By Katherine Bonfante, Digital Managing Editor
Sustainability is not new. In the paper and plastics industries, recycling has been a way of life since the 1960s.Ā For years, even decades, some manufacturers have been involved with cogeneration, alternate energy, water reuse/recycling and chemical reuse, and many more companies are following their example. What is new is the insistence from the public, the economic community and the government that we must be sustainable now. Add to that the growing understanding that sustainability efforts can drop quickly to the bottom line, and you have much more than a feel-good marketing effort. Now you're talking about a sensible business strategy that's a win-win for manufacturers, their customers and the environment.
The Economic Calculus
At the Siemens User Summit in 2008, Bruce Taylor, then with Suncor Energy USA Inc. (www.suncor.com), described the sustainability task that its executive management set for him. They asked Taylor and his team to produce a viable energy management system. The first challenge they addressed was not on the plant floor, but in the accounting department.
"We started building awareness that energy is not a fixed cost," said Taylor. "There was an 'abundance' energy mentality with aggressive focus on production growth. Our energy and carbon dioxide costs were not fully valued. Our energy budgets would more than double if fuel internally consumed was assigned a cost. There was distributed accountability for energy management, and there was a lack of linkages between targets and performance."
Taylor continued, "Just from shaping behavior, we can impact a 3% to 5% annual improvement in energy costs, culminating in a cumulative improvement of 25% to 30% in carbon footprint."
How is the new mentality different from the old? There's no entry in a cost-accounting rollup for saving the environment or moderating global climate change.
What happened is best described by a concept called the "economic calculus." As with the air and water pollution control drives that erupted in the 1960s after the publication of Rachel Carson's The Silent Spring, the economic calculus was widened to permit those costs to be incorporated into the ongoing operating costs of an enterprise.
No company today would think twice about including air or water or solid waste pollution controls and mitigation strategies in a new or rehab plant design. The management support Taylor received is a clear indication that the economic calculus is widening once again, this time in favor of sustainable manufacturing.
More New MathāSustainability Drivers
"Energy is a hot topic right now, mainly because of the volatility of energy costs," says Marcia Walker, global market development manager for sustainable production at Rockwell Automation (www.rockwellautomation.com).Ā "For the past 12 months, energy costs have gone down. However, industry professionals are preparing for the future, and they want to able to keep energy costs under control, especially because energy is the largest variable production cost."
The cap-and-trade policies under discussion now have also put energy costs in the spotlight. Whatever the final shape of these policies, manufacturers want to be readyāand controlling energy costs is part of that preparedness. From an environmental perspective, when manufacturers are able to control carbon emissions, they also are able to control energy usage and save on their energy costs. Most manufacturers today continue using coal- or gas-fired energy processes with big emission footprintsāand big emission footprints cost more than small ones.
Environmental policies have a financial impact. For example, getting rid of industrial waste often is, in the end, more costly than implementing green practices. Furthermore, local communities are discouraging industrial plantsāusually through taxes or feesāfrom dumping industrial waste into landfills.
That financial penalty encourages creative waste disposal. Many process plants send their industrial waste to re-use facilities. Here businesses use someone else's "garbage" for raw material. More than a dozen years ago, Fluke Corp.'s (www.fluke.com) George Bissonnet showed Control's editor in chief, Walt Boyes, that the circuit board and spent chemical recycling business he developed was actually a profit center.
Safety compliance is another strong driver in sustainability. This is based, one assumes, on the proposition that a safe plant is more sustainable than one prone to damage from unsafe practices. Study after study has shown that safety compliance, both in traditional workplace safety and in process safety management produces higher profit levels over time than ignoring safety issues does.
Walker adds, "[The process industries] are looking at things through a new lens. They want to improve their environmental performance, not just for responsibility reasons, but also for financial reasons."
Manufacturers also have a responsibility to shareholders to maximize profits. As T. J. Rogers, chairman of Cypress Semiconductor (www.cypress.com) says, "If you want businesses to do something, show them the money." This is another example of that widening economic calculus.
What Is Sustainability Anyway?
Rockwell's Walker explains that sustainability consists of making operations cleaner, safer and more energy efficient. "[Rockwell Automation] buckets sustainability into energy efficiency, environmental applications and safety. Energy, environment and safety are the three main components of it, with energy being the component that surprises people the most," says Walker.
Going green is not about doing just one thingāreducing waste, reducing energy cost, minimizing the carbon footprint or reusing materials in the production processes. Green practice in process automation is about mixing and matching sustainability efforts, creating the perfect balance at the plant level, not only benefiting end users' return on investment, but also benefiting the environment as a whole.
"It's a bit surprising that sustainability is being treated as something new," said Mark Lee, Coca-Cola's director of commercial product supply engineering at the Rockwell Automation Manufacturing Perspectives event in 2008. "It's really just good business practice."
For Lee and other end-user executives, sustainability in many ways does represent a rebadging of the manufacturing professional's stock-in-trade: a continuous improvement process aimed at increasing efficiency, reducing waste, easing environmental impact and boosting workplace safety.
"Sustainability is part of the relentless pursuit of waste elimination," Lee said. "It's part of being a world-class manufacturing organization."
Siemens Industry's (www.siemens.com/entry/cc/en/) marketing manager, Ken Keiser, adds, "Sustainability is a way to use green technology to help both the environment and the company. Instead of ripping out and throwing away systems, customers can lengthen the life cycle of the equipment they have by just changing a few key components and using as much of what they have as possible."
Getting There from Here
It's easy to see that the pressure is on to "go green," but the best way to respond to that pressure isn't so easy to discern. Few in the process industries have a clear strategy for doing so. Deciding which green initiatives make most sense for a particular operation, much less how to implement those initiatives is a complex decision. But help may be on the way.
In 2008, the Aberdeen Group (www.aberdeen.com) conducted a survey of manufacturing companies about their specific sustainability initiatives. The findings revealed that the companies that have the best sustainable production performance also tend to have the best performance in other areas such as financial performance.
Rockwell Automation used these findings and partnered with Aberdeen to launch its Sustainability Assessment Tool in January of this year. "This tool allows automation professionals to answer questions specific to their sustainability needs," says Walker. "Not only can a sustainability assessment tool guide industry professionals to view their entire processes at a glance, but it gives them the opportunity to identify their biggest target for improvements. Assessment tools and processes give professionals a guide or starting point towards meeting their sustainability goals."
Walker adds that an in-depth process sustainability assessment can help identify the potential return on investment for many businesses. These specialized assessments help determine whether the initial company involvement requires just a capital investment, a personnel investment or a combination of both. Assessments can pinpoint the duration of the sustainability process and how much capital investment to expect in return.
Control system integrator Indesco (www.indesco-usa.com/home.html), Louisville Ky., has been using the tool to help its customers achieve their sustainability goals.
"To become sustainable in the process automation industry, you can't just change the focus on one single piece of equipment," says K.W. (Bill) Holladay, president of Indesco. "It's not just about that one process. It's about all that can help improve your carbon footprint or become more sustainable," he says. "Rockwell's Sustainability Assessment Tool doesn't tell you that you have to replace this or that component. It doesn't tell you that you have to drag out this new technology, and put it in. What the tool does is help you look at the company as a whole, comparing you to what is going on in the industry and measuring you against other companies that are being successful."
Live Monitoring
Indesco's vice president of sales, Thad Parrott, says that live monitoring is essential for achieving sustainability goals. "When our customers use live monitoring systems, they know within one month what's working and what's not. The reason they know this is because they have been able to tweak things each week as the process goes along," says Parrott.
As Holliday says, "Monitoring processes is a big thing. You can't fix what you can't see."Ā
Take the case of General Mills. "We were told in 2005 to reduce our energy footprint by 15% in five years," explained Dave Spryshak of General Mills in November of 2009 at Rockwell's annual Automation Fair. "We discovered that the single biggest energy consumer in our plants was the HVAC system."
Spryshak's team discovered that by applying process control principles to the control of airflow in plant buildings, the company could improve air quality indoors and out, and reduce electricity use 17% to 49%. Gas usage was reduced 14% to 63%. In one case, Spryshak was able to reduce electricity consumption 3 MW, and saved $1.5 million in a single year.
The project team used cascading loop control for air volume, an enthalpy algorithm to use the least-cost energy source, multiple room-space recipes, and used CO2 measurement to determine room occupancy and derive airflow requirements.
General Mills has modified 16 plants and is rolling out the changes across the rest of its enterprise.
How to Implement Sustainable Measures
Ray Zimmermann, of RJZ LLC, a sustainability and energy optimization consultant, who also spoke at Automation Fair, outlined the overall plan for "going green" in a process plant. First, he said, "You have to change the corporate culture to make sure that energy-saving projects will continue to perform properly."
The U.S. industrial sector is the number one consumer of energy in the nation. All four major economic sectors recorded tremendous growth in their use of energy, yet the industrial sector used the largest share of total energy.
He added that top-level management buy-in was critical to energy-optimization project success, and that it was necessary to make it a company priority, establish structure and committees, identify key personnel at each level of management and establish an energy missionāthat is, integrate energy into overall company strategies. Then, establish objectives for energy accounting and data requirements, and develop a plan to heighten communication and make energy a visible priority.
After that, Zimmermann said, select partners with experience, set leadership priorities and move forward to study and audit energy usage. Once you have completed the audit, you can prioritize the energy saving projects you want to complete, and then get to work.
Changing the Lightbulbs
Sometimes, it really can be that simpleāif changing the bulbs at 300 facilities is simple. Osram Sylvania (www.sylvania.com) and its parent company, Siemens Automation AG, (www.siemens.com) have partnered to design different energy-efficient lighting technologies, as well as state-wide recycling programs to reduce the amount of carbon emission produced in the process automation industry. These programs and green practices allow Osram Sylvania and its participating customers to reduce the amount of glass, metal, mercury and fluorescent substances used in Osram Sylvania's lighting products.Ā
One company currently benefiting from Osram Sylvania's green products, such as the Quicktronic family of ballast and lighting controlsāthe T12, T8, T2 and T4 fluorescent lampsāis Norfolk Southern Corp. (www.nscorp.com/nscportal/nscorp), the Virginia-based rail transportation company.
Norfolk's primary goal was to become sustainable throughout its processes, and with Osram Sylvania's help, it retrofitted more than 300 of its locations, and is anticipating an annual energy savings of 50 million kWh and an annual CO2 emission reduction of approximately 76 million pounds.
SustainabilityāTrend or Fad?
Sustainability right now seems like a fad, but it isn't. Currently, sustainability programs are taking over corporate goals, and everyone wants to accomplish sustainable practices for their own reasons.
"Three to four years ago when people started talking about sustainability they would just shrug it off," says Walker. "Many thought sustainability was just a fad."
The process industries today are seeing an increase in the number of employees that are hired to perform sustainability-related jobs, and these companies annually publish corporate responsibility reports.
Corporate human-resources departments also play an important role in making sure green initiatives are part of business plans. Employees want to work for environmentally responsible corporations, and businesses want to hold a strong sustainability performance because they use this to attract new talent.
Financial officials know that when carbon trading comes along, this will be a costly process for corporations. In order to reduce energy costs, reduce emissions and remain profitable, industry must find ways to make money. Trading emission credits could be the way to go.
Growing government pressures and tougher environmental and safety policies act as regulators pushing sustainability initiatives as the norm, as the economic calculus widens yet again.
Marketing also plays a role in setting sustainability practices as a trend. Consumers today demand green products and stockholders are putting pressure on manufacturers to deliver and meet popular demands, while operating in a sustainable fashion, and with a lower carbon footprint. As Kermit the Frog used to sing, "It isn't easy being green."
However, 10 years from now, sustainable practice will be woven into daily operations, and running a green plant will be the only way to remain in business and profitable.Ā
Latest from Safety Instrumented Systems
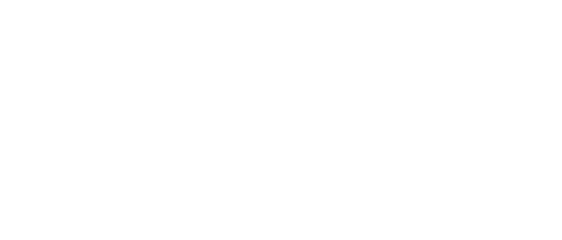
Leaders relevant to this article: