Roadmap for Best Practices in Manufacturing
Manufacturing historically has viewed implementation of safety practices as punitive actions or compliance activities. Today, safety represents opportunity to gain a competitive edge.
For best-in-class manufacturers, the combination of global safety standards, advanced safety technologies and innovative design approaches are turning safety into a core function that delivers significant business and economic value. This includes financial returns beyond the benefits of reducing costs associated with incidents and medical expenses.
In fact, best-in-class companies are the safest and most productive. A recent Aberdeen Group study, co-sponsored by Rockwell Automation, measured the relationship between automation safety and productivity and showed the best-in-class companies had 5 percent higher Overall Equipment Effectiveness (OEE), 4 percent less unscheduled downtime, and significantly fewer injuries and repeat accidents compared to peers. OEE is a widely used measurement of how well a manufacturing plant performs relative to its designed production capacity.
These forward-thinking manufacturers understand that a well-designed safety system can help improve their efficiency, productivity, and business and machine performance – ultimately helping reduce costs and differentiate themselves in the marketplace.
So, how do best-in-class manufacturers provide a safer working environment that is compliant with applicable standards and supportive of a productive and competitive operation?
At the core, they comply with safety standards without jeopardizing productivity by combining safety and operational systems through a risk management approach, Aberdeen found. The most successful risk management approaches included a strong safety culture, formalized risk management strategy and technologies that integrate safety systems with the standard automation system.
Defining Best-In-Class
The Aberdeen Group study defines best-in-class manufacturers with four key performance indicators (KPIs) deemed critical to the success of the safety program as well as plant safety. They include the OEE, repeat accident rate, injury frequency rate and unscheduled asset downtime.
Respondents to the study were divided into three categories, best-in-class, industry average and laggards:
- The top 20 percent, or best-in-class, are those with the highest OEE and the lowest accident and injury rates.
- The lowest 30 percent have the lowest OEE and the highest accident and injury rates (see Table 1
Furthermore, best-in-class manufacturers average five percent higher OEE and four percent less unscheduled downtime than industry averages, while having significantly fewer injuries and repeat accidents than their competitors. Just as important, those manufacturers also average significantly fewer injuries (1 in 2000 employees vs. nearly 1 in 100 employees) and repeat accidents (0.2 percent vs. 2.4 percent) than industry average manufacturers. This makes for a much less stressful and more productive work environment – and reduces liabilities.
The bottom 80 percent of manufacturers can follow the best practices of the best-in-class industrial plants and develop a formal, effective risk management strategy, foster a safety culture and invest in advanced technologies, often including systems that integrate standard and safety automation control, to help foster a safer work environment and increase productivity.
Creating a Safety Culture
Creating a workplace that values and embraces safety programs is unfortunately not a commodity to be purchased, but rather an atmosphere to be encouraged by plant managers. Without the buy-in of everyone from upper management down, implementing an effective safety culture is difficult. Managers must develop relationships with the environment, health and safety practitioners in the plant, and help each individual understand the role machine and process safety plays in their plant.
Specifically, companies need four critical components if they are going to be successful in establishing a safety culture – credibility, commitment, accountability and rigor. If employees don't believe it's a credible program, i.e., if they believe it's a marketing ploy or simply nice words, then it will surely fail. What builds that credibility is continual senior management commitment driven and adopted throughout the organization. Most companies have some management commitment in words and deeds, but it must result in action and funding. Without this, a safety program cannot survive.
A safety program also won't survive without accountability and ownership within the organization. In a successful safety culture, everyone is a stakeholder.
Lastly, rigor is key, because it reinforces the credibility of the program, meaning it becomes more "real" because it has a well-defined structure, i.e., documentation, training, milestones in the process, key success metrics, etc.
If a manufacturer has all four components along with buy-in throughout the organization, then safety becomes a core value. Without buy-in throughout the organization, it is difficult to maintain a safety culture and to view employees as critical assets in the organization – no matter how a risk assessment is conducted.
Developing a Formalized Risk Management Strategy
Establishing a formalized risk management strategy to identify, prioritize and mitigate risks is a key factor in addressing top level safety pressures while maintaining and improving productivity. The Aberdeen study found that manufacturers with an effective risk management strategy are more likely to have established procedures than those in the Industry Average or Laggards categories, as shown in Figure 3. Furthermore, best-in-class companies consistently had a significantly higher capability to assess, rank and create processes to mitigate risks.
Conducting a risk assessment is the first phase of the Safety Life Cycle, as defined in standards IEC 61508 and IEC 62061, which provides a detailed, systematic design process for machinery applications (See Figure 4). A risk assessment helps determine what potential hazards exist, and which safety mechanisms should be implemented to help ensure adequate protection. A risk assessment provides the basis for the overall risk reduction process, which involves the following steps:
- Reduce the risk of hazards by using inherently safe design concepts
- Employ safeguarding and protective measures with hard guarding and safety devices
- Implement complementary safety measures including personal protective equipment (PPE)
- Help achieve safer working practice with procedures, training and supervision
After a risk assessment, the designer will define the functional requirements of the machine and begin designing the safety system. The next step is to verify and validate the performance of the safety system design. The final phase in the life cycle is to conduct maintenance on the machine as needed and make future improvements as new technologies become available.
Investing in Advanced Safety Technologies
Traditionally, plants kept safety technology separate from their standard automation systems. Many manufacturers still embrace this approach and value employing workers whose main responsibility is to monitor and control safety systems.
However, this approach generally costs more and creates numerous design and integration issues.
The Aberdeen study found that although a majority of manufacturers continue to separate the two systems, 47 percent of the best-in-class are integrating. With many recent changes to safety standards and various advances in technology, many manufacturers find it increasingly easier to merge safety and standard control systems into a single platform, especially for discrete applications. One control platform minimizes the need to manage two disparate systems while lowering hardware, software and labor costs.
In addition to investing in single control platform technology, the study found adopting industrial Ethernet as the networking protocol to be a best-practice. Industrial Ethernet allows for a seamless transport of data between safety controls and standard control devices, allowing for increased visibility into safety data, among a slew of other advantages. The EtherNet/IP network, for example, allows users to effectively manage real-time control and information flow throughout the manufacturing and IT enterprise. By using a single, open protocol as the "networking backbone"f for the entire enterprise, users have the flexibility to control, configure and collect data from any point in the system to help simplify communications, improve productivity and protect manufacturing systems.
As safety standards and technologies continue to evolve, industrial plants with formal risk management programs in place are better equipped to keep up with safety compliance, and achieve superior operational performance. Forward-thinking manufacturers will work toward achieving or maintaining this best-in-class status by embracing a safety culture, creating a formalized risk management strategy and by investing in integrated safety technologies.
For more information on contemporary, integrated safety configurations, global standards, and how users are employing safety automation in their organizations, visit the Rockwell Automation Safety Resource Center: http://discover.rockwellautomation.com/safety.
Latest from Safety Instrumented Systems
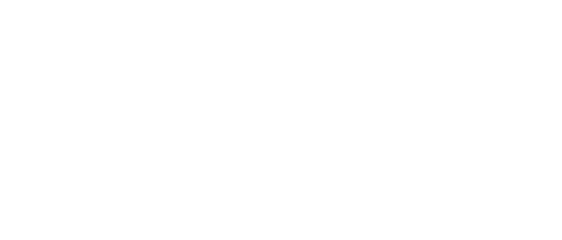
Leaders relevant to this article: