wide area.
- Many pumps and motors: Plants often have hundreds of pumps and motors. And while continuous condition monitoring is noble in concept, wiring vibration sensors to all of them would be prohibitive. Wireless allows an easy connection.
- Extreme environments: Hot, dangerous and/or hazardous environments make it difficult to install instruments and run wire. Wireless minimizes the problem.
- Crowded environments: Wireless eliminates the need to snake new wires through crowded enclosures and conduit.
- New wiring is too expensive: Installed costs of $50 to $100 per foot can make adding new wired measurement points cost-prohibitive.
- Need for feedback: Manual valves that have no position feedback can cause safety problems. Wirelessly monitoring can cost as little as 10% of a wired solution.
- No other way: Wireless works for mobile assets, remote sites and rotating equipment where using wired instruments is impossible or impractical.
INEOS Köln Prevents Unscheduled Downtime
Emerson Smart Wireless technology is enabling polyethylene maker INEOS to detect blocked filters within polyethylene pellet transportation tubes that can lead to production downtime at its plant in Cologne, Germany.
INEOS could have established a preventive maintenance routine and cleaned the filters on a time-based schedule. However, this could mean that filters are cleaned when they don’t need it, or that filters could block between cleanings. Cleaning and unblocking the filters requires INEOS to stop the blowing and that is not good for the process. Should a blockage take place on a weekend, the maintenance costs are higher. INEOS chose to clean the filters on a predictive basis, before they become blocked and lose too much efficiency. By closely monitoring the filter condition the maintenance team can schedule the cleaning work at a time that will minimize the cost and disruption caused.
INEOS explored the possibility of installing an online system that would closely monitor the condition of the filter and ensure availability. Using differential pressure meters it is possible to monitor the condition of the filters online. However, because of the location of these filters, connecting the required measurement points back to the control system using a wired solution was not feasible.
“The filters are very hard to reach and the high cost of installing cabling to connect the devices prevented us from installing the online condition monitoring points we wanted.” explained Frank Mehlkopf, maintenance engineer, INEOS Köln GmbH.
Instead, they turned to wireless. “We found Smart Wireless so easy to use and we are currently testing it at eight filters in our logistic area,” said Mehlkopf. “These transmitters don’t even need to have line of sight to the gateway....We fully intend to take advantage of this.”
Technochem Troubleshoots with Mobile Measurements
Imagine pulling off this nifty troubleshooting trick using the wired tank farm instrumentation the company initially considered when Huijben arrived last year.
Then, an accurate tank level measurement system was needed, along with an automated method of moving that data into a computer database. In addition to using the data for tracking and managing inventories, it was needed to schedule incoming customer delivery and provide customers with order status, including assurance that their chemical wastes had been treated and destroyed.
Today, Emerson Process Management’s Smart Wireless field network is automating inventory management and monitoring levels in fourteen tanks at TEC. Among the benefits apparent since April 2008 are the elimination of “clipboard rounds,” more accurate real-time data for process efficiency, documentation to verify that specific chemical wastes have been destroyed, and access to the data via the company network. When management personnel are at another site, they can view the process data and order changes if necessary. Electronic connection of select data for customers is being developed.
In an unanticipated bonus, some of the fourteen Rosemount wireless pressure transmitters are moved from place to place to aid in troubleshooting and new process development in TEC’s continuous improvement culture. “The flexibility of Emerson’s self-organizing wireless technology makes it much easier to troubleshoot problems as well as evaluate new applications,” says Huijben. Indeed, TEC is planning further use of Smart Wireless. “At first, we thought this technology was too expensive for us,” Huijben adds, “but we now believe we are saving money with it.”
Continue Reading
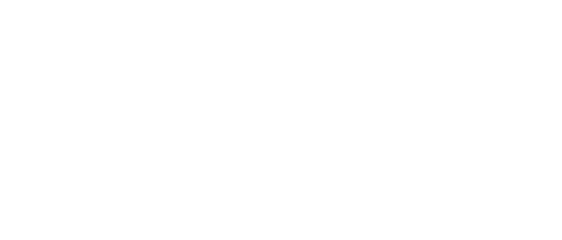
Leaders relevant to this article: