In keeping with the "Smart, Safe and Sustainable Manufacturing" theme of this year's Automation Fair in Orlando, Fla., energy management is getting a lot of attention. Beginning yesterday with the Manufacturing Perspectives panel discussion "Optimizing Production with Power and Energy Management," continuing with this morning's Energy and Environmental Industry Forum and culminating at Booth 528 with the introduction of the Energy Management Industrial 'GreenPrint' road map, attendees who wanted to get their arms around the changing business of energy management got plenty of food for thought.
Yesterday at the Manufacturing Perspectives panel, Dr. Neal Elliott, associate director of research at the American Council for an Energy-Efficient Economy (ACEEE) summed up the opportunity and the challenge of the new energy landscape this way: "The smart grid will give us an opportunity to change things."
"We need to make energy measurements in terms of dollars and cents." Rockwell Automation's Phil Kaufman explained the company's Industrial GreenPrint methodology, and how it can be used to relate WAGES (water, air, gas, electric and steam) consumption to economic performance.
Philip Kaufman, business manager, industrial energy management at Rockwell Automation, added that one of the things that should change is the way we look at measuring energy. "We need to make energy measurements in terms of dollars and cents," he said. "Right now, we don't know how to optimize energy usage in terms of dollars. We need a unit of measure that turns kilowatts or therms into dollars so we can do ROI calculations."Rockwell Automation's solution is to first convert WAGES data (water, air, gas, electricity and steam) usage into their equivalent energy value in millions of BTUs, which can then be used to calculate the actual cost of the energy used in a particular process. "The ultimate goal is to be able to look at energy like any other raw material," says Kaufman. "We want to be able to use it as another unit of production. We've never looked at the fact that the operations manager, armed with this kind of data, can affect profitability."
Rockwell Automation has addressed this challenge with the Industrial GreenPrint methodology. Industrial GreenPrint is a customized company roadmap to measure and monitor energy consumption by individual energy-intensive assets—process units, loads, machines and lines—to more effectively manage consumption patterns for the plant, predict the overall impact of production changes on energy use and emissions and ultimately automate production for optimal energy consumption across the enterprise.
There are four stages to the methodology—Awareness, Efficiency, Optimization and Aggregation—that can be implemented over time as manufacturers gain better understanding of their energy consumption patterns.
The Awareness phase is all about data gathering. Manufacturers can use their existing automation devices and systems to obtain much of the necessary WAGES data needed to understand consumption in a way that helps them lower their utility costs and greenhouse gas emissions.
This first step is relatively easy, said Kaufman. "Most manufacturers have 40% to 60% of the equipment necessary to do this already," he said. In addition, Rockwell Software RSEnergyMetrix provides measurement and verification solutions for tracking WAGES consumption data, gathering it from sensors and control systems already in place.
The second stage of the Industrial GreenPrint methodology builds on that data, allowing manufacturers to implement forecasting, load aggregation and rate analysis exercises. The Rockwell Software Enterprise Energy Management solution can help by providing real-time energy monitoring and management capabilities, such as weather-normalized predictive modeling, as well as worldwide key performance indicators, dashboards and reports for comparison of multiple facilities.
Stage three of the methodology enables manufacturers to optimize their plant-floor assets by modeling production with energy as an economic variable. By combining the enterprise-wide WAGES data collected at stage two, including production metrics, regulatory reports and behavioral and climate forecasts, manufacturers can balance the many process variables inherent to production. The Rockwell Software Economic Energy Optimization solution automatically modulates production to align with a manufacturer's optimal energy profile. Model predictive control and optimization applications minimize energy usage while optimizing production yield for dryers, evaporators, fermentation, distillation, grinding and crushing, hydro-metallurgy, material blending, reactors, extruders, furnaces, ovens and more.
By visualizing WAGES resources consumed by manufacturing processes versus the facility itself in the earlier stages of the Industrial GreenPrint methodology, the fourth stage allows manufacturers to compare that information against production output data and other enterprise resource planning-level information to gain higher returns on their WAGES resource expenses. As a result, companies can eventually document energy on their production bill of materials and enhance their supply chain to include energy as an input. Rockwell Automation Energy Supply Chain Management solution aggregates production data with WAGES consumption information for energy and greenhouse gas reporting. This solution manages energy as a raw material, allowing manufacturers to view energy as a manageable, documented input to production and ultimately include energy on the production bill of materials.
Rockwell also offers consulting services to advise manufacturers in the implementation of any of these solutions.
Kaufman reiterated a number of times that the first step in the Industrial GreenPrint journey toward complete understanding of energy costs and usage is to gather data. This can be as simple as taking advantage of the many free audits available from various government agencies, extracting data already resident in your systems, or even just finding out where you stand in comparison to your peers.
If you're in Orlando for Automation Fair this week, visit Booth #528 and take the iPad-based survey that enables you to compare where your operations stands in comparison to those of other Automation Fair visitors. The survey is also online at www.RockwellEnergyEvaluator.com.
Latest from Safety Instrumented Systems
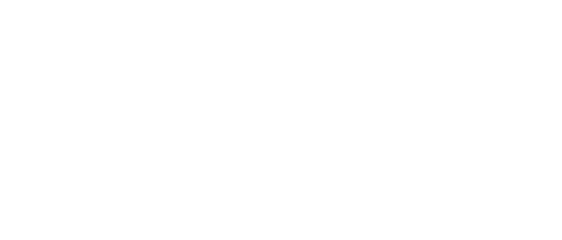
Leaders relevant to this article: