There's been a lot of talk lately about supervisory control and data acquisition (SCADA) systems, most of it having to do with cybersecurity. Originally, and still to some extent, people not very familiar with control system architectures thought all control systems were SCADA, and so it became a buzzword for all types of industrial control systems.
SCADA systems were developed from the radiotelemetry stations installed by the government for military and space program use. Because of the low bandwidth and mostly analog signals, the architecture was developed, so that all of the control was done locally through a remote telemetry unit or RTU, while the data was sent to a control room called the "head end," where operation of the system was monitored. Rarely would anyone attempt to add some control features.
COTS and SCADA
In the 1970s, SCADA systems were purpose-built from the RTU to the head end (the control panel). In the 1980s and 1990s, the advent of PLCs and HMI software made it possible for the newly emerged control system integrator to produce a custom SCADA system out of components and integrate it himself. SCADA system architecture diverged. In many cases, the old line SCADA companies disappeared or were bought out, such as the purchase of Bristol Babcock by Emerson Process Management. The majority of SCADA installations in water and wastewater, for example, are now done this way. Small SCADA companies, such as Multitrode Pty., just acquired by Xylem Corp., continue to manufacture purpose-built RTUs, but provide impressive connectivity to ControlLogix, OPC, DNP3, Modbus and other protocols. The larger oil and gas-centered SCADA brands, such as Bristol Babcock and Telvent, now parts of Emerson and Schneider Electric, respectively, continue to produce purpose-built RTUs and SCADA head ends because their markets need the specific types of intellectual property built into the system architectures, such as flow calculations and custody transfer algorithms.
The PLC or PAC-based SCADA systems are used in many other applications, such as water treatment and distribution, wastewater distribution, and the like.
Radio-Liberated SCADA—Now Come Cellular and Mesh Radios
At first, most SCADA system RTUs were interconnected with the head end using leased lines from the phone company. These were incredibly expensive and could transmit only one variable or status (alarm) setting per leased line. In the 1970s, two things changed. First, digital telemetry from the space program became simple and cost-effective because of the introduction of microprocessors. Digital telemetry could be transmitted via radio (or satellite in the case of remote oil and gas pipelines). Many digital signals could be encoded and transmitted simultaneously at a relatively high rate of throughput. This enabled real control and not just "supervisory" control from the head end.
Radio SCADA systems, especially water and wastewater systems in metropolitan areas were spectrum limited. There were only a few frequencies available in the Industrial Scientific Medical (ISM) bands, and once those were gone, they were gone. The advent of cellular radio made it somewhat easier to use radio telemetry for SCADA, but until the pricing came down, cellular radio made only moderate inroads into applications. In the early 2000s, however, cellular providers realized the potential for SCADA applications, and created pricing plans that made them competitive with leased lines and broadcast radio frequencies.
The use of cellular wireless networks made integrating RTUs relatively simple. The field devices and motor controls connect to an RTU, which connects to a cellular modem. Some SCADA companies, such as Opto22, Advantech, and Exemys have introduced wireless field devices (Exemys has standardized on Zigbee, a protocol similar to WirelessHART or ISA100.11a), so the installation and integration is even simpler. The wireless field devices form themselves into a mesh network with a gateway. The gateway connects to the RTU. Sometimes the gateway itself is wireless, using the IEEE 802.11 protocol.
Integrating wireless field devices using IEC62591-WirelessHART or ISA100.11a makes it possible for real-time diagnostic information, as well as the process values (PVs) and alarms and status indications, to be transmitted through the RTU to the SCADA head end. This means that the cost of operators driving to the remote stations to check status and evaluate and inspect the field devices, pumps and motor controls is reduced to nearly nothing.
SCADA in the Cloud
B&B Electronics' Bill Conley has designed a solution for a small water utility in Arizona that incorporates nearly all of the new SCADA system architecture (Figure 1). Using local radio modems, the individual sensors are connected to a cellular router through the "RF cloud." The cellular router transmits the data via the cellular provider's network to the Internet, and from there it goes to the remote PLC, video feed and remote PC at the system head end.
Like this article? Sign up for the twice weekly Control Update newsletter and get articles like this delivered right to your inbox.
Where previously the system head end was in a control room, Conley's head end is wherever he wants it to be. "Using the cloud for data storage and transmission," he said, "I can control my installation from anywhere using a standard browser, yet maintain a high level of security."
SCADA Apps
SCADA systems are using more COTS products and integrating them like building blocks. Many systems are architected using standard IEEE 802.11 access points and routers. Others use Zigbee, Z-wave and Z-link access points from home automation systems.
Now SCADA meets the app store concept. In February, at the ARC Advisory Group meeting in Orlando, Fla., Inductive Automation announced a marketplace for SCADA software modules for its Ignition software platform. Ignition is a modular software platform that can be customized for applications in a wide variety of industries. Inductive Automation has created a software module store (http://marketplace.inductiveautomation.com/) where users can download, try and buy Ignition modules ranging from small plug-ins to complete MES solutions. The concept is similar to the app store and its competitors on iOS and Android platforms. In the same way they use other app stores, Inductive Automation's users can provide their own modules, and upload them to the marketplace. In the press release announcing the store, CEO Steve Hechtman says, "The ability to instantly buy modules and share modules with the simplicity of an ‘app store' experience will be revolutionary for our users."
Read Also: What Is a Supervisory System?
In fact, the Smart Manufacturing Leadership Coalition is working on a non-proprietary platform designed to permit apps to be combined into systems to control any manufacturing process from automobiles to water and wastewater. It seems this concept is the future of SCADA and industrial control system architecture.
Integration for Everyone?
COTS products, including wireless sensors, network access points and gateways have redefined the simplicity of integrating SCADA systems. With the addition of modular software apps, it will be possible to create a SCADA system of nearly any size or complexity with the efficiency of plug-and-play utilities. This will lower the cost of system design and widen the number of systems in use.
Figure 1. The sensors link to the cellular router via RF connections.
Latest from Safety Instrumented Systems
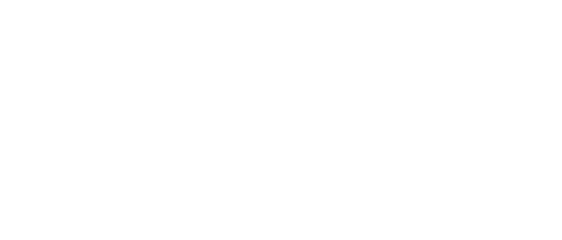
Leaders relevant to this article: