To see additional online resources visit ControlGlobal.com/service_plant_now.html
By Nancy Bartels, managing editor
That question brings to mind the image of the blind men and the elephant. What you think EAM is depends on which piece of the elephant you’re touching. Is it really just CMM (computerized maintenance management)? Or is it CBM (condition-based monitoring)? Or one of the PMs—preventive or predictive maintenance? Is it an asset database and work order management system, spare-parts inventory tracking or a plant-floor-based road to business process optimization? The “next big thing” or merely an acronym in search of an application? Or all of the above? That depends on who you ask.
“EAM is different from industry to industry,” says Charles Gifford, director, lean production management, at GE Fanuc. “Some think of it as [something used in] continuous process—oil & gas, etc. It’s everything to a continuous process, where they’re running 24/7. They have thousands and thousands of I/O points. They’re highly automated, very sophisticated. By law, all hazardous factories have to have sophisticated maintenance in place. The chemical industry moves the needle far to the right and does predictive maintenance. The needle moves way to the left for most batch and discrete manufacturers. They’re doing preventive maintenance.”
David Berger of Toronto-based Western Management Consultants, says “I see no real difference between a CMMS and an EAM. It may have been a distinction many years ago, that CMMS was a small, stand-alone system, as opposed to a big enterprise-wide one. But in my view, it’s still a CMMS. I’m not slamming vendors, but the distinction is not really relevant in today’s world, and it only confuses users.”
That vagary is one of the reasons that EAM is often the red-haired step child of manufacturing software. Another is the persistent islands of automation that make up the plant-floor environment. “The operations guys have targets,” says Jeff Tropsa of Siemens Energy and Automation. They need to provide so many widgets. Maintenance is gauged by the number of work orders they complete. Neither side is aware of what’s happening on the other side.”
Finally, there’s the lingering belief that “maintenance is an evil cost,” says Neil Cooper, general manager of the Avantis business group, the EAM arm of Invensys, pointing to one of the dirty little secrets about maintenance that makes management less than eager to spend more on it than absolutely necessary. “Fifty percent of equipment failures are caused by faulty maintenance. That’s the double whammy of doing preventive maintenance. You’re spending too much anyway and then you run the risk of introducing a failure.”
Another cost-related reason is that the benefits of a state-of-the-art EAM system simply aren’t clear. Most manufacturers have other pain points that need attention first. “When you’re competing for IT systems, you’re competing against ERP, MES, etc. for software dollars, and everyone has the same ‘the sky is falling’ story,” says Gifford. “I don’t believe the EAM vendors are making the same business case as other software vendors. Maintenance is the last place where the money gets spent.”
No wonder many manufacturers—both process and discrete—are lagging well behind the technology in terms of adoptions. Gifford says “In most plants in America, EAM is two to three revisions behind what the vendors’ are offering.”
But a few end users in the process industries (call them “early adopters,” “leaders” or if you’re inclined to cynicism, “bleeding-edgers”) have taken the EAM concept beyond the old equipment database, work-order-generating software of even a few years ago. They are using their maintenance systems to help them, not just with maintaining and tracking their assets, but supporting their regulatory compliance, improving their product quality and, ultimately, their bottom lines.
The Drug Company
For drug maker ImClone, regulatory compliance is one of the big drivers behind the sophisticated integration of its control, maintenance and ERP systems. The goal says Steve Greguske, Imclone’s principal control engineer, is to draw data directly from the controls, taking advantage of the history in the database and analyzing it for decision support—not just about maintenance, but about process optimization—and for proof of regulatory compliance.
At ImClone’s new $330-million facility in Branchburg, N.J., which was licensed by the FDA just this year, the company’s SAP ERP system and its Allen-Bradley Logix control platform and Rockwell Software’s FactoryTalk Asset Centre work in tandem to handle not just maintenance, but documentation for compliance.
“We’re using SAP for scheduling work orders for maintenance. But because of the advantages of the control systems, we’re integrating them [with SAP] to allow us more proactively to see when our systems need maintenance. Using the data historian, we can go back in time to see how things were degrading and figure out how to do thing better,” explains Greguske.
This information gives Greguske important clues about the timing of maintenance, which in itself is a money-saver. “We keep track of the frequency with which we replace parts or check on them. Now we have data we can look at and decide that maybe we only need to do certain maintenance every three months instead of monthly. Or say we’ve been doing the check every six months. By looking at the data, we may conclude that we should do it every three.”
The SAP system generates the maintenance work orders at ImClone, and the Rockwell historian provides the data that enables engineers to make adjustments to the maintenance schedules or the SOPs. “The integration is not entirely seamless,” says Greguske. “What we use the historian for is to tell us, ‘something is weird.’ Then it will email the appropriate person who then decides what action is to be taken, including whether to issue a work order.”
This linkage of plant-floor data to enterprise and maintenance systems has another important driver—compliance. “The FDA doesn’t make big demands: Just prove that what you say is true,” says Greguske wryly. “From that demand comes a whole host of things that need to be done. We have to do a lot of tracking. We do assessments of every change, asking how it will impact the process or the product.”
The automated tracking is key to this documentation. “When you’re in the middle of a plant and things are running all around you and you’re in operation and something happens that’s different, it’s hard to remember what you did before. Now you have the data—objective documentation—that can show you exactly what you did,” says Greguske. “You have readily accessible data without digging through a lot of paper.”
And the benefit of gathering and analyzing all this data?
Hard numbers aren’t available, but “production capacity is up,” says Greguske. “Capacity is up. What we’re seeing is that we’re not hiring people as we gear up. We’re getting productivity increases at a time when we need them.”
The Electric Company
If ImClone is doing cutting-edge data analysis for maintenance optimization, Statnett, the state-owned provider of electricity for Norway, with 2006 operating revenues of NOK 6,661 billion (€868,352,216 or $1,230,171,648) is upgrading an old system more slowly and using its new EAM to ease its transition to a new business model. Like many state-owned operations, it is facing deregulation and the challenges of learning new ways of doing business. Rethinking and revamping its maintenance operations are part of that.
It went to its ERP provider IFS, which also has a strong EAM module, for help with the transition. Using its ERP vendor also plays into Statnett’s strategy of minimizing the number of software systems it uses, says Statnett’s Einar Mørk. The company already used IFS for bill processing, project management and finance, so when it discovered that the vendor also had EAM functionality, it made sense to use it. “There weren’t so many changes to the system,” he says.
Statnett’s journey to cutting-edge EAM will be a long one. It has been using the IFS system since 2001 for substation maintenance and since 2004 for line maintenance. Prior to that, says Mørk, it was working with a 20-year-old paper-based system that was less than a success. In the end, it was relegated to managing spare parts. Most of Statnett’s maintenance is handled in-house, but some line maintenance is handled by outside contractors. Work orders to the far-flung power stations across Norway are still sent by mail, says Mørk. While changing that arrangement is part of the plan, it is not the first priority.
That is managing all the preventive maintenance functions, says Ulf Stern, IFS global director for asset management, including planning for investment and upgrades. “The main idea is to plan and execute preventive and emergency work, support inventory and scheduling and manage all the maintenance technicians, including third-party suppliers,” he says.
One of the chief aims of the system is to strike the right balance between preventive and emergency work across the electrical grid, says Mørk. The focus is on preventive maintenance, he says, with the company now having a 70% preventive/30% repair ratio. The motivation is there to bring the repair number down. “As a utility, we have to pay for any downtime,” Mørk explains.
Change at Statnett is incremental. “This is a difficult process,” says Mørk. “You have to change the culture, the people, the leadership. It’s not just learning to use IFS. You’re designing new work descriptions, helping people understand how the tool works with maintenance and how it can help them.”
The Pipeline Company
Enbridge of Calgary, Alberta, operates the world’s longest crude oil and liquids pipeline system. The company owns and operates Enbridge Pipelines Inc. and a variety of affiliated pipelines in the U.S. and Canada, These systems comprise approximately 13,500 kilometers (8,500 miles) of pipeline, delivering more than 2 million barrels per day of crude oil and liquids.
Enbridge is using IBM’s Maximo EAM system to manage and track the maintenance of that system, including documentation for regulatory compliance. “We’re showing that we’re doing what our operational and maintenance manuals say we should do,” says Tom Reid, Enbridge’s team lead for Maximo services. But his job is bigger than that. He’s also using the Maximo system to help transition to a predictive maintenance model.
"We’re pulling unit run time from our SCADA system,” explains Reid. “We can schedule maintenance based on hours run rather than basing it on time. For example, we have six units on one line. The only time the fifth and sixth units got started up was when we were taking readings. That vibration was not going to be any different than the last time. So now we take a vibration reading on the machine every 700 hours rather than on a fixed time schedule.”
Like Steve Greguske at ImClone, Reid says the benefits of EAM are “soft” right now, but very real. “We are constantly expanding at Embridge. We did a comparison of the amount of equipment in the field now and in the past. We looked at the amount of equipment we had in the field, the operations and maintenance budget and the staffing. What we saw was a drastic increase in the amount of equipment, but the operations and maintenance budget was the same, if not lower, and the number of technicians was the same.”
Is It Worth It?
So is moving past basic asset-tracking CMMS worth all the effort? Western Management’s David Berger delivers his own warning: “You have to analyze to death,” he says. “So few industries really do this. The only one that really does is the airlines because planes will fall out of the sky if they don’t. Just imagine the amount of work that goes into this. What kind of failures? What to monitor? How? Nobody has time to do this analysis, which is why, if you have a good tool, it helps.”
On the other hand, Steve Greguske, Einar Mørk and Tom Reid think investing in that good tool is indeed worth it. Their respective managements agree. But make no mistake. EAM is not a magic bullet. To get to the benefits that drop visibly to the bottom line will a significant investment of time, labor and money.
To see additional online resources visit ControlGlobal.com/service_plant_now.html
Elephant Anatomy
- Reactive maintenance. It’s broken and we have to fix it.
- Preventive maintenance. If we do the following things on schedule, the equipment won’t break—or at least will run well longer.
- Predictive maintenance. The data lets us estimate closely when we actually need to work on this machine to prevent a failure.
- Complex analysis. This step moves us into fine-tuning and optimizing our maintenance to help with decisions about which assets get which kinds of maintenance and how we link operations data to initiatives such as TQM, SPC and Six Sigma to improve overall quality and production capacity.
Types of Predictive Maintenance
- Condition-based monitoring. Use real-time data (run hours, starts and stops, etc.) to indicate when an asset needs maintenance.
- Reliability-centered maintenance. This is an exhaustive process, says Avantis’ Neil Cooper. You must look at every asset and do FMEA failure mode and effect analysis—what could make it fail? what is the effect of failure, both upstream and downstream?—in order to determine the optimum maintenance strategy. Here’s where you can analyze whether it makes more sense to run an asset to failure or—at the other extreme—equip it with full instrumentation and go to advanced condition-based monitoring to prevent it from ever failing.
The Evolution of CMMS/EAM
In the beginning was a data depository, says David Berger of Toronto-based Western Management Consultants. “It was a place to put all your asset information, when it was purchased, its size, the tombstone and transactional data. Then it became a planning and control tool. It was no longer just a bunch of asset records, but we can use it to schedule work. We could use it to record work done and for preventive maintenance. Then we could get more sophisticated around scheduling; connect it with HR and have a record of what people are available to do the work and when they’re available. We got greater sophistication around features and functions. We could schedule by year, by time, by events. We got more functions and other ways to slice and dice the data.
“Then we got greater analysis capability. We could build correlations between certain types of downtime and certain vendors, for example. We started doing analysis as opposed to just reporting. And with better analysis, you can make better decisions. Analysis tools allow you to pinpoint issues and give you the intelligence to make decisions.
“The other area of change is integration. What used to be a simple data dump and report tool starts to creep vertically and horizontally into other areas. Think of shop-floor data collection: PLCs, HMIs, SCADA. [With that you can get] better cooperation between engineering, maintenance and operations.”
To see additional online resources visit ControlGlobal.com/service_plant_now.html
Latest from Safety Instrumented Systems
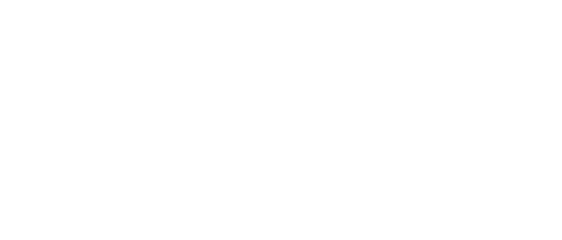
Leaders relevant to this article: